Compaction
The consolidation of a mass of powder is usually performed in a closed die, although other means such as roll compaction, isostatic compaction, extrusion or forging can be used. Parts can also be produced by slip casting using the techniques employed in pottery making. Regardless of the technique employed, each produces densification of the powder mass that can be related to the density of the solid metal at its upper limit.
Most granular copper powder is used in the production of P/M parts, and, generally, a closed die is used to form a specific shape. As pressure is applied, the operation proceeds in a series of stages: (1) slippage of the particles with little deformation, (2) elastic compression of contact points between particles, (3) plastic deformation of these points to form contact areas of gradually increasing size and (4) massive deformation of the entire powder mass. 1 To achieve uniform densification it is necessary to select a particle-size distribution which will permit uniform packing in the die. It is also necessary to select suitable pressing conditions.
Different materials require different compacting pressures. Pure copper P/M parts are produced with relatively low pressures. An initial compacting pressure of 34- 40 ksi (234-276 MPa)* has been recommended for thin sections although higher pressures can be used for heavier sections. 2 The objective is to permit the escape of gases and water vapor formed by the internal reduction of oxides during sintering. Compacting pressures that are too high will prevent proper sintering of the center of the compact and reduce the electrical conductivity and the strength. Recommended pressures and compression ratios for some copper and copper alloy compacts are given in Table 2.
*Throughout the report strength properties and stresses are given in U.S. units of thousand pounds per square inch (ksi) and in metric (S.I.) units of megapascals (MPa).
Compacting Pressure | |||
---|---|---|---|
Typical P/M Part | tons/sq. in | MPa | Compression Ratio |
Brass Parts | 30-50 | 414-690 | 2.4-2.6:1 |
Bronze Bearings | 15-20 | 207-276 | 2.5-2.7:1 |
Copper-Graphite Brushes | 25-30 | 345-414 | 2.0-3.0:1 |
Copper Parts | 15-18 | 207-248 | 2.6-2.8:1 |
Solid State Sintering
Sintering is the bonding of particles in a mass of powder by atomic or molecular attraction in the solid state through the application of heat. Powders differ from massive metals in having a much greater ratio of surface area to volume. Consequently, the surface energy is greater. During sintering, changes in the shapes of the pores and a reduction in their volume reduces the surface energy.
Sintering can be considered to proceed in three stages. During the first, neck growth proceeds rapidly but powder particles remain discrete. During the second, most densification occurs, the structure recrystallizes and particles diffuse into each other. During the third, isolated pores tend to become spheroidal and densification continues at a much lower rate. 3 Figure 2 illustrates the progress of densification of compacted copper powder as a function of time and temperature.
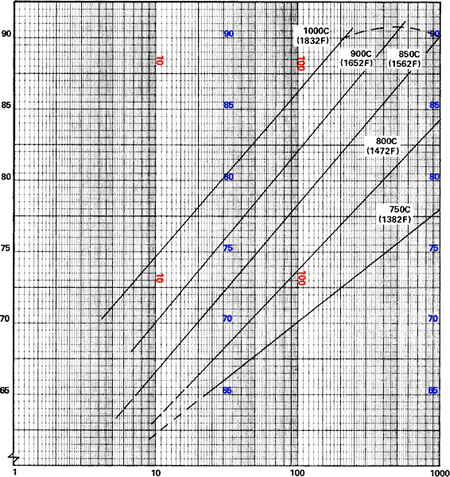
Time, minutes
Figure 2. Effect of Sintering Temperature and Time on Densification of Copper Powder Compacts
Source: R.I. Cable and T.K. Gupta, "Intermediate Stage Sintering," in Sintering and Related Phenomena, New York, Gordon and Breach, 1967.
The rate of sintering has a significant effect on compact properties and can be modified by either physical or chemical treatments of the powder or compact or by incorporating reactive gases in the sintering atmosphere. These treatments are known as activated sintering. The favorable influence of reducible oxide films on copper powder compacts has been known for years. The activation effect is shown by improvements in densification, strength and electrical conductivity of the compacts.
As an example of chemical treatments, improvements in densification of copper powder treated with aqueous formic acid are indicated in Figure 3.
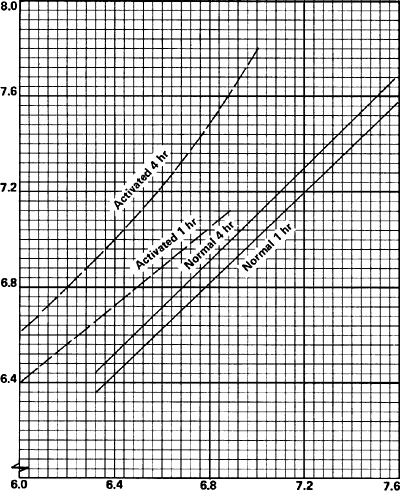
Green Density, g/cm 3
Figure 3. Effect of Activated Sintering on Density of Sintered Copper.
Source: R.I. Cable and T.K. Gupta, "Intermediate Stage Sintering," in Sintering and Related Phenomena, New York, Gordon and Breach, 1967.
Liquid Phase Sintering
In liquid phase sintering a mixture of two or more powders is sintered at a temperature below the melting point of the high-melting constituent but above that of the low-melting constituent.
Liquid phase sintering applies to premixed powders of copper-tin and iron-copper, for example. If the constituents are properly mixed, the behavior on sintering depends on the wetting properties of the two metals. The mechanism of liquid phase sintering can be explained by considering three overlapping actions: (1) the liquid phase allows rearrangement and rapid shrinkage of the solid material, (2) dissolution and re-precipitation occur with accompanying densification and (3) coalescense occurs when the liquid phase disappears. 3
In the copper-tin system, the tin melts and alloys with the copper to form a bronze, with the accompanying expansion of the compact. Figure 4 is a photomicrograph showing the structure of a typical sintered bronze part. In the iron-copper system, the copper melts, becoming saturated with iron, and the iron-copper alloy diffuses into the iron skeleton, causing expansion of the skeleton. Pores remain at the sites vacated by the copper.
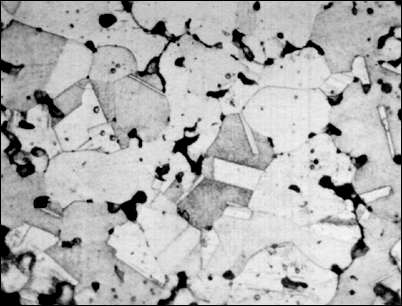
In both the copper-tin and the iron-copper systems, growth or shrinkage of compacts can be modified by the addition of carbon in the form of graphite. Thus, graphite can be used to control dimensional changes in these systems. In the copper-tin-carbon system, sintering is inhibited by mechanical separation of the constituents and, as a result, expansion increases. In the iron-copper-carbon system, the proportion of the liquid phase is increased by the formation of a ternary iron-copper-carbon eutectic which restricts expansion.
Back to TopFootnotes
-
P.J. James, "Fundamental Aspects of the Consolidation of Powders," Powder Met. Int. 4:82 (1972).
-
P.W. Taubenblat, W.E. Smith and C.E. Evans, "Production of P/M Parts from Copper Powder," Precision Metal 30(4):41 (1972).
-
F. Thummler and W. Thomma, "The Sintering Process," Metallurgical Reviews No. 115, June (1967).