Symposium - Copper Plumbing Tube Pitting
Copper plumbing tube has been the industry standard in the U.S. for the last half century. In the year 2000, 750 million pounds were installed in the U.S. ( Figure 1). This translates to 1.2 billion feet installed in that year. Since 1963, the year CDA was established and began tracking consumption, more than 28 billion feet or approximately 5.3 million miles of copper plumbing tube has been installed in U.S. buildings. That is equivalent to a single coil of copper plumbing tube wrapped around the earth 200 times. By any measure, copper has been very successful as a plumbing tube material. However, failures do occur, but they are few and infrequent. Additional information on copper plumbing tube can be found in various locations on our site.
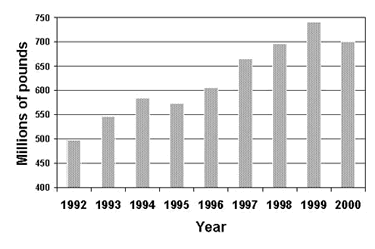
In response to an aberrant increase in pitting failures in one water district in the U.S., a one day symposium on copper plumbing tube pitting was organized for technical personnel in companies which produce copper tubing and fittings, as well as others. The intent of the symposium was not to provide a solution to the pitting failures in this one water district, but rather to review the state of the knowledge in pitting in order to provide direction for future efforts. For additional background, a search of peer reviewed technical articles related to pitting is easily conducted on The Copper Data Center. The Copper Data Center is a searchable database of technical articles, to which newly published papers are added each month. For example, conducting a search with one keyword, pitting, will yield 1002 citations. Using a second keyword, water, will reduce that number to 695 and combining it with a third keyword will reduce it further to 34 references, including authors, titles, keywords and abstracts.
Over the years, analysis of failed copper tubes has been regularly conducted. As shown in Table 5, failures related to flux corrosion are the most common mode of failure and are occurring at an increasing frequency. A great deal, but not everything, is known about corrosion of copper but theories that have little scientific basis are constantly surfacing. Some of these are listed in Table 6.
Corrosion Cause | 1994 | 1995 | 1996 | 1997 | 1998 | 1999 | 2000 |
---|---|---|---|---|---|---|---|
Cold Water Pitting | 0 | 4 | 2 | 1 | 5 | 3 | 2 |
Concentration Cell | 6 | 5 | 3 | 4 | 3 | 8 | 15 |
Flux Corrision | 10 | 18 | 12 | 32 | 17 | 28 | 23 |
Underground Corrosion | 0 | 2 | 5 | 8 | 10 | 13 | 5 |
Green Water | 0 | 1 | 0 | 1 | 0 | 0 | 0 |
Erosion/Corrosion | 3 | 4 | 7 | 6 | 8 | 20 | 7 |
Sulfide Attack | 1 | 0 | 2 | 1 | 0 | 1 | 0 |
Stress Corrosion Cracking | 0 | 0 | 0 | 0 | 0 | 0 | 1 |
Hot Water Pitting | 3 | 2 | 5 | 11 | 14 | 10 | 5 |
Workmanship | 1 | 1 | 2 | 2 | 0 | 1 | 1 |
Glavanic Corrosion | 0 | 0 | 0 | 0 | 0 | 1 | 0 |
Total | 24 | 37 | 38 | 66 | 57 | 85 | 59 |
Table 6. Proposed Causes of Pitting with Little Scientific Basis
- Electrolysis
- Grounding of electrical systems/phone systems to the piping system
- Harmonic divergence (the lining up of the planets)
- Solar flares/sun-spots
- Cellular phone/radio signals
- Cheap/inferior copper or imported copper
Six speakers, who are identified in Table 7, made presentations on the various aspects of copper plumbing tube pitting 2 . The symposium culminated with a panel discussion.
Table 7. Copper Plumbing Tube Symposium Speakers:
- Marc Edwards, Virginia Tech
- Marc Mittleman, Altran Corporation
- Richard Hoffmann, Hoffmann & Fiege Inc.
- Peter Ellis II, M & M Engineering Inc.
- Richard Corbett, Corrosion Testing Laboratory Inc.
- James Myers, JRM Associates
Marc Edwards
Marc Edwards (Virginia Tech) discussed the formation of corrosion films on copper, how they are influenced by pH, water treatments such as chlorine, which has been used in the U.S. since 1904, and the new generation of oxidants, such as the chloramines. It was indicated that the use of aluminum coagulant water treatments increases general corrosion but not pitting. In addition, it was stated that aluminum and chlorine can act synergistically in regard to corrosion and that a source of aluminum includes Portland cement lined pipe, which contains 5% aluminum. It was indicated that pitting has not, to date, been reproduced in the laboratory. Water, which has caused pitting in the actual installations, has been taken back to the laboratory and used in testing, but pitting has not been observed. This implies that copper pitting in potable water is not a completely understood phenomenon. If it were completely understood, it should be ideally reproducible, and thus predictable and hopefully preventable.
Marc Mittelman
Marc Mittelman's (Altran Corp.) presentation focused on microbial corrosion or biocorrosion which he defines as "the loss of essential material properties as a result of biological activity associated with engineering surfaces", "involves biological microbial biofilms" and is "electrochemical in nature". Microbial corrosion, which is often referred to as microbially influenced corrosion (MIC), is not a new phenomenon. It has been around a long time, in fact, since materials have been used by man. However, MIC is an increasing phenomenon because of increasing recognition as a distinct form of corrosion; decreasing residual chlorine efficacy; extending lay-up times during hydrostatic testing; and phosphate scale-control programs leading to higher levels of suspended solids. A severe example of a form of microbial corrosions found in humans, dental plaque, is shown in Figure 2. Another example of microbial corrosion is the massive biofouling of the copper heat exchanger shown in Figure 3. Microbial induced corrosion does occur in copper even though copper is macro-fouling resistant and has well documented biostatic/biocidal properties.
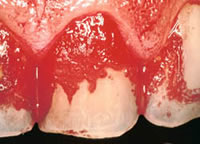
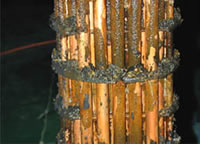
Microbially influence corrosion can be prevented and mitigation strategies are possible, such as cleaning the system to remove organic deposits, using biocides following cleaning if possible, avoiding stagnant conditions, using thermal shock, eliminating nutrient sources, and increasing the pH. In plumbing systems, microbial corrosion can be mitigated by changes in water chemistry, reducing total organic carbon (TOC) and disinfecting by maintaining a residual chlorine level.
Richard Hoffmann
Richard Hoffmann (Hoffmann & Feige) reviewed the reasons for using copper, including its inherent corrosion resistance and its excellent service history, and indicated it performs well 99.9% of the time. It was emphasized that when copper fails, it is usually a result of factors outside the designer's knowledge and control. It was indicated that corrosion on the internal surfaces of tubes is typically associated with contaminants such as excessive flux from soldering. Also, improper chlorination may cause pitting, and chlorination, in combination with residual flux, can result in rapid perforation, sometimes in a matter of days. In addition, other factors, such as high operating velocities, and burrs or lips remaining on unreamed cut ends of soldered tubes can lead to erosion failures. Actions on the exterior of tubes, which are independent of potable water chemistry, can also lead to failure. These included animal waste, which may contain ammonia, and moisture interacting with insulation. A special point was made for the need to insure that sufficient clearance is provided in floor pass-through channels for tubes. Tight floor pass-through channels, which can partially restrict tube movement, are known to be a factor in corrosion fatigue. In summary, it was stated that copper corrosion can be attributed to several factors including water-side chemistry leading to pitting, improper operation or design such as a high velocity or stagnation, foreign contamination on the outer surface of the tubes, and on inner surfaces during storage prior to installation. However, it was stressed that poor workmanship including excessive use of flux is also a most important factor.
Peter Ellis
Peter Ellis (Mechanical and Materials Engineering) presented a very thorough review of pitting from a historical prospective and challenged the theory that exposure to "pitting waters" necessarily results in pitting. Aggressive "pitting waters" are characterized as having a pH range of 7.2 to 7.8, high content of CO 2, (over 10 ppm), high total dissolved solids including sulfates and chlorides, and the presence of dissolved oxygen gas 3 . It was stated that exposure to " pitting waters " and other waters shows no difference in the time for a first leak to appear 4 , as shown in Figure 4. After the present state of knowledge of pitting was reviewed, it was concluded that "a coherent theory, that allows prediction or prevention of copper pitting, is currently lacking". In a test loop 4 , in which "pitting water" was passed through a system consisting of three parallel runs, each run was joined by a different method. The results of this exposure clearly show, as illustrated in Figure 5, that all other things being equal, flux plays a large role in pitting perforations. A variety of antroprogenic (i.e. of human origin) causes are responsible for premature failures, as illustrated schematically in Figure 6. They include failures related to flux, erosion downstream of burrs, incomplete soldering leading to crevices, microbiological action (as a result of inadequate water treatment or stagnation) and debris leading to underdeposit corrosion. In closing, it was illustrated that the antroprogenic causes are increasing, as shown in Figure 7. 4,5
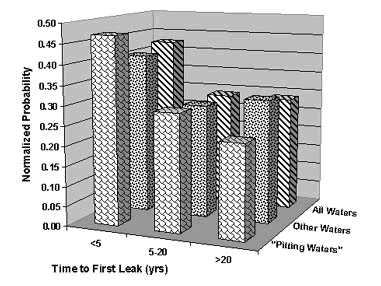
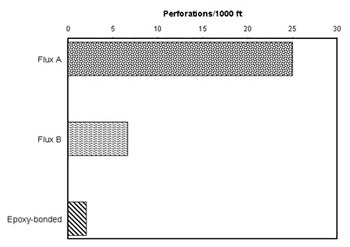
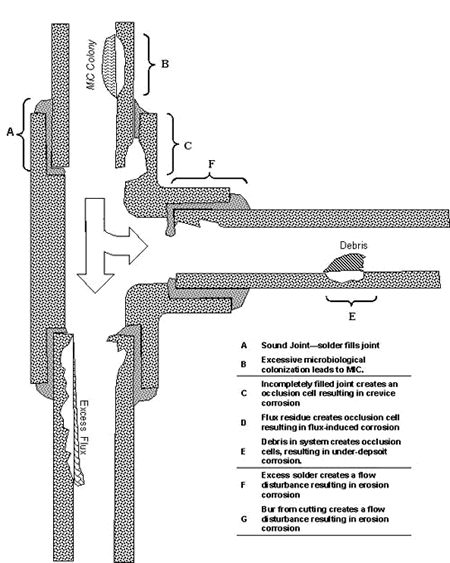
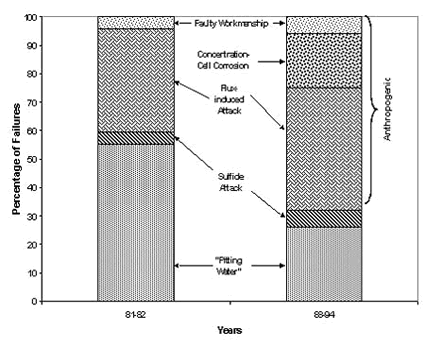
Rick Corbett
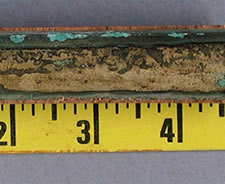
Rick Corbett (Corrosion Testing Laboratory) reported on the cause of extensive pitting observed in a new hotel in the Middle East after only one year. On the basis of only one small sample and little in the way of operational parameters, it was determined that water quality was a major factor in the observed failures. It was known that a reverse osmosis plant supplied the water, which was heated and recirculated in a closed loop. It was speculated that the system may have had stagnant branches. On the basis of observation of a tan colored deposit on one-quarter of the circular segment of a tube, which is shown in Figure 8, it was concluded that this was the lower portion of a horizontal section. The chemical analysis of this deposit showed high calcium, and contained copper, iron, silicon and magnesium, as shown in Table 8. The remainder of the ID surface is covered with a light green scale with scattered islands of heavy blue-green deposits. The point chemical analysis of this heavy blue-green scale is presented in Table 9 for several locations, and indicates varying amounts of chlorine, sulfur and to a lesser extent, silicon. One should guard against the danger of sweeping generalizations, especially on the basis of one sample and incomplete operational history. However, the aggressive nature of both chloride and sulfur, are well known. Both can be detrimental to copper. It was concluded that the water quality was less than ideal and the high concentrations of contaminants, which can be aggressive to copper were present. The life of the hot water system was greatly reduced.
Ca | Fe | Si | Mg | Cu |
---|---|---|---|---|
64% | 8% | 2.5% | 1% | balance |
Location | Cu | C1 | S | Si |
---|---|---|---|---|
A | 64% | 35% | < 1% | 1% |
B | 98% | < 1% | 0% | 1% |
C | 98% | < 1% | < 1% | < 1% |
D | 97% | 1% | 1% | < 1% |
E | 84% | < 1% | 15% | < 1% |
F | 92% | 0% | 8% | 0% |
G | 75% | 20% | 5% | 0% |
James Meyers
James Meyers (JRM Associates) presented a broad review of over 1200 investigations of copper tube failures that have been analyzed over many years. It was indicated that there are seven forms of corrosion seen in domestic water systems, which are flux-induced pitting, hydrogen sulfide-induced pitting, erosion (and cavitation), cuprosolvency, concentration-cell corrosion, chemistry-related cold water pitting and chemistry-related hot water pitting. An extensive description of each form of corrosion was provided. In conclusion, it was stressds that all seven forms of corrosion can be viably and cost-effectively mitigated if: the systems are properly designed in such a way that velocities do not exceed 4 to 5 fps (1.2 to 1.5 mps) in circulating systems, the copper tubing systems are properly installed using the general guidelines presented in ASTM Standard Specification B 828 and the CDA Tube Handbook 3 without the use of excessive flux or unusually aggressive fluxes, the systems are operated within the design parameters including safe and energy-efficient hot water temperatures between 120°F to 130°F (49°C to 54°C), corrosion of water heater/storage tanks is prevented, and the water purveyor distributes quality products which do not contain unacceptable amounts of suspended solids, dissolved carbon dioxide, microorganisms, aluminum, dissolved hydrogen sulfide and/or iron.
Conclusions from the Symposium on Pitting of Copper Plumbing Tube
It was concluded that:
- by any measure, copper is a very successful plumbing tube material.
- failures do occur, but they are few and infrequent.
- pitting has not been reproduced under controlled laboratory conditions.
- a coherent theory that allows prediction or prevention of pitting is currently lacking.
- flux induced attack is a major cause of pitting.
- pitting can occur under deposits, and crevice attack can be observed in incompletely filled joints.
- erosion failures are a result of poor design and installation, as well as operating at excessive velocities.
- MIC is increasing because of increasing recognition as a distinct form of corrosion, decreasing residual chlorine levels, extended lay-up times during hydrostatic testing, and higher levels of suspended solids related to phosphate scale-control programs.
- MIC can be mitigated by cleaning to remove organic deposits, use of biocides-after cleaning if possible, avoiding stagnant conditions, using thermal shock, eliminating nutrient sources, and increasing pH.
- corrosion can be mitigated if:
- systems are designed so that velocities do not exceed 4 to 5 fps ( 1.2 to 1.5 mps ) in circulating systems.
- copper tubing systems are properly installed, without he use of excessive or unusually aggressive fluxes.
- systems are operated within design parameters including safe and energy-efficient hot water temperatures between 120°F and 130°F (49°C and 54°C ).
- hot water heater/storage tank corrosion is prevented.
- the water purveyor distribute quality product which does not contain unacceptable amounts of suspended solids, dissolved carbon dioxide, microorganisms, aluminum, dissolved hydrogen sulfide and / or iron.
References
-
Copper Symposium 2001, Plumbing Tube, Publication Number A4056-XX/01 The Copper Development Association Inc., New York, 2001.
-
The Copper Tube Handbook, Publication Number A4015-94/95, The Copper Development Association Inc., New York, 1995.
-
A. Cohen and J.R. Myers, " Mitigation of Copper Tube Cold Water Pitting by Water Treatment, " Corrosion/84, NACE International, Houston, TX, 1984.
-
J.R. Meyers and A. Cohen, " Pitting Corrosion of Copper in Cold Potable Water Systems " , Materials Performance, 34 (10), October 1995.