The Copper Motor Rotor Program has been met with great enthusiasm throughout the motor industry since the project's inception. Development goals have been met and the die-casting-tool material problem has been solved. As progress moves from research and development to promotion, the copper industry is on the brink of a new multimillion pound per year, worldwide market in the electric motor arena.
At the Annual Spring Meeting of the Copper Development Association in June, industry expert, Darryl Van Son, presented some impressive data which points to the breadth of this potential market:
- Motors use 2 trillion kWh per year;
- Two-thirds of all electricity used by industry is expended running motors;
- Just 1 percent increased motor efficiency would save 20 billion kWh per year - the equivalent to $1.4 billion at 7 cents per kWh.
Mr. Van Son also outlined the test results achieved by the copper motor rotor project team. The team is comprised of: Dr. John Cowie, CDA; Dr. Edwin Brush, BBF & Associates; John Mollet, ICA; Dr. Stephen Midson, Formcast; Jay Keist, Formcast; Ruedi Beck, DieTech; Darryl Van Son, Van Son & Associates; and Dr. Dale Peters, consultant to CDA. In a direct copper-to-aluminum comparison, seven rotors were tested in the same stator and on the same dynamometer. Test results were compared to a large database of previous motor tests that used aluminum rotors. The aluminum motor rotor data were simply averaged to provide a reference "standard" motor.
The following paragraphs outline the results of the team's testing efforts. Each run measured iron core loss, stator resistance, rotor resistance, windage and friction, and stray load losses. These terms are defined:
- Iron core loss - magnetic losses in lamination stack, inductance and eddy current losses.
- Stator resistance - current losses in windings.
- Rotor resistance - current losses in rotor bars and end rings.
- Windage and friction - mechanical drag in bearings and cooling fans.
- Stray load losses - magnetic transfer loss in the air-gap between rotor and stator.
IEEE Motor Tests
The motors were tested using the IEEE 112B efficiency test standard. Overall, aluminum lost 179 more watts than copper - a 14 percent difference. Stator resistance and iron core loss between the two metals were equal since the same iron laminations and stator were used for both the copper and the aluminum rotors.
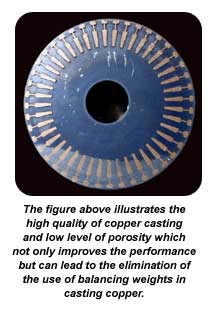
However, copper performed significantly better than aluminum in rotor resistance. Copper lost 157 watts where aluminum lost 261 watts - a 40 percent improvement with copper.
Measurements taken for windage and friction showed copper to have a 43-watt, or 37 percent, advantage over aluminum. Copper lost 32 less watts, or 23 percent less than aluminum, in stray load loss. This disparity is accounted for by the fact that copper castings had far less porosity and near-perfect balance.
An unexpected result of the tests was a large decrease in the operating temperature of the motor using the copper rotors - a drop of 4.5°C. Heat affects the life expectancy of the motor. Conventional guidelines estimate that for every 10°C hotter a motor runs, typical motor life can be reduced by half from its design point. With a reduction of 5°C in operating temperature, copper motor rotors may increase life expectancy by 50 percent.
The tests did find one negative impact on motor performance due to using the copper rotors. Starting torque is reduced 36 percent. Breakdown torque is reduced 17 percent; and locked torque is reduced 4 percent. Starting and breakdown torque levels are reduced from historically high values but are still within NEMA minimum requirements. The locked rotor torque, nonetheless, is still impressive. As the motor was not optimized for copper rotors, the torque problem can be corrected with modifications to the lamination slot design.
The level of consistency from copper rotor to rotor throughout the tests was incredibly high and not seen in aluminum die casting methods to date. The efficiency of the motors with copper rotors averaged 90.7 percent; all were within a range of 90.6 to 90.8. The process variables, such as fill rate and quenching media, had no effect on the final results. Due to the high quality of the casting with very little porosity, no balancing weights were required. If this practice could be brought to the production level, the costly balancing procedure would be eliminated. Because aluminum rotors have more variability in porosity, they are typically longer than needed to compensate for quality. Consequently, high-quality copper rotors could be reduced in stack length and provide the same efficiency at reduced material cost.
Motors Designed Around a Copper Rotor
Subsequent to the above tests, another set of tests was conducted on a series of rotors optimized for use of copper. The stator winding and iron core laminations were modified from standard motor design to gain the best possible results for the copper rotor. The results were even better than those from the previous set of tests. On average, copper rotor losses were 40 percent lower than those of an equivalent aluminum motor rotor. Total losses decreased 23 percent using the copper rotor. The operating temperature of the motor decreased even further than in previous tests. And, efficiency increased an impressive 1.6 percentage points from 90.9 to 92.5 percent.
As motors have become more efficient over the past two decades, the industry is approaching a point of diminishing returns. After the adoption of cast copper rotors, only two known technologies are left to explore that could improve motor efficiency - amorphous steel laminations and superconducting stator windings - both presently extremely expensive.
Further Developments
Testing has continued since the CDA June meeting. Independent tests were performed by a motor company that replaced their existing motor rotors with copper. The motor sizes were 3kW, or 4 hp. The efficiency test results show a reduction in overall loss exceeding 20 percent, without even measuring stray load losses. Measurements by two previous motor companies show significant improvements to stray load losses using copper rotors. Therefore, the test results for the third motor company are conservative. Reductions in losses should be greater than 20 percent using this rotor.