We've known for some time that electric motors with die-cast copper rotors can exhibit efficiencies higher than comparable aluminum-cage models if both are designed specifically for that purpose. Basic physics - the I 2R relationship - makes it self-evident. However, data from the Copper Development Association supporting that expectation were mostly derived from what are essentially hand-made test motors, of which no more than a few dozen examples in various sizes were constructed. In fact, a few of those motors actually were proved to be less efficient than expected, owing to certain process- or materials-related phenomena, as described in an ealier Update. Regular readers will recall that two factors, excessive oxygen content of the melt and inappropriate metallurgical condition of the lamination steel, proved to be particularly detrimental. It would therefore be reasonable to expect that other, yet-undiscovered devils might be hiding among the many exacting details attending overall motor design and manufacture.
The underlying question: Is the improved efficiency of copper-rotor motors so sensitive to materials and process controls that consistently meeting levels higher than NEMA PremiumTM under mass-production conditions might prove elusive? And, if that isn't enough to worry about, would the manufacturing cost savings projected in a 2005 Update fall victim to the elevated copper market costs seen since then? The CDA study, which predicted cost reductions of 14% and 18% for 7.5-hp and 15-hp motors, respectively, was conducted when both copper and steel prices were a fraction of what they are today.
Not to worry! The news is entirely positive on both counts. In fact, it's much better than expected.
As Update readers are well aware, the Siemens Energy & Automation (SEA) unit of the giant international electrical equipment manufacturer announced earlier this year that it was bringing to market a line of ultra-efficient motors based on the CDA-led consortium's copper die-casting process (Figure 1). The copper-rotor motor had finally and decisively made the leap from laboratory to mass production! A press release describing the announcement is published elsewhere on this website. Additional details, including nameplate efficiency data and pricing information, can be found on the relevant SEA website.
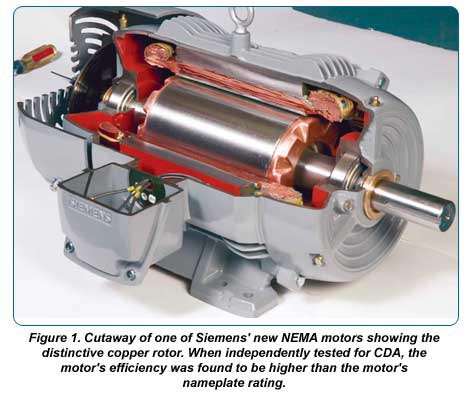
Sure enough, the motors that SEA modestly lists as "Premium Efficient" models sport nameplate efficiency ratings that exceed NEMA Premium levels. For example, the NEMA Premium nominal efficiency for a 10-hp, 208-230/460-V, 1800-rpm, general-purpose TEFC motor is 91.7%. SEA's new versions of this motor, designated GP100 or GP100A (for cast iron and aluminum frame models, respectively) claim a full-load nominal efficiency of 92.4%, or 0.7 percentage points higher than NEMA limits for this size and type. Details can be found on the SEA specification/data sheets for the GP100 and GP100A motors. Other copper-rotor, ultra-high efficiency motors are listed in the company's index.
That's all well and good, but NEMA permits a statistical deviation from its nominal Premium Efficiency ratings to take into account the variations that unavoidably occur under mass-production conditions. Thus, in addition to the nominal rating, NEMA Premium motors' nameplates also generally identify a guaranteed minimum efficiency rating, which is lower than the nominal value.
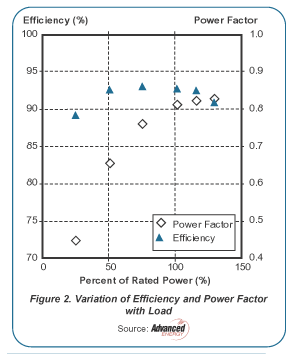
CDA Tests Actual Efficiency Values
In order to determine how well SEA's new motors actually perform, CDA purchased several units from a distributor and submitted them to laboratories for evaluation according to IEEE/ANSI 112-1996, the accepted U.S. test method. (An essentially identical standard applies in Canada.) One of those motors, a 10-hp GP100A, was sent to Advanced Energy, a nationally accredited independent laboratory located in Raleigh, North Carolina ( www.advancedenergy.org). Advanced Energy's lab was the first in the nation (1997) to be accredited for motor efficiency testing by the National Voluntary Laboratory Accreditation Program of the National Institute of Standards. Advanced Energy is well known in the industry. Tables 1 through 3 contain the results of their investigation. Variation in efficiency and power factor as functions of rated power are shown in Figure 2.
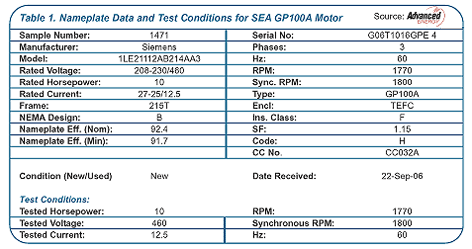
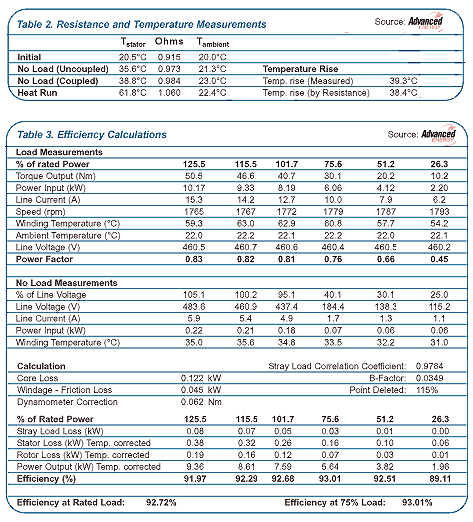
The data present a number of very significant points:
- Temperature rise in the copper-rotor motor is comfortably within Class B (40°C) limits (Table 2). This is conservative, considering that motor's windings contain a proprietary Class F insulation. The low operating temperature suggests the motor should easily exceed its design life since it is widely accepted that cool-running motors last longer.
- When tested at nominally 50%, 75%, 100%, 115% and 125% of rated load, the motor's efficiency substantially exceeds the 91.7% nominal rating for a NEMA Premium motor of this size and type (Table 3). Indeed, the efficiency/load response is essentially flat between 50% and 75% of full load (Figure 2). The motor's actual efficiency is significantly better than its (nominal) nameplate rating.
- Power factor exceeds 0.80 at load factors greater than 75%, making it reasonably comparable with commercial NEMA Premium motors of this size and type.
- As expected, rotor losses are very low, thanks to the motor's high-conductivity, die-cast copper squirrel cage. The fact that stator losses are also quite low indicates that SEA increased the copper content of stator windings at least to the extent typically found in NEMA Premium motors. This represents smart thinking on SEA's part, since (all benefits of the copper rotor aside) there is usually more efficiency improvement to be gained in the stator than in the rotor.
- More significant, however, are the exceedingly low stray-load losses, which range between zero and 80 Watts over the range of loads tested here. Stray losses at 100% load were found to be approximately 50 Watts and only 30 Watts at 75% load. These numbers are meaningful in that stray-load losses, by definition, arise from all sources that cannot readily be accounted for by electrical, magnetic, materials-related, mechanical or thermodynamic factors. As such, they are often interpreted as being indicative of the overall quality of the motor's manufacture.
As mentioned earlier, the CDA-led motor consortium's investigators encountered many technological pitfalls over the course of the six-year R&D program. SEA has apparently addressed these problems - and perhaps others, as well - and applied appropriate solutions in its manufacturing processes. Tests by one additional laboratory (results of which were not available for publication as of this issue) indicate stray-load losses in this motor might be as low as 35 Watts at full load and that efficiency might be as high as 93.3%!
The $64 Question: What about Cost?
The list price for the 10-hp GP100A motor given in the SEA specification/data sheet cited above is $801. Published list prices for other manufacturers' NEMA Premium motors of this size and type currently range between about $890 and $1,020. It should be noted that CDA did not conduct an exhaustive pricing study; other manufacturers' list prices may fall above or below this range.
Of course, list prices are commonly discounted in commercial practice. CDA actually paid $605.42 for the 92.4%-efficient SEA motor. Purchase prices for a sampling of comparable NEMA Premium motors ranged between $596 and $898.
The significant points here are: the manufacturing cost projections made in CDA's 2005 report appear to be conservative, despite the lower raw materials costs at the time, and the SEA copper-rotor motor tested is cost-competitive with conventional, aluminum-cage, NEMA Premium motors of equal or lower efficiency.
CDA congratulates the research scientists, engineers and manufacturing technologists at Siemens Energy & Automation for their accomplishment. Thanks to their efforts - and, of course, the CDA-led consortium and our favorite red metal - the electric motor industry has taken a significant step forward. We can't wait to see what comes next!