Pre-Mixes
Copper, which has been used for many years to modify the properties of steels and cast irons, is receiving increasing attention as an alloying element in iron-base P/M parts. These parts can be produced by pressing and sintering mixed elemental powders. Carbon, in the form of graphite, is frequently used to produce steels. Control of dimensions during sintering and optimum mechanical properties are achieved by adjusting the iron-copper or iron-copper-graphite composition. Prealloyed powder obtained by atomizing a suitable iron or steel composition can also be used to produce P/M parts, to which metallic copper can be added by mixing. Premixes of iron and copper, with or without graphite, are made by simple blending. These premixes can be fabricated to produce a wide variety of density and strength levels by conventional pressing and sintering. A practical maximum pressure of 90-112 ksi (621-772 MPa) for iron-copper premixes without graphite yields a strength range of 40-50 ksi (276-344 MPa) and a density of 6.2-6.4 g/mm 2. With graphite under the same pressing conditions, strength levels of 75 ksi (517 MPa) can be achieved. The properties of iron-base P/M parts containing carbon can be enhanced by heat treatments such as those used for conventional irons and steels.
The properties of iron-copper parts produced from premixed powders are influenced by the type of iron powder. As shown in Figure 8, there can be considerable variation in the strength properties and dimensional changes in P/M parts produced with a constant copper content depending on the type of iron powder used.
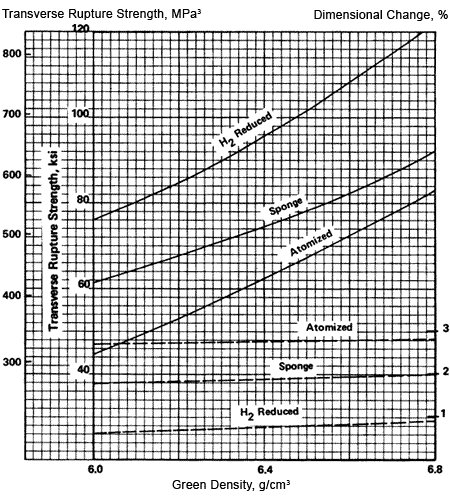
Source: P.W. Taubenblat, "Importance of Copper in Powder Metallurgy," Int. J. Powder Met. & Powder Technology 10:169 (July 1974).
Typical mechanical properties of a series of iron-copper-carbon P/M compacts produced from premixed powders are given in Table 5. The effect of carbon on the as-sintered compacts and the property improvements obtainable by heat treatment are apparent.
Nominal Composition | Condition | Sintered Density g/cm 3 | Tensile ksi | Strength MPa | Yield ksi | Strength MPa | Elongation % in 1 in. | Rockwell Hardness |
---|---|---|---|---|---|---|---|---|
Cu 1.5-3.9 | As sintered | 6.6 | 30 | 207 | 21 | 145 | 4 | B15 |
C 0.3 max | As sintered | 7.0 | 37 | 255 | 23 | 159 | 7 | B30 |
Cu 1.5-3.9 | As sintered | 6.6 | 50 | 345 | 38 | 262 | 1.5 | B70 |
C 0.3-0.6* | Heat treated | 6.6 | 85 | 586 | 81 | 558 | 0.5 | C30 |
As sintered | 7.0 | 62 | 428 | 45 | 310 | 3.0 | B80 | |
Heat treated | 7.0 | 100 | 690 | 95 | 655 | 0.5 | C35 | |
Cu 1.5-3.9 | As sintered | 6.6 | 60 | 414 | 48 | 331 | 1.0 | B70 |
C 0.6-1.0* | Heat treated | 6.6 | 80 | 552 | — | — | 0.5 | C35 |
As sintered | 7.0 | 80 | 552 | 57 | 393 | 1.5 | B80 | |
Heat treated | 7.0 | 100 | 690 | 95 | 655 | 0.5 | C40 | |
*Combined Source: Metal Powder Industries Federation data. |
Premixes of iron-copper and of iron-copper-carbon (graphite) are in use in an increasing number of applications. In wide use is an alloy containing about 2% copper and 0.7% carbon. This alloy is in use in automotive applications such as camshaft drive sprockets, valve rocker arms, lifter parts and oil pump gears. It is used also in chain saw engine connecting rods, differential gears for garden tractors and piston rings for small-bore engines and many similar applications.
To cite a few other examples: A low-carbon copper P/M steel is used for a 16-mm projector sprocket. A similar steel is used for the eccentric for an automatic dryer belt adjustment. A cam for a business machine, an application requiring high strength and impact resistance together with sufficient porosity for oil impregnation, was produced from a 2% copper-0.6% carbon steel at a density of 6.4 g/cm 3. Cable grips with teeth sufficiently hard to bite into high-strength alloy steel cables on a power transmission line support were produced from a similar steel at a minimum density of 6.4 g/cm 3 which was carbonitrided to achieve the required hardness.
Back to TopInfiltrated Parts
Iron-base P/M parts can be infiltrated with copper or a copper alloy by placing slugs of the infiltrant (which has a lower melting point than the porous body) on the compact prior to sintering. Upon melting, the infiltrant is completely absorbed as a liquid into the pores by capillary action to produce a component with a composite structure. The resulting properties generally depend upon the metals which constitute the structure of the infiltrated part and the manner and proportion in which they are combined.
Infiltration has a number of advantages. It increases density with a resulting improvement in mechanical properties, improves corrosion resistance by closing pores, and improves machinability and brazability. It is possible to achieve tensile strengths in the range 70-90 ksi (482-621 MPa) in porous iron bodies infiltrated with 15% to 25% copper.
Erosion of the porous iron body is a major problem with infiltration. The effect is greatest with pure copper and can be minimized by using a copper-iron alloy to which other elements, such as manganese, nickel and aluminum, have been added to lower the melting point and act as deoxidants during infiltration. The properties of the infiltrated part are influenced by the type of iron powder, infiltrant type and composition, furnace conditions, and any heat treatment performed after infiltration.
Table 6 indicates the properties obtainable in infiltrated iron parts with and without carbon additions. The presence of carbon results in a considerable increase in strength, even in the as-sintered condition, but at a reduction in ductility. Ductility in the carbon-free alloy can be improved greatly by normalizing, and there is little reduction in strength. Heat treatment of the alloy containing carbon produces parts with excellent strength accompanied by ductility that is superior to that obtained in premixed material of similar carbon content.
Carbon % | Heat Treatment | Sintered Density g/cm 3 | Tensile ksi | Strength MPa | Reduction of Area % | Elongation % in 1 in. | Rockwell Hardness | Izod Impact ft-lb |
---|---|---|---|---|---|---|---|---|
0 | None | 8.02 | 68 | 469 | 13 | 8 | B74 | 5.0 |
1* | None | 7.96 | 105 | 724 | 4.8 | 4 | B93 | 1.0 |
0 | Norm 1800 F (980 C); 950 F (510 C), 4 hr |
7.95 | 60 | 414 | 20.5 | 18 | B71 | 11.3 |
0 | Norm 1800 F (980 C); 950 F (510 C), 4 hr; 1300 F (700 C) 2 hr |
8.01 | 58 | 400 | 44.3 | 25 | B70 | 14.9 |
1* | Norm 1800 F (980 C); 1550 F (840 C), w.q. |
7.98 | 159 | 1096 | 3.7 | 3.2 | B110 | 1.0 |
1* | Norm 1800 F (980 C); 1550 F (840 C), w.q.; Temp 930 F (500 C) |
7.97 | 140 | 965 | 4.7 | 4.0 | B106 | 2.3 |
*Combined, Infiltrant 90% Cu-5%Fe-5%Mn. Source: R.L. Pettibone, "Properties and Performance of Infiltrated Powder Metallurgy Parts," Progress in Powder Metallurgy 19:86 (1963). |
Copper-infiltrated iron parts are particularly suitable for applications requiring good resistance to shock loading and good fatigue strength accompanied by resistance to wear. Some examples are:
A clutch hub for an automatic transmission, formerly produced by machining internal and external splines on a forging, was switched to a copper-infiltrated iron P/M part with a cost reduction of 25%.
A printing press paper gripper for use on an offset press was required to resist high wear under light-impact conditions. It was produced of copper-infiltrated iron and had a tensile strength of 75 ksi (517 MPa), an elongation of 11% and a hardness of Rockwell C17-20 without heat treatment.
An automatic transmission part consisting of an SAE 1112 steel pin and a body of P/M iron infiltrated with copper had to meet medium shock, medium torque, load-bearing wear and high-strength requirements. The pin was bonded to the body during sintering. The assembly was carbonitrided and hardened. After this treatment, the body had a tensile strength of 120 ksi (827 MPa) and was file hard.
Back to Top