Copper Heaters Improve Fuel Tank Safety on Space Shuttle
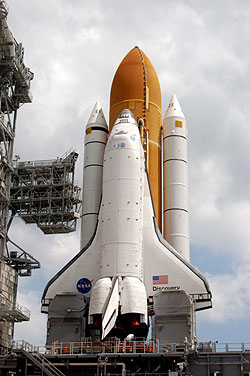
Photo Courtesy of NASA/KSC.
High-resolution version of this photo.
When the Space Shuttle flies again this July – for the first time since the Columbia disaster two years ago – copper will be an important part of two new safety features designed to prevent future accidents.
The stakes are high: All seven Columbia crewmembers died in 2003 when their ship exploded on its return to Earth. Investigators believe the accident was caused by a suitcase-sized piece of exterior foam insulation that broke off from the Exterior Tank (ET) during launch and punctured the shuttle's left wing. Upon re-entry to earth, superheated gases penetrated the wing, causing the shuttle to disintegrate.
Re-evaluating the ET's thermal protection system, which prevents ice and frost from forming on its metal surface prior to launch, was a priority for NASA engineers following Columbia. Frozen condensation could, like the foam, fall off and damage the shuttle's heat-deflecting ceramic tiled exterior during take-off.
One of the new safety measures NASA has implemented for the launch of Discovery this month is the replacement of two foam sections on the shuttle where the ET connects to the spaceship. It was this area where foam broke loose from Columbia and a previous shuttle voyager, Atlantis.
Copper Plates for Heaters
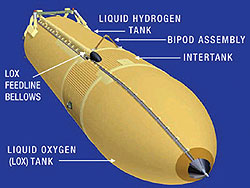
High-resolution version of this photo.
Instead of foam, NASA is using electric heaters installed under key components known as bipod fittings. Four 300-watt cartridge heaters are each placed on a copper plate that is separated from the ET by thermal padding. Copper's superior heat-transfer properties will help distribute the heat to this vital area and prevent ice from forming on the fittings. According to NASA, the heaters will melt any ice formed by condensation from the tank's super-cold cargo – 526,126 gallons of liquid propellant used to fire the shuttle's three main engines.
After extensive testing in wind, vibration, structural, and thermal trials, the bipod heaters are being retrofitted to the shuttle fuel tanks for this and all future space missions. NASA will continue to spray the rest of the fuel tank with insulating foam to keep its contents in their liquid state and to prevent icing.
A close-up of the redesigned bipod fitting that helps attach the External Tank to the shuttle. The old design, left, used a foam ramp to prevent ice from building up on the fitting. Falling foam opened a hole in one of Columbia's wings, leading to the orbiter's breakup on entry. The new design, uses a copper heating element instead of foam to prevent ice buildup. Illustration Courtesy of Lockheed Martin/NASA Michoud.
Copper Heating Belts
Copper is also being used for a belt-like heater for the uppermost bellows (a flexible joint) of the Liquid Oxygen Feedline. This section needs extra protection because it is positioned above the shuttle, and frozen debris falling from it would likely strike the ship. The bellows heater consists of two copper- nickel metal strips about 53 inches long and one-half inch wide.
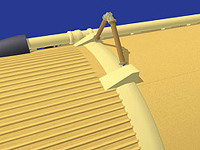
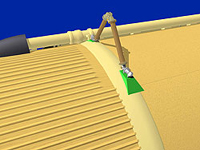
The fastest growing area for copper tubing, however, is for fuel gas. More home builders are installing gas these days, says Rick Schaffer, a representative for Mobile GaThe External Tank is the largest piece of equipment on the shuttle, measuring 15 stories high and weighing over 1.5 million pounds. When the shuttle reaches its optimal velocity, the ET (like the two rocket boosters that fire the vessel into orbit) is jettisoned and falls back to earth. Cu
Resources:
Also in this Issue:
- Copper Comet Impactor: A NASA Success Story
- Copper Heaters Improve Fuel Tank Safety on Space Shuttle