FAVI S.A., a major French supplier of copper and copper alloy die castings, now offers custom-designed, copper-based rotors for squirrel-cage electric motors in sizes ranging from fractionals to 100 hp. Announcement of the company's breakthrough to full commercial-scale production is certain to be greeted with interest by motor manufacturers and others who might be thinking about entering the "super premium efficiency" motor market but are hesitant to take on the considerable technical hurdles involved. FAVI has already crossed those hurdles thanks to a 10-year R&D program conducted at the company's Hallencourt, France, facilities.
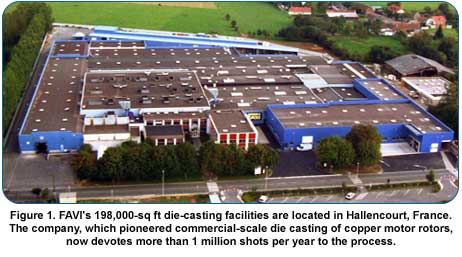
The manufacture of copper rotors is a natural evolution for the FAVI organization, which has built a strong reputation throughout Europe as a supplier of die-cast copper-alloy components for a variety of industries. The company began 47 years ago as a leading manufacturer of plumbing and water-handling products. It then found new opportunities in other die-cast products such as lock parts, electrical hardware and automotive components. Most products are die cast in standard brasses or in custom copper alloys designed by the company's metallurgists.
About 10 years ago, a large pump manufacturer asked FAVI if it would be possible to die cast copper motor rotors. Grundfos, based in Denmark, was seeking an alternative to aluminum rotors for use in its submersible pumps, where corrosion resistance is important. Copper was clearly the preferred material because its corrosion resistance and electrical conductivity are both significantly higher than for aluminum. As readers of this newsletter know, die casting copper is anything but simple, but FAVI engineers were able to draw upon their extensive experience with copper alloys to make the process work. Nevertheless, bringing copper rotors to commercial production took nearly 10 years.
Today, FAVI supplies rotors in a variety of configurations based on customer specifications. Included among its client listings are a growing number of European industrial equipment manufacturers. Some, like Grundfos, are looking for better corrosion resistance, while others are more interested in high electrical efficiency or the more compact size (for equivalent power) that copper makes possible.
Short Delivery Time
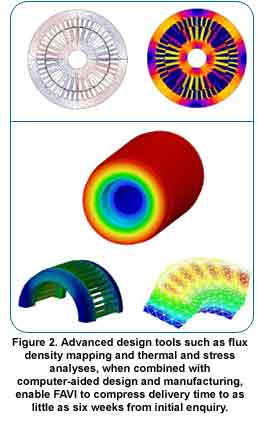
After receiving an enquiry, FAVI engineers work with customers to design the rotor. Size and slot configurations are optimized to achieve the required electrical, magnetic and mechanical characteristics commensurate with dimensional constraints. Modeling and computer-aided design facilitates the process, enabling the prediction of induction and flux density for various slot designs and of temperature and stress distribution in conceptual rotors (Figure 2). Such state-of-the-art design tools shorten the interval from initial enquiry to production to as little as two months.
FAVI's comprehensive service includes design and assembly of all tooling. In addition, prototype rotors are tested at a 3,000 sq ft research facility supported by the company at the Graduate School for Electronic and Electrical Engineering (École Supérieure d'Enginieurs en Electrotechnique et Electronique, ESIEE) in nearby Amiens.
Equipment includes two fully instrumented test stands, at 11kW and 75kW, to evaluate rotor performance and quality. Tests can be conducted according to several international standards, including IEC 34-2, CSA C390-98, CEI 61972 and IEEE 112-1996 (B). In terms of quality control and assurance, the company is fully certified under ISO 14001, ISO 9002, and ISO 9001 version 2000, as well as EAQF 94, QS 9000, QSE and OHSAS 18001.
Looking Ahead, Expanding Production Facilities
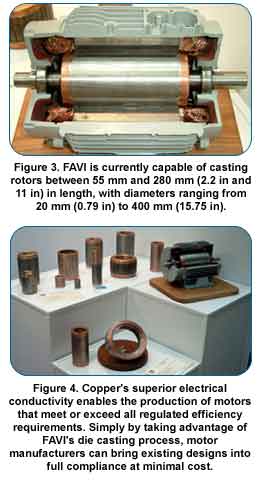
FAVI's Hallencourt plant currently devotes some 1,000,000 injection shots per year to the production of copper rotors. The number of rotors produced is somewhat larger, since smaller models permit the use of multi-cavity molds. Production capacity can be increased further to meet the needs of motor manufacturers seeking to adapt their product lines to new European efficiency standards. That, according to Olivier Walti, manager of FAVI's rotor program, is something that can be accomplished quickly and cost-effectively by simply converting the rotor from aluminum to copper. Several large manufacturers, including ITT/Grundfos, LeRoy Somer/Emerson and SEW Eurodrive, the German supplier of motor and drive technologies, are currently exploring this approach to improve efficiency of their equipment.
Walti points out that FAVI is currently capable of casting rotors with axial lengths between 56 mm and 280 mm (2.2 in and 11 in). Minimum rotor diameter is 20 mm (0.79 in). With its strong engineering department, says Walti, the company can readily and quickly adapt rotor designs to their customers' individual requirements. Looking farther down the road, FAVI sees exciting new possibilities in the production of highly efficient copper-based starter-alternators for the next generation of automobiles.
Additional information about FAVI and its copper rotor program is available on their website. Worldwide enquiries can be directed to: Olivier Walti, Manager, FAVI S.A., 14, rue Louis Deneux, B.P.5, 80490, Hallencourt - France. Tél.: +33 (0)3 22 66 20 20. Fax.: +33 (0)3 22 66 20 63 e-mail: rotor@favi.com.
FAVI is represented in North America by: Patrick Cicchini, F.C.M., 30600 Telegraph Rd., Suite 2183, Bingham Farms, MI 48025, USA. Tel: 248-594-9922. fax: 248-540-2408. e-mail: fcmfavi@aol.com.