Copper Air Lines Handle the Pressure
Copper was the choice for engine repair shop after plastic systems fail
Since 1996, S&G Motor Repair has seen plastic come and go in their shop. Paul Yancey, the owner of the certified rebuild shop in Blackfoot, Idaho, installed PVC plastic pipe, Schedule 80, for his compressed air service - a system that operates all of their major equipment in the plant.
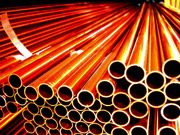
Unfortunately, the plastic system failed after just four years in service, and it was replaced with another plastic pipe system. Five years later, the PVC system failed again. Following this second failed attempt with plastic, Yancey decided it was time to move on to copper.
Copper tubing offers several benefits for mechanical systems including: corrosion resistance, durability, versatility, and workability when installing.
For Yancey, the longevity and workability were what convinced him to switch to copper. He wanted a system that his maintenance crew could install themselves, inexpensively in their downtime at the shop.
"We looked at several other options," Yancey said. "We could have used carbon steel pipe or an extruded aluminum system, but we were looking for something user-friendly, something we could install in-house so we could control costs."
Ultimately, Yancey chose a copper system from Mueller Industries called StreamTECH, which uses an alternative joining method. Its solderless or "flameless" connection system is based on a high-tech structural adhesive that can be ready to pressure test in just three hours.
"Pipe connections continue to evolve," said Copper Development Association (CDA) vice president, Andy Kireta Jr. "Alternative solderless methods provide watertight seals and offer other advantages, too, such as fast assembly times and joint strengths that meet or exceed those of their plastic counterparts."
Other types of solderless systems rely on push-connect or press-connect fittings, which are suitable for most plumbing applications including cold and hot water distribution, hydronic heating and cooling, compressed air, inert gases and fuel gas systems. Joints made using these systems are capable of withstanding the pressure and temperature ranges common to both residential and commercial building systems.
The copper system that Yancey chose met the requirements for a quick-and-easy installation, which was completed by S&G employees in a week and a half.
Aside from the easy installation, there was another reason why the transition to copper was welcomed.
"The schedule 80 PVC air line that was originally installed would literally explode," Yancey explained. "The second PVC system we used was rated for compressed air systems. This second system wasn't rupturing but it developed leaks. The leaks worsened until it blew a big enough hole for a major air leak. We didn't know why it was leaking until we took a closer look."
Yancey noted leaks at the beginning and tail-end of the air line and did some research. He discovered that the PVC system wasn't compatible with certain oils, a fact that wasn't stressed at the time of installation. When the oil from the compression [compressed] air system reacted with the plastic, it would cause the piping to soften and break down to the point where it couldn't hold up to the pressure.
Copper has long been recognized as a reliable metal for HVAC and plumbing applications, and it is no different for this motor shop. The compressed air system at S&G Motor Repair is used in practically all of the day-to-day operations, so a reliable material is a must for the shop.
"We look forward to having the copper system last a long, long time," Yancey said. "Aside from the fast installation and reliable performance, it also looks great."
For more information on the use of solderless fittings for joining copper tube, visit the CDA website. Cu