The die-casting technology developed by the copper industry is now in commercial use and proving to be a robust process. Although still in early production, this new manufacturing process is confirming our development team's analysis that it is an economical method to manufacture copper rotors that significantly improves motor efficiency. Motors with cast copper rotors are now sold commercially by an innovative motor manufacturer, SEW Eurodrive. We believe more companies will make similar new-product announcements within a few months.
Widespread adoption of this technology will bring important benefits to the motor industry and, importantly, to end users, environmentalists and the copper industry. I would like to share that perspective with Update readers.
Motor Manufacturers
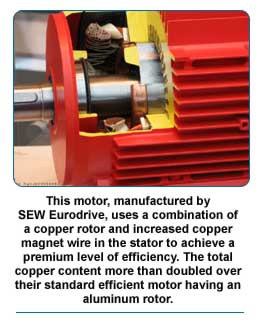
Motor design engineers at SEW Eurodrive calculate that this copper technology can have a positive impact on costs because it may be possible to reduce the size of a motor without lowering its power output or level of efficiency - a major cost driver. And, if production experience like SEW's, proves it is possible to manufacture motors with copper rotors more economically than those with aluminum rotors, copper will replace aluminum in the rotors of many, if not most, induction motor applications.
End-Users
Clearly the use of premium-efficiency, and now the possibility of super-premium-efficiency motors, versus standard-efficiency motors will save end users a substantial amount of money over the life of a motor. And, as SEW's Martin Doppelbauer observes, unless economic incentives, such as rebates or tax incentives, are offered, many end users of high-efficiency motors are likely to continue making purchasing decisions based solely on the initial purchase price. The idea of life-cycle costing - long-term energy costs versus one-time purchasing costs - is still not sufficiently widespread. Purchasing managers must be further educated on the concept of energy efficiency. Governmental regulations raising the required minimum efficiency levels of motors would push managers in the right direction and help reduce energy consumption.
Environmentalists
Motors with copper in the conductor bars of the rotor will make a substantial contribution toward energy conservation. This offers positive benefits in terms of reduced greenhouse gas emissions and their contribution to global warming.
The efficiency increase seen in motors with copper rotors is due largely to the reduced I2R losses in the rotor, because the electrical conductivity of copper is nearly 60% higher than that of aluminum. Because of the widespread use of motors, significant energy savings are possible. The U.S. Department of Energy reports that motors above 1/6 hp use about 60% of all electricity generated in the United States and that medium power motors (1-125 hp) use about 60% of the electricity supplied to all motors. A one-percent increase in motor electrical energy efficiency would save 20 billion kWh per year or $1.4 billion in electricity (at $0.07 per kWh) and 3.5 million barrels of oil in the USA alone. Worldwide, these savings would be multiplied by about a factor of four.