The Art and History of Brass Musical Instruments
Through the ages, copper and brass instruments have been used in an assortment of capacities, and are still popular today throughout the world. In the famous Broadway Show The Music Man, its memorable tune "76 Trombones" by Robert Meredith Willson is belted out in a parade with copper and brass musical instruments gleaming like a beautiful sea of copper.
But, what comprises a brass instrument? Anthony Baines, author of European & American Musical Instruments, states that brass instruments are defined as instruments that produce a tone by vibration of the lips as the player blows into a tubular resonator. Also known as labrosones, brass instruments are constructed of brass and other corrosion resistant, easy-to-fabricate copper alloys.
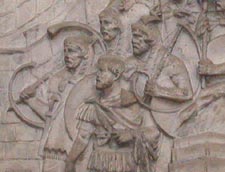
Photograph courtesy of Dan Pocklington
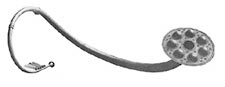
Photograph courtesy of Dieter A. Bachmann
The actual description of brass instruments are dependent on the overtone series first studied and analyzed by the Greek philosopher Pythagoras. A string or vibrating air column in the case of a brass instrument will tend to vibrate at certain frequencies based on the length of the string or tube. The fundamental pitch is the lowest natural note with other possible notes one octave above the fundamental, followed by a perfect fifth, fourth and up. Modern brass instruments usually alter the length of the tubing through valves, including the slide still used by today's trombonists. The Roman Tuba, Lituus and Buccina, and other early brass instruments were made of bronze combined with animal horns, like the Scandinavian lur, and the Roman cornu.
Getzen Brass Instruments: Then and Now
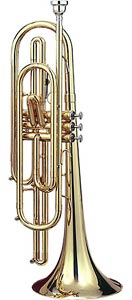
Photograph by Getzen, Co.
Musical instruments are a long-standing family tradition of the Getzen family that began in 1939 in a converted dairy barn behind their family home in Elkhorn, Wisconsin. Three employees concentrated on band instrument repair and they produced their first trombones in 1946. They're now producers of world-class trumpets, cornets, fluegelhorns, and trombones.
"Now, we make approximately 15,000 instruments a year and we send them all over the world," says Brett Getzen, Special Projects Manager and great-grandson of the founder Anthony James Getzen. "Tony originally worked for another band instrument manufacturer but, in 1939, branched out to start his own company. When he began building horns in the late 1940's, he used a copper trim. Copper has also been used for quite a while to create resonant bells. We have two kinds of copper bells - one made here from copper tubing for the bell and the other kind is electroplated. They take a steel mandrel and plate copper onto that until it's thick enough to break away - and then you have a bell blank. When you create a bell for a trumpet you spin it on a lathe to get the tapered look, and the blank looks like a bell that, at that point, isn't the right size - yet. At that time in the production, it can become several things. One example is several different bells on trumpets. The rate of paper to the bell, the size of the throat and flare determines how the horn sounds and plays, so according to what you're trying to achieve, we make these copper blanks into different bells, depending on how we spin them. The largest copper instrument we have is the trumpet bell. We also use copper in our plating and use copper plate as a basecoat before we do a silver plating. We put a thick layer of copper on before we put the silver on because the copper makes the silver more illustrious and provides a distinguished tone, as well."
According to Getzen, their copper sheet and tubing comes from Central Steel and Wire, or Copper and Brass Sales. Because they use a small amount, they don't purchase it directly from a mill, to make their copper and brass hand-made pieces. It amazes people because there are probably four or five pounds of brass and nickel to build a trumpet and most of their costs are for hand labor.
"We have basic models that are produced the same and models that are more customized or higher optimized that customers specifically order," explains Getzen. "We have approximately 97 employees and the majority make the instruments. Several actually play the instrument, therefore each instrument is 'play tested' before it goes out."
Many famous musicians had Getzen instruments by their side when they got their start, and continue to use them today.
"Doc Severinsen played our horn for years, Kiku Collins, the trumpet player for Beyonce plays our trumpet, and Joe Alessi, the principal trombone player for the New York Philharmonic, also plays our instruments," adds Getzen. " Other musicians and bands that use our instruments include trumpet players Rick Braun, Johnny Brit, Mike Vax and Christian Scott. The band, Reel Big Fish's, trombone player, Dan Regan plays a Getzen as does the trombone player from Less Than Jake."
Getzen also thinks that brass instruments are they're about to make another revival into the mainstream music world once again.
"It's one of those things like in the 30's and 40's when brass instruments were huge, then they went out, and now this resurgence is happening with swing music," he says. "Even jazz is making a bigger comeback."
Upholding the Tradition of Past Brass Masters
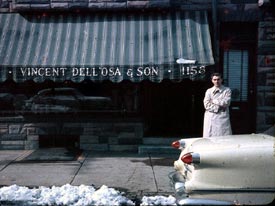
Photograph courtesy of www.hornmouthpiece.com
Fixing copper and brass instruments is an art passed down in generations. Vincent Dell'Osa, Jr., well-known as one of the last of the brass masters in Philadelphia, owned a repair shop in South Philadelphia and fixed brass instruments for members of the Philadelphia Orchestra, the Symphony Orchestra in Italy, Nashville Symphony, musicians across the USA, Canada and South Africa, as well as local musicians who played with the big bands of Harry James, Benny Goodman or Tommy Dorsey. He was taught by his father, Vincent Dell'Osa, Sr., who apprenticed from age ten in Torino di Sangro, a town in Italy. When the elder Dell'Osa arrived in Philadelphia, in 1912, he worked for RCA Victor by day, and utilized his talent of working with metal instruments at night. He had eight styles of mouthpieces and Duke Ellington, Lionel Hampton and other prestigious musicians used them. His knowledge was passed on to his son.
"I was in the repair business for 47 years and finally retired in 1993, but I still get calls," says Dell'Osa, Jr. "In those days, trumpets, trombones, baritones and tubas were mainly brass, but occasionally they'd put a copper bell on a trumpet, making it two-tones. Sometimes they had nickel silver trimmings, but some companies tried to be more flashy with copper bells. I didn't make the instruments I fixed them. I removed dents, and used metal rods for dents deep inside the instruments. Some of those rods were created by my father, using the furnace in our basement. Other times, the instruments had holes from wear and tear so I'd create patches to fit that spot. I tried to make it look artistic in such a fashion that it would be noticeable, but, on the other hand, you'd have to look twice to see if it was a patch."
According to Dell'Osa Jr., sometimes called, "Dr. Dell'Osa", a Civil War buff once arrived at his shop carrying a bugle with a missing valve, asking for help. Emergency calls in the middle of the night from musicians with broken brass/copper instruments were a normal occurrence and part of the job.
Anderson Silver Plating Company, in Elkhart, Indiana, is also a second-generation company who produces copper musical instruments. They offer silver, 24- karat gold, nickel and stainless nickel and can arrange for lacquer finishes, as well as like-new condition for any horn. They also provide a variety of services beyond musical instrument plating and renovation that include military and aerospace specification electroplating in copper, gold, nickel, and tin nickel.
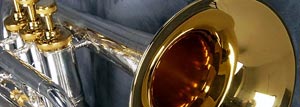
Photograph courtesy of Anderson Silver Plating Co.
"In our plating, in most cases, we don't put silver directly on the base metal. It's preceded by an intermediate plate and we use copper for this," says Mike Anderson, owner. "The intermediate plate is called a strike just like the primer coat in painting. I purchase it from Univertical, a company in Detroit, and then, because we have an electroplating operation where everything has to be hooked up electrically, a lot of our parts are tied up with copper wire and tied to a plating rack. The rack is moved with lots of copper alloy parts - either brass or nickel silver - hanging from it. We also do electroforming, where we have a tank of high speed copper and put a stainless steel mandrel in the bath, then plate a copper shell on it, pull the shell off, and that is our product. That's how we create trumpet and trombone bells. We sublet the repairs although we refit pistons (the valves on trumpets) and other brass wind instruments from a trumpet to a sousaphone. The pistons wear and we have to hone the piston and cylinder to make up the distance in diameter with copper plating."
Resources:
Also in this Issue:
- The Art and History of Brass Musical Instruments
- Maiden Foundry: A Successful Artist-Run Foundry Piloted by Michael Maiden
- The Legend of the Moscow Mule: The Copper Cup that Could
- Steel by Day, Copper by Night: Outside Folk Artist Dave Nally
- MIA Purchases Rare Bronze Masterpiece of African Sculpture