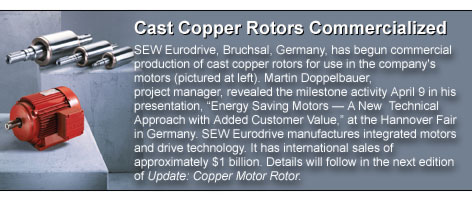
Last year, we reported on a small die casting business in India that, with limited equipment and resources, was performing its own copper motor rotor trials and meeting with a fair amount of success. The ingenuity displayed by this small operation piqued the interest of the Copper Development Association's Copper Motor Rotor Project Manager, Dr. John Cowie. Update recently caught up with Akhtar Hussain G. Ajmearwala, owner and operator of Perfect Die Cast in Gujarat, India, and found that the efforts of his team continue to push the limits of their resources to die cast copper rotors.
A significant obstacle for Ajmearwala and his team is the use of steel dies in their copper motor rotor trials, "We can die cast a rotor as long as 300 mm with our current machinery, but we have a problem with heat checking," Ajmearwala said. CDA's research has demonstrated that nickel alloy dies are far superior for die casting copper.
Cowie explains, "Nickel alloy dies (Inconel 617 or Haynes 230) preheated above 600 C prevent surface cracking known as 'heat checking' from occurring during repeated expansion and contraction. The preheating substantially decreases the cyclic thermal expansion and contraction from die casting high-melting-point metals such as copper. Since tool steel loses its strength above 500 C, it cannot be adequately preheated to prevent this thermally induced fatigue cracking from occurring. Consequently, only materials that retain their properties of strength, ductility and oxidation resistance at elevated temperature can be successfully employed in this application."
Despite their difficulties, Perfect Die Cast has found a niche market in die casting copper motor rotors specifically for submersible pumps. The company has been contracted by a major Indian motor and pump manufacturer to cast motors in a wide array of sizes. "We've die-cast pump rotors 48 mm in diameter and 200 mm in length, very easily," he explained (see Figure 1). According to Cowie, the longer rotor is particularly difficult to cast, "When molten copper is filling the rotor's far end ring, the copper is substantially cooled while passing through the long slots in the steel laminations that eventually form the copper conductor bars. If the copper is cooled too much, there is a danger of it freezing off inside these slots, which would not allow the complete filling of the far end ring and result in excessive porosity" he said.
"We made a most encouraging achievement recently when we achieved a 2.5% gain in efficiency versus an aluminum die cast rotor. The company that contracted with us is continuing their tests on the rotors we made and are very interested in copper cast rotors," Ajmearwala said. (see Figure 2).
"Submersible cast copper rotors are an attractive alternative to fabricated copper rotors, as the fabrication process is a very complicated and costly procedure. These rotors often reach the length of 1100 mm," Ajmearwala said. Cowie explained that, due to the complexity of manufacture, fabricated rotors sometimes vibrate, causing premature failure. This is mainly due to misalignment, partly as a result of the air gap between the end ring and laminations.
"With a cast copper rotor, there is no room for the air gap. This results in a smooth working rotor with far better conductivity and a much longer working period," Ajmearwala said. He also reports improved motor efficiency, due to lower starting torque and a 40 percent increase in a pump's water output.
While not yet in full production, Perfect Diecast has gained the interest of motor companies from Bombay to Europe. "Almost every part of our success in copper motor rotors can be initially attributed to CDA," Ajmearwala explained. However helpful technological support can be, the ingenuity displayed by Mr. Ajmearwala and his team is the secret to their copper die casting success. "It seems that very soon the market will see a new super-premium-efficiency motor which will start a new revolution in motors," he said, explaining his enthusiasm and undaunted efforts.