John S. Brana Designs: Adding a New Sheen to Contemporary Jewelry
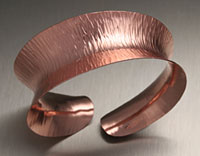
Photograph courtesy of John S. Brana
Out of the traditionalists' preference for 24k, a new type of jewelry artist has emerged, where the designs are worth their weight in gold, but not necessarily made from the metal itself. Designers like John S. Brana are bringing a new sheen to the contemporary jewelry market by giving copper and bronze a prominent name among high end jewelry collectors.
Brana's jewelry can be found dangling around the necks, wrists and ears of both actors, models, and everyday people, but no two pieces are alike. Inspired by the charm of San Francisco's most characteristic neighborhoods, each piece is handcrafted, with price ranges from $30 to $20,000.
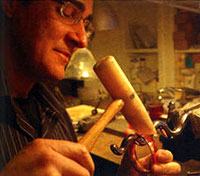
Photograph courtesy of John S. Brana
Brana loves to feature nontraditional metals, his most recent collection thrusting copper and aluminum in the spotlight. His designs are flirtatious and intricate, often with elegant geometric textural elements and clean curves. His new line, named after the South of Market district, "SoMa," is inspired by the curved angles of the architecture and the "opulent gold rush period" of its heyday.
Not many other jewelry designers value the unique abilities of copper the way Brana does. In a contemporary jewelry industry founded on the classic value of semi-precious metals and gemstones, his choice of materials like copper, bronze and aluminum is giving a new sheen to the high end jewelry industry.
"I didn't want to pursue being a goldsmith," Brana explains. "Jewelry customers think of copper in the dark brown oxidized way-like an old penny." But many of Brana's copper and bronze pieces are exquisitely polished, breaking the customer's previously held belief about what copper can be and how it is worn. "When they see my red brass pieces, made from 85% copper and 15% zinc, they think it looks like 14k gold!"
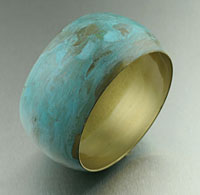
Photograph courtesy of John S. Brana
Brana's charmed life as a designer had not been his original career choice. Before starting up John S. Brana Designs in 2006, he had been a VP of Finance at Charles Schwab, when a series of events compelled him to turn a 180. The financial services industry that had coasted high on the dot-com boom came barreling down after the recession that echoed from tower collapses of 9/11. Surviving three rounds of cuts from his company, it was a personal crisis that brought Brana to his creative side.
"My father developed lung cancer, and I came to the realization that I no longer wanted to pursue a corporate agenda," he recalls.
One day on television he caught a Carol Duvall demonstration on Precious Metal Clay-a clay form that can be molded into any shape and fired to become pure silver. Intrigued by the process that would marry his interest in ceramics with the new pursuit of wearable art, he began experimenting with jewelry design. Though he soon abandoned PMC as a "hobbyist medium," it ushered him into the realm of the professionals. From there he went on to perfect his skills in melt casting and fabrication, and hasn't looked back since.
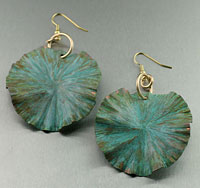
Photograph courtesy of John S. Brana
The designs speak for themselves with a perfect combination of allure and a price range for everyone. One of the most popular of his designs is a flower or leaf shape, part of a chasing and folding process with the malleable copper. When asked how he gets the realistic representation of a leaf's veining he is quick to point out that none of it is impressed from an original. "It's all chased by hand," he explains, a similar process as engraving aimed to create a decoration. Due to copper's elasticity, designs can be folded to create the shape of leaves or petals: "If you fold the metal like you fold a taco, you've got a folded side and two edges. If you chase on the edge you can expand the piece in a crescent shape to get a leaf pattern."
Brana also uses organic techniques to bring about the natural patination processes, resulting in earrings and pendants of turquoise, magenta, mustard and cauliflower blue with a notable texture.
"There's probably 300 different colors that you can apply to copper," he says, referring to his Muir Woods collection of patinated pendants and earrings. That is what is special about copper, he says. "You can't do that with any other metal."
To make his patinas, Brana will moisten the copper with ammonia, vinegar or other chemicals and bury it in sawdust, soil or tobacco for three weeks to age. "I like that you get a very in-depth texture," he says, because all copper that's patinated goes through a sandblasting process so that the chemicals more easily adhere to the metal.
Everything that Brana sells is handmade, chased or patinated by him, singularly working long hours in the studio. But his bronze rings are truly one-of-a-kind-hand-sculpted precisely to the size, color and weight of a particular gemstone. Brana employs the lost-wax casting method to create the basic bronze ring, casting about 40 at a time. Then each gemstone is individually set, and the ring carefully hand-polished up to 45 minutes before it's completed.
"I think the strength of my design company is that it hasn't followed a traditional route," says Brana. "People like my jewelry not because of the semi-precious metals, but because of the interesting original designs."
Resources:
Also in this Issue:
- John S. Brana Designs: Adding a New Sheen to Contemporary Jewelry
- Arizona Copper: Home of Copper Ken
- Kindred Spirit Designs: Creating Rainbows on Copper
- The Beautiful History of Capital Copper
- Spirit and Form: Michele Oka Doner at Frederik Meijer Gardens & Sculpture Park