Kiln Design: Old School in the Natural World
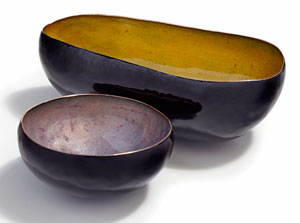
Photograph courtesy of Kiln Design Studio
Kiln Design copper enamelist artists Jay Leritz and Elissa Ehlin kick it old school. Together, they keep the dying art of raising metal and the true aesthetic of copper alive in Brooklyn and beyond.
Leritz owned an art metal fabrication furniture design company in California for years. At the time, he bought preformed enameled copper for the business. Randomly, he spotted a night course offered at the local community college and decided to learn how to do it himself.
"I got hooked," says Leritz. "Then I met my wife. We started doing it together and became addicted."
Soon the couple spent all of their spare time creating decorative houseware from enameled copper, and trying to figure out ways to sell it.
Today, Kiln Design does everything by hand, without the use of industrialized processes in their Brooklyn, NY studio. Sometimes they form the copper in a hydraulic press. Sometimes they spin the copper, creating three-dimensional symmetrical objects, like bowls and plates. Most often, they incorporate the old fashioned silversmithing technique of raising. Using a hammer and stake, Leritz stretches and pulls flat metal into whatever shapes necessary.
"It's a dying art to do it by hand," Leritz told me.
Enameling comes next. Leritz and Ehlin heat glass to 1500 degrees in a kiln, so it becomes a glaze. Then they can melt the glass onto the surface of the metal. The wrong metal - like stainless steel, for instance - can separate from the glass. Copper is the best metal for this process because its rate of expansion is so close to that of glass.
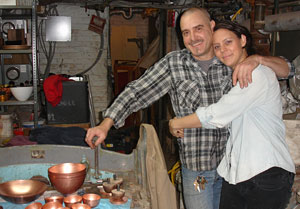
Photograph by Paul David
Prone to oxidizing and tarnishing, glass provides the perfect finishing for copper while maintaining its natural luster. Leritz and Ehlin play with opaque and transparent glass, as well as different colors. The combinations of colored glass and colored copper are endless.
Leritz also plays with shape and design. He applies a ball peen texture with a hammer or embosses a pattern onto the copper. This adds to the dimension and depth of a piece.
From this overall process, the couple creates jewelry, bowls, plates, and sculpture. Bowls and plates are cooking and serving friendly - but because of their fragility, customers often purchase them for decorative means.
What really makes Kiln Design unique is the hand spinning, which is almost obsolete.
"Other artists work with preformed bowls that they buy," Leritz explains. "We can make our own shapes and find the best process."
The couple makes custom pieces when parts aren't available - from chandeliers to lamps and antique motorcycle parts.
Scraps of copper do not go to waste. Most often, that's what inspires Leritz and Ehlin to keep working.
"If I make a mistake, or burn something, then I'll realize it has a neat effect," says Leritz. "I think about it until I can come up with something to use it for," says Leritz.
From leftover pieces of copper, they've fashioned unique jewelry, giant bugs, sea creatures.
When asked to describe the inspiration for their work, Leritz describes it as an environmental concern - both ecological and aesthetic.
Kiln Design creates objects that are intended to endure-not be thrown away. This eco- friendly mindset carries over into how they operate the studio. They avoid working with toxic chemical and processes and they don't create waste.
They also appreciate that each piece "has its own fingerprint, creating one-of-a-kind pieces.
"We make a ring, and make it the same way every time, but the process allows it to look different every time," he explains. "Just like how each person is unique, each ring is unique."
Resources:
Also in this Issue:
- A Reverence for Copper and the Slower Melt of Time
- Robert Arneson: Self-Portraits in Bronze
- Kiln Design: Old School in the Natural World
- Studio 78: Artistic And Functional Hand Painted Furniture Enhanced with Copper
- Inspired by the Past: The Copper Art of Annie Keifert