This History of Intaglio
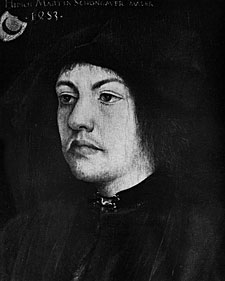
Photograph courtesy of Wikimedia Commons
As early as 5,000 B.C., cultures such as the Sumerians created jewelry by carving designs into metals like gold, silver and copper. In the middle ages, goldsmiths engraved metalworks to decorate armor, musical instruments and religious objects. When artist Martin Schongauer exploited copper engraving in the 1430s, a new form of printmaking resulted using the intaglio techniques.
The process began with an engraver's block, which was used to hold or turn a copper plate as Schongauer cut fine lines into it using a burin or square tool-steeled rod sharpened diagonally at one end. The prominent corner was an effective and controllable cutting edge. Copper was the preferred metal because it was strong yet easily worked and did not rust.
Printer inks were then rubbed over it and wiped with tarlatan (starched cheesecloth) leaving ink only within the cuts. It was then run through a press where paper absorbed the ink in the small reservoirs created by the grooves.
The mezzotint matrix was worked with an intaglio rocker to have a consistent tooth to hold the ink. Copper plates were perfect for this process because it was not so hard that the rocker would be damaged but still offered excellent retention of detail considering the pressures required during printing.
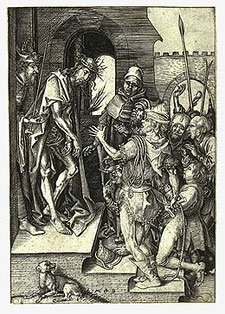
Photograph courtesy of Wikimedia Commons
By the 19th century, engraving became used mainly for illustrations. Etching was an easier process for artists to use and machines helped speed up the printmaking process. Etching also used copper plates and depressed the images below the metal surface. A ground (acid resist coating) was hardened by heating with a candle, then cooled. The design was scraped into the ground to expose the metal and the plate was submerged in acid solution to the desired depth and width. Depressed areas were filled with ink and non-printing parts were wiped clean. Dampened paper on top of the plate passed under considerable pressure through the printing press and the image transferred from plate to paper.
In her book, Etching, Engraving, Ruth Leaf states that copper used for etching should be cold-rolled 16- or 18-gauge and hard ground rather than soft so you can get very fine lines. You can polish the backs of old copper plates if you can find them. Or, they can be purchased with an acid resistant coating on the back surface.
Intaglio aquatints offer tone gradations in color. The copper plate is dusted with resin and heated. The grains melted and produced an irregular pattern surrounding the resin patches. Acid applied to etch only the spaces around this resin resulted in an overall texture. Then watercolor in added.
Since the advent of photography, intaglio is less common, but still used by artists that want to create a true one-of-a-kind print. Modern plates for printing money, checks, bonds and other securitysensitive papers display such a high level of microscopic detail that it can't be recreated or scanned. More than one hand engraver will work on the same plate, too, making it impossible to duplicate all engraving on any document.
Also in this Issue:
- Lower East Side Printshop: Working Side by Side with the Artist Community
- Evan Summer: The Fine Art of Intaglio
- Quincy Pond Print Works: Past Lives Brought into Focus
- New Show at Washington Printmakers Gallery Features Work by the New York Society of Etchers
- This History of Intaglio