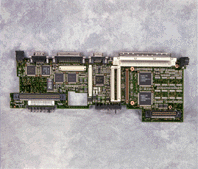
While it is rare, formed parts can develop fractures after they are placed in service. This type of failure is referred to as stress corrosion cracking (SCC). Four factors, are required before stress corrosion cracking can occur. First, the part must be stressed, either from an applied force or due to residual stress (usually from forming). Simple bending, a common practice for forming contacts, is sufficient. Second, it takes time for the fracture to occur; usually weeks or months, but it can be years. Third, SCC requires a hostile environment; ammonia, chlorides, and nitrogen compounds are particularly aggressive. Fourth, the alloy must be susceptible. The material specifier usually has little or no influence on stress, as it must be used for contact force, although residual stresses from forming can be relieved with a thermal treatment. Similarly, time is not subject to management; parts must perform for their design life.
The specifier can affect the remaining two variables, environment and alloy susceptibility, by judicious choices of alloy and coatings. For example, in hostile environments, Cu-Ni alloys are highly resistant whereas the brasses, particularly those with Zn above 15%, are quite susceptible. The designer may also elect to control the environment by plating the spring component with either Sn or Ni. Such protective coatings are effective only when the part is 100% covered and the plating is free of porosity, voids, cracks, and other defects which would impair its integrity. Because of the difficulty of obtaining defect-free plating, invasion by unwanted species is a risk, so alloy selection is the usual method to combat SCC.