Carolina Bronze: Sculptural Puzzle Solving
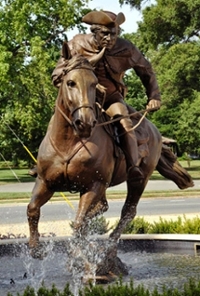
Sculptor Ed Walker dabbled in a lot of experimental materials before developing an affinity for working with bronze.
“It’s a lasting material,” he says, recalling a time when bronze proved itself. “It has stood the test of time and people trust in it. During the ‘60s and ‘70s, a lot of sculpture was experimental and some of it didn’t hold up and some did."
Aside from his own work, the Seagrove, North Carolina-based artist’s 25 year-old business, Carolina Bronze, depends on it. “We specialize in fine arts bronze casting and fabrication,” says Edward’s wife, Melissa, who is a painter and printmaker in addition to being the V.P. and marketing director of the business. Their clientele consists of artists, architects, museums and non-profits. “Artists would be our biggest clientele,” says Melissa, particularly those who hail from the East Coast.
“Our best known artist would be Chas Fagan who is known for his presidential portraits, well-known politicians and historical sculptures. He is probably the one we do the most work for. We have a lot of other really talented sculptors.”
The fine arts foundry specializes in casting sculptures of all sizes ranging from tabletop size to monumental, with the primary bulk of their work evolved around historical sculptures, many life-size, and memorials, such as fallen firefighter memorials.
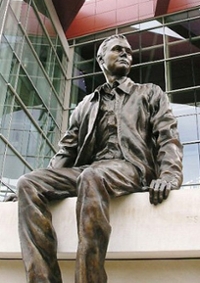
“We have done a number of sculptures of Ronald Reagan, in addition to a number of other presidents – George Bush Senior and Junior,” Melissa says. The process of making a casting is one that is collaborative. “The artist will typically bring us a small model in an oil-based clay,” Melissa says. “We will either mold that directly or if they want it enlarged, we have the ability to scan the model and enlarge it using digital enlargement methods.”
Once the model is enlarged in high-density foam carved on Carolina Bronze’s CNC router, it’s time for the artist to make any final modifications. “The artist will come in and add clay to the foam armature and then we will mold and cast using the traditional lost-wax process,” Melissa says. Their staff of 16 wears many hats in some cases. “For one life-size work, the whole staff gets involved at some point,” she says.
Architects seeking to work with Carolina Bronze are typically in need of replication.
“If there are architectural pieces on a building, we can do that,” Melissa says, of their ability to replicate. “A number of years ago in Washington, D.C., in the National Archives Building -- where they have a bronze rail that goes around where the documents are displayed -- they sent us a section of a bronze that had to be recast.” In some cases Ed is commissioned to create a sculpture from start to finish for a client. “We finished a large fallen fire fighter memorial for the city of Wilmington, North Carolina,” Melissa says. “Sometimes we have people come in and they are not an artist, but work for a governmental agency or a military person and we either find an artist to do the work for them or we do it in house.”
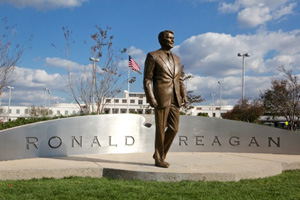
Carolina Bronze’s high-detailed scanner sets their foundry apart from others.
“We pride ourselves in the amount of detail we get in our enlargements,” Melissa says. The quality of their castings is paramount, so they spend a lot of time working with the artist. “They can actually come to our facility and work on large pieces here. We can help artists with getting the work done if they need extra hands. We have a number of trained artists working here who have a good eye for detail.”
The facility has a section dedicated to making rubber molds and working on waxes.
“Then we use a ceramic shell process to coat the wax pieces,” Melissa says. “From there that goes into the foundry and then it is cast, usually in bronze, occasionally in aluminum.”
Next, it goes into the metal finishing part of the building.
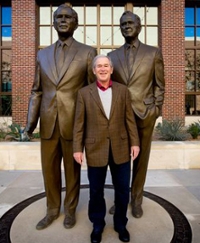
“The different pieces of the casting are welded together,” she says. “All of the seams are ground and chased until you can’t see where the different pieces have been fit together. Patina is then added after all of the metal work has been finished.”
The foundry typically completes a small-scale sculpture for a client in one month and a life-size figure takes approximately two to three months to complete. After completion they will crate a piece up and deliver it. They also offer complete installation of a sculpture anywhere in the country. Despite the foundry being located in a town with only one traffic light, you can find their work all over the world. “Dubai, London, Aruba,” Melissa says, of a few of the many locations where their sculptural work is located.
Carolina Bronze also has sand casting equipment to be put to use when requested by a client who may be in need of some short run manufacturing. They are capable of making up to 500 pieces of the same item.
“It is a different kind of process than the ceramic lost wax,” Melissa says. “We can cast pieces using the sand molding process which is a more direct process than the lost wax.”
The sand molding process works best for less detailed, manufactured objects. They are currently using the sand casting process for a project for a trolley car company in California.
“They are refurbishing old trolley cars and instead of using the overhead wires, they have the hydrogen batteries,” she says. “We are making cast bronze and aluminum pieces for hardware on the car.”
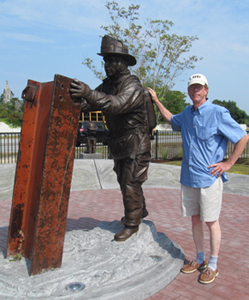
The foundry, located on 55 acres of timberland has a showroom. In the next year or two, they plan to infuse samples of their sculptural work with their vast amount of acreage.
“Plans are in the works to add a large pond and a sculpture garden that goes around the pond on a path,” Melissa says.
Ed describes some of the greatest satisfaction he gets through his work. “In our consumerist society we are bucking the trend in that we are manufacturing things that are meant to last forever,” he says. He also enjoys the problem solving process for sculptors and others who come to them with a concept of what they want. He thrives on the challenges posed by his work.
“We create new puzzles to solve everyday we come to work,” Ed says. “So far we haven’t found one we couldn’t beat.”
Resources:
Also in this Issue:
- Carolina Bronze: Sculptural Puzzle Solving
- Patina Studio: Enhancing the Natural Beauty of Copper through Science
- Teaching the Touch of Copper and Brass
- Unique Copper Weathervanes Crafted from Old World Metalsmithing
- BMA Acquires Monumental Magritte Bronze