The Defense Logistics Agency (DLA) provides worldwide logistics support for the missions of the Military Departments and the Unified Combatant Commands within the U.S. Department of Defense (DoD). The Defense Logistics Agency's mission is to provide best value logistics support to America's Armed Forces, in peace and war, around the clock, around the world.
The DLA has a serious supply problem and has awarded CDA a $1 million contract to help provide a solution. The problem: the U.S. manufacturing base for mechanical components in DoD's older, "legacy" equipment has simply disappeared. The vanished manufacturers are the second- and third-tier suppliers of the components and spare parts needed to keep major weapons systems operational. What happened to them? They may have moved their manufacturing operations offshore, or maybe they simply fell victim to the manufacturing sector's recent sluggishness. Whatever the reason, DLA's need is real. According to Dr. John Cowie, CDA's motor rotor project manager, DLA believes one way to fill the gap is by embracing new, more efficient manufacturing technology.
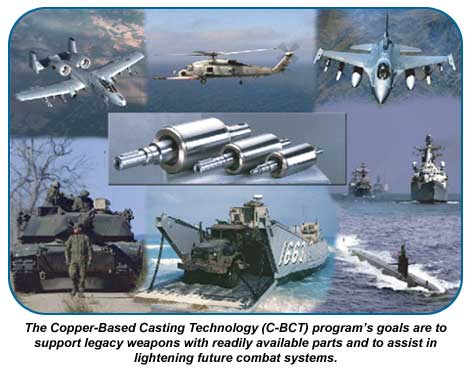
Cowie points out that CDA has become adept at technology development. The copper motor rotor is probably the best example of this activity, and, in fact, it accounts for one part of the DLA/DoD contract, as will be explained shortly.
Think outside the box for a second. CDA's motor rotor is not just a way to replace aluminum squirrel cages with copper. What CDA actually developed, says Cowie, is "a new way (using ordinary pressure die casting) to make a whole lot of things from copper and copper alloys that didn't exist before."
"Taking that one step further," he continues, "and applying the key technical elements of the motor rotor's success (using superalloy casting dies and operating them at elevated temperatures), to products other than motors, you find an answer that might help solve DLA's supply problem. It's a process known as semi-solid casting."
Semi-solid casting is nothing new. Among other things, this offshoot of pressure die-casting technology is used to make products such as "mag" automotive wheels, which are actually aluminum. Like die casting, the process is fast, economical (for large-volume production) and capable of producing near-net-shape products with good mechanical properties and excellent surface finishes.
As its name implies, the semi-solid process involves the pressure casting of metal while it is in a partly liquid/partly solid state at temperatures between the liquidus and solidus for the alloy in question. Cowie says the metallurgical key to success is that the alloys' freezing ranges must be fairly wide. A number of copper alloys meet that criterion.
Just as was the case with aluminum squirrel cage rotors, the roadblock to copper-based semi-solid castings was limited die life. Therefore, the know-how CDA gained while developing the die-cast copper motor rotor is precisely the information needed to make semi-solid casting work with copper alloys.
Recognizing this, DLA became very interested in CDA's new technology because it saw a possible way to alleviate its parts supply problem. Why? Because with relatively few modifications (and only modest investment), many hundreds of die-casting shops could rapidly convert a portion of their operations to the manufacture of precision, high-strength products of the types the DLA needs. For example, components currently made from mild, low-alloy or stainless steels might be converted to appropriate copper alloys such as high-strength brasses or aluminum bronzes.
Second, and in more general terms, DoD is interested in new manufacturing methods for its Future Combat Systems (FCS) program. The new systems in question will be lightweight, highly mobile and possibly robotic. The desired capability will take what one defense organization called "advanced technologies, a revolution in both strategy and tactics, and innovative industrial teaming."
CDA is now a part of that team. A portion of the initial Congressional appropriation that backs the DLA/DoD contract award will target semi-solid casting development well beyond proof-of-concept. Follow-on contracts are anticipated as the new casting technology finds additional applications. Even more interesting is the prospect that die casters serving primarily commercial customers will see semi-solid casting as a means to expand their businesses.
DLA first became aware of the semi-solid casting program through the motor rotor program, and it retains a strong interest in CDA's breakthrough technology. The Navy, in particular, is interested in a motor's ability to operate at ultrahigh electrical efficiencies. They see that as being critically important on today's warships, whose generating capacities are hard pressed to meet the needs of modern electrical and electronic weap-onry. Efficient motors can reduce a ship's electrical load, and since copper is the proven way to achieve efficiency, DLA is willing to invest a portion of its grant to develop the technology.
Copper-rotor-based motors can also be made lighter, smaller and possibly less costly (for equivalent output) than conventional aluminum motors. That makes them very interesting to aerospace engineers looking at tomorrow's aircraft and missiles, where more bang for the buck is more than just an expression. Another portion of the DLA/DoD award will therefore look at prospects for weight savings in new motor designs.
A wise person once said that for success, you have to be smart for only ten minutes; the rest is easy. Development of the copper motor rotor may have taken a bit longer than ten minutes, says Cowie, but the possibilities this revolutionary technology has opened up can lead to an entirely new spectrum of copper-based products for both defense and commercial applications.