The Handcrafted Legacy of Lawson Horns Lives On

Photograph courtesy of Kendall Betts
When Walter Lawson, a second chair horn player in the Baltimore Symphony Orchestra, started a small musical instrument repair shop in his garage in Boonseboro, MD, he had no idea where this path would lead. Lawson had a successful career as a professional horn player and taught in the Baltimore area, but after suffering a career-ending injury in 1979, he began dedicating his time to improving the horn from an engineering perspective, and Lawson Horns was born.
After years of repairing musical instruments, Lawson had learned a lot about the craftsmanship that went into making a great horn, and began manufacturing his own design in 1982 with the assistance of his three sons, Paul, Duane and Bruce. Paul was a machinist who built valves and spun bells, Duane made parts and polished/lacquered the instruments and Bruce acted as acoustician, making sure the musical devices had the perfect sound, intonation and response. Lawson's endeavors spanned decades of work and included commissions on various effects of horn playing by institutions like the International Horn Society.
Using connections in the metallurgical world, Lawson's extensive experimentation with heat treatments and his unique pattern annealing process on numerous metals enhanced sound quality in all dynamic ranges. In the 1970s and 1980s, Lawson performed tests on hardness of the bell flares and the different effects bell alloys produced. He also received advice from Thomas FitzMaurice, a metallurgical engineer at Anaconda Brass Company in Waterbury, CT, and, as a result, introduced Ambronze. This strong, workable metal had been used in architecture but was never before used on musical instruments.
With the newest technology at his fingertips, Lawson began using computer aided drafting and audio sampling to further develop acoustic tapers.
Lawson’s research paid off and he began receiving rave reviews from musicians around the world. In 1999, The Baltimore Sun credited the company for creating some of the world's finest French horns.
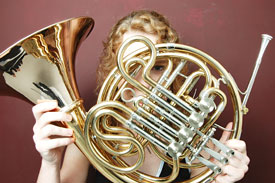
Photograph courtesy of Picture Perfect Studios
After 50 years of service and just before his death in 2007, Lawson sold the company to life-long friend and former student, Kendall Betts, also a professional horn player. The business was then relocated to New Hampshire.
"I was often referred to as Lawson's fourth son," says Betts. "I wanted to preserve the old-fashioned, made-from-scratch aspect with only slight improvements when necessary. Today, our materials come from various suppliers: sheet from Anaconda, rod from Enco or MSC and tube from H and H Tubing in Michigan."
"Most horns are made from red brass, Ambronze or nickel silver/nickel bronze but yellow brass is available. This provides normal professional playing for 30 years or more before requiring an overhaul to the valves. Tails and flares are still cut from sheets of metal in a pattern, then formed in several stages. Valve and mouthpiece parts are now made on CNC lathes which gives us 100% precision in tolerances. Tapered and straight parts and slide crooks are still done by hand except we now hone the straight tubes by machine for greater accuracy. Our tapers, developed by Walter and Bruce Lawson, are unique in the industry. Bells are spun in the traditional method. We've created an engraving pattern at the bell tail. Personal quality control is the key so we have an advantage over factory made instruments. Bruce is still a consultant on new designs," reports Betts.
In the 1960s, Lawson created a French horn mouthpiece kit where four parts of different dimensions could be screwed together for testing more than 12,000 possible combinations. The mouthpiece is especially important to players because it affects changes in sound and playing characteristics.
"Many conservatory students and major professionals designed custom mouthpieces using the kits made by Lawson," explains Betts, for whom one was also made. "Copies went to performers like the late, great John Barrows. During this time, contours and rim materials were studied in collaboration with hornist/composer Don Haddad. Today, brass or plastic mouthpieces can be turned on a lathe from any material machinable to dimensions of very close tolerances."
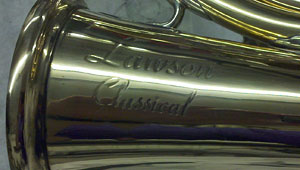
Photograph courtesy of Lawson Horns
In 1985, Betts, then Principal Horn of the Minnesota Orchestra, and IBM Executive/amateur hornist Tom Cowan did an extensive computer-aided study of some 200 mouthpieces. The data pointed to certain design elements that influenced efficiency and sound. Bruce Lawson continued the studies doing extensive acoustical research and designed two cups whose unique shapes resulted in optimum efficiency in tone production and moving the sound through the instrument. Four rim contours were developed as well, with eleven inside diameters. Since 1987, the Lawson mouthpieces have been used worldwide and are considered by many to be the best available.
According to Betts, "We can rebuild, restore, and customize to cover the gamut of performance requirements. There are four types of leadpipes which can be bent exactly to fit using photocopies of your instrument from one of our hundreds of existing bending blocks. We also offer five construction alloys - yellow brass, red brass, nickel silver and we are the only makers of Ambronze bells. Another alloy that is exclusive with us is nickel bronze, a nickel silver alloy with no zinc, which is unique because it is closest to the German nickel silver used by the famous Edward Kruspe before WWII."
"We are proud to offer the extraordinary, acoustically superior, high-quality Lawson horns that are used by professionals, amateurs and students worldwide,” he says. “We offer two models of full double horns, the Fourier and the Classical, plus two descant models (specialized horns for high horn playing) with matching acoustics to the doubles. We can also make single Bb horns in various valve configurations. The Fourier model is our version of a large bore horn, the Classical is our version of a medium bore horn. Bruce and I are currently working on a new design for a triple horn (an instrument combining the acoustics of a double and a descant) and I hope to have a prototype built soon," states Betts.
"Well-known horn soloist/conductor Barry Tuckwell, who was a neighbor and close friend of Lawson, used a Lawson descant for decades due to its superior response and sound," mentions Betts. "Lawson horns can be found in many major orchestras and top military bands including the Los Angeles Philharmonic, National Symphony, Minnesota Orchestra, Atlanta Symphony, Dallas Symphony, the US Marine Band and the US Army Field Band. We are currently building a matched set of four Fouriers for the 1st Marine Division Band at Camp Pendleton, CA."
Resources:
Also in this Issue:
- The Handcrafted Legacy of Lawson Horns Lives On
- Super Sax Back
- Zenfire Guitar Picks: Exploring the Unique Sounds of Copper
- Gilded Days: Antique Sheet Music Finetuned by Copper
- New Works by April Wood on View at Austin's AMOA-Arthouse