Other Headlines
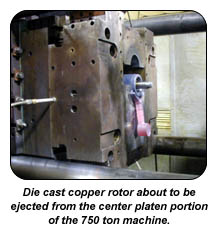
The September issue of Die Casting Engineer (the official publication of the North American Die Casting Association) contains a report of the Copper Development Association's copper motor rotor project. The article, "Mold Materials and Process Modifications to Die-Cast the Copper Conductors of Induction Motor Rotor," states that "the potential energy savings of applying copper to the rotors of medium horsepower motors are a significant national consideration."
The article is more than just a glance at the ongoing project; it takes an in-depth look at the specific trials of the project. The reader is led through the successes and failures of various candidate mold materials, test molds and molding equipment. The article also contains detailed test results. It is the most comprehensive report on the copper motor rotor project thus far and required reading for those interested in this exciting new technology. An excerpt follows:
"The copper die-casting tests indicate that certain nickel-based alloys (INCONEL alloys 601, 617, and 625) operated in the 600-650°C temperature range are very promising mold materials for die-casting of copper motor rotors.
An important conclusion from this work is that it is absolutely essential to operate dies at elevated temperature to extend die life. The higher die temperature reduces the thermal gradient from the surface to the interior on each shot which in turn greatly minimizes the expansion and contraction associated with each cycle and thus the thermal fatigue of the surface that leads to crazing and eventually to significant cracking. INCONEL alloys 617 and 625 operated at about 650°C are excellent die materials. Temperatures above 650°C are not required and in fact would reduce productivity by increasing the cooling time. A practical method to achieve the necessary die temperature has been developed.
Copper motor rotors were pressure die cast and evaluated in motor tests by the several motor manufacturer partners. Motor companies tested the copper rotors according to IEC 34-2 and IEEE Std. 112 Method B. A standard rotor with die-cast aluminum bars and end rings was tested to provide the baseline. All rotors were tested by each company in the same wound stator dynamometer test bench to eliminate other performance variations. Overall motor efficiency was increased by a solid 1.2 and 1.6 percentage points in motors tested with the two sets of copper rotors cast. This is significant because 20 years of motor efficiency improvements have been accomplished by using all of the readily available approaches. Copper rotors represent the only way to reduce losses significantly without turning to expensive amorphous iron or superconductivity."