- Use a nickel-base superalloy as the die material.
- Preheat the die to approximately 650 C (1202 F) before injecting molten copper, and maintain that temperature between shots.
A superalloy - and there are several viable choices - resists softening and oxidation at the high operating temperatures involved, while preheating the die and keeping it hot reduces thermal stresses that rise abruptly each time the die is filled. Reduced stress, in turn, delays the onset of the alligator-skin-like heat checking that marks die failure.
CDA found that applying these practices extends die life to at least several thousand shots, long enough to make the process commercially viable. The pertinent question, of course, is how long can die life actually be extended: Is it 5,000 shots? 10,000? 50,000? Companies considering the production of copper motor rotors need a reasonable estimate to predict costs. The fact that a European manufacturer is currently in large-scale serial production (Update, Vol.4 Issue 1) of copper rotors suggests that even longer life than that experienced in CDA's tests might be attainable.
Unfortunately, die life testing using actual rotors is made very expensive by the need for large numbers of laminations and arbors, not to mention the cost of the tooling itself. CDA therefore chose to simulate tests with a computerized model of the die-casting process.
Modeling Program
Prof. Jerald Brevick of the Ohio State University (OSU) Department of Mechanical Engineering supervised the study. The OSU researchers first calculated the surface temperature of the die at the time molten copper (at 1200 C, 2192 F) is introduced and for several minutes thereafter. This portion of the study required thermal mapping, a task accomplished with ANSYS, a commercial analysis program. Dies would be assigned preheat temperatures of 200 C, 350 C and 650 C (392 F, 662 F and 1202 F), respectively, as a check on CDA's experience that increasing die temperature increases die life. As might be expected, cooling times increased with increasing die preheat temperatures.
The transient, nonlinear thermal analysis took into account copper's material properties for the casting and the superalloy's properties for the die. Certain assumptions were necessary, among them an estimate of the thermal contact conductance, also called the gap conductance.
Simulations assumed a worst-case scenario with a high and constant value of contact conductance (10,000 W/m2K). The copper temperature was assumed to be 1200 C (2192 F).
The researchers next calculated thermally induced strains arising from the respective temperature profiles. Calculations were made using finite element analysis (FEA) - also within ANSYS - in which the complex shape of the die is partitioned into a grid of small elements for which local strains can be determined using iterative computer calculations that take into account the die materials' physical and mechanical properties. Only the die was considered in this part of the investigation. The FEA was conducted using two-dimensional elements. It quickly became apparent that the thermally induced stresses - all of them compressive - exceeded the yield strength of the die materials; therefore, both elastic and plastic properties of the material had to be taken into account. The resulting strain maps were then evaluated to identify nodes at which stresses and strains are highest, i.e., where thermal fatigue failure would most likely begin.
It remained to calculate the fatigue life (reported as the number of die-casting shots) based on those strains and known or estimated material properties under those conditions. This calculation was made using a technique known as the method of universal slopes, which was originally developed for NASA. Its fundamental equation of strain is:

where is the sum of the plastic and elastic strain ranges. Calculated strains are the effective or von Mises strains, determined from the calculated principal strains,
1,
2,
3,

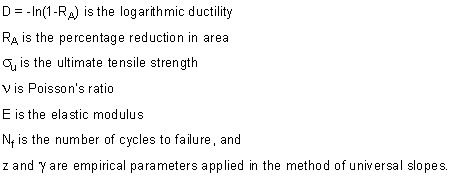
In this case, calculation of the number of cycles to failure considers only the plastic portion of the strain equation, since plastic strains predominate, or, more to the point, the die operates in a low-cycle fatigue regime.
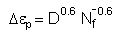
Superalloy Die Materials
The OSU researchers were asked to evaluate the performance of Inconel 617 and Haynes 230, two nickel-base superalloys previously selected by CDA.
Inconel 617 is a solid-solution, nickel-chromium-cobalt-molybdenum alloy with exceptional high-temperature strength and oxidation resistance. Inconel 617 was chosen for analysis because it was concluded to be one of the most reliable die materials from the earlier CDA test program. This alloy gave very good results after preheating the die to about 650 C.
Haynes 230 alloy is a nickel-chromium-tungsten-molybdenum alloy with excellent high temperature strength and outstanding resistance to oxidizing environments up to 1149 C. It has good long-term thermal stability and low thermal expansion, and it exhibits high elongation and reduction in area at elevated temperatures, both of which are measures of ductility. This alloy was evaluated after CDA's tests as an alternative to the Inconel alloy, due to its high temperature strength properties. Particularly important are the alloy's excellent creep and stress-rupture strength and the fact that it exhibits excellent low-cycle fatigue properties at elevated temperatures. In addition, alloy 230 is easily weld-repairable, in contrast to most other die materials, which can assist in achieving long die life in production.
Model Casting
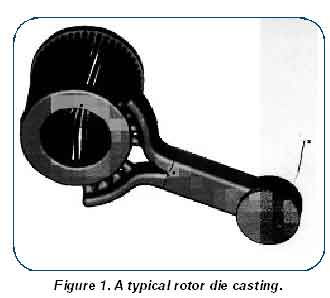
Figure 1 shows a model of a typical motor rotor die casting. Hot metal enters at the biscuit (far right), then passes through the runner and gates to the near-side end ring. It then passes through the conductor bars to the ejection-side end ring. Thermal analysis predicted that the die's highest thermal loading would be at the near end of the biscuit (as seen in the figure), along the flat surfaces of the runner and at the entrance to the gates. Since the remainder of the die would see lower stresses and therefore fail after a much higher number of cycles, the end rings and conductor bars were not modeled.
The symmetrical configuration of the runner suggested the use of the two-dimensional ANSYS software to calculate strains. Doing so reduced computation time. Although the biscuit is circular (axisymmetric) in cross section, it was treated as a planar element in the evaluation. Ultimately, the biscuit was not considered at all in terms of die-life prediction, since most of it is in contact with the shot sleeve, which is made of a different material. Cooling lines were not modeled, and only thermal loads were taken into account; i.e., mechanical loads were ignored in the current investigation. A cross section of the modeled area and a typical two-dimensional FEA map are shown in Figures 2 and 3.
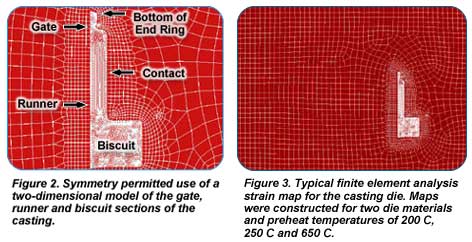
The model was meshed as two separate areas, one inside the other ( Figures 2 and 3). The study could, therefore, be described as an uncoupled thermal-structural analysis, in which temperature distributions from the thermal analysis were applied as loads for the subsequent structural analysis, while the results of the structural analysis were not applied as loads for the thermal analysis.
FEA predicted that highest stresses would occur at nodes B, C and D on Surface 1 (which is also the parting line for the mold) and at nodes A and E on Surface 2, shown in Figures 4 and 5.
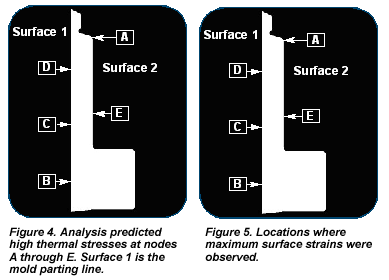
Figure 6 shows the change in die life (number of cycles to failure) as influenced by initial bulk die temperature (200 C, 350 C and 650 C) for nodes on die Surfaces 1 (B, C and D) and 2 (A and E) for the two die materials. According to the analysis, location A, an inside radius close to the gate area, should exhibit the shortest die life for both die materials investigated. Location B, at the mold inlet, is also expected to experience early failure. The results, while encouraging, should be viewed as quite conservative.
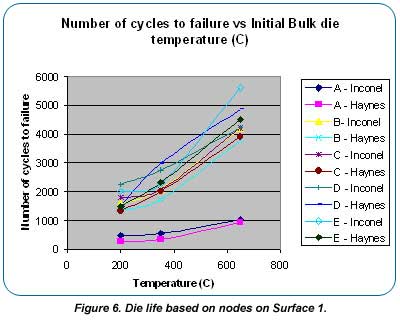
A Conservative Model
The model clearly explains and corroborates CDA's observations that heated dies prolong die life. It also correctly identifies locations in the die that would most likely fail first (and should, therefore, be constructed as replaceable inserts). However, several necessary assumptions taken in the model possibly lead to overly conservative predictions with regard to attainable die life:
- The nickel-base superalloy Haynes 230 is quite ductile at elevated temperatures. In fact, ductility is one of the principal reasons it was selected. Unfortunately, no data on percent reduction in area at the temperature of interest are available for the alloy. Estimates of %RA made from available elongation data are probably low, perhaps by a factor of two or more, and use of experimental %RA values (if available) would have a correspondingly large positive effect on the predicted die life.
- Similarly, while the von Mises-Hencky failure criterion is generally regarded as giving the closest correlation with experimental results, it is based on tensile behavior; whereas, fatigue failure in the case of a cyclically heated die surface more likely results under shear deformation. Such deformations can be considerably larger than the instability-bound tensile ductility limit, and, if applied to the model, would lead to longer predicted (and actual) die life.
Finally, the experience of the European die caster cited earlier, as well as CDA's own finding that the life of even H-13 die steel can be extended by as much as 75 times by preheating to temperatures as low as 490 C (914 F) suggest strongly that die lives far longer than those predicted in the model should be attainable. Further work remains to be done, but it is not unreasonable to expect that die life comparable with that seen with low-temperature die-casting operations might ultimately be attained.