The main function of an injection mold, beside defining a part's shape, is to remove heat from the plastic as quickly as possible. The mold should be thought of as a heat transfer device much like the automobile radiator shown above. The faster the mold can transfer heat out of the molten plastic and solidify it, the faster the mold can be run. Reduced cycle time equates to reduced manufacturing cost. This is where copper alloys outperform other metals used for molds. Copper alloys provide the best combination of high thermal conductivity and hardness for molds used in the plastic industry today. As seen in the Comparison of Mold Alloy Properties Table, hardness and conductivity vary over a range for each alloy system-steel, aluminum or copper. Copper alloys have thermal conductivities 3 to 9 times greater than the commonly used Type 420 stainless steel.
Copper Alloy Molds
Additional Information
- Copper Advantage
- Cooling Prediction of Non-Watered Copper and Steel Mold Cores
- Getting Heat Out of the Mold Where Water Won't Go
- Whirlpool Uses Copper Alloy Mold for Dishwasher Console Part
ANTEC Reports
- Undercutting Mold Performance: Ejection Wear
- Size Does Matter: Mininization Of Gate Wear
- Use Of Copper Alloys To Reduce Mold Condensation Problems
- Impact Of Fines Separation On Reinforced Thermoplastic Regrind
- Comparison Of Various Hard Coatings To Protect Copper Mold Components From Erosive Wear
- Resistance To Erosive Wear By Copper Alloy Mold Components
- Understanding The Source Of Reduced Mechanical Properties In Reinforced Molded Products
Useful Resources
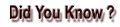
Bronzes are unquestionably the most versatile class of bearing materials, offering a broad range of properties from a wide selection of alloys and compositions.
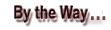
The high thermal conductivity of copper alloys makes them ideal materials for the injection mold sprue bushing and runner bars.
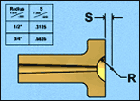
In North America two injection mold nozzle and sprue bushing radii are used, 1/2 and 3/4 inch. To insure proper fit up, the nozzle radius is nominal -.015 inch, while the sprue radius is nominal +. 015 inch, required tolerances to use.
Order Industrial educational & technical publications.
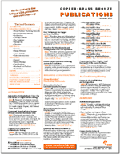
