Other Headlines
The breakthrough technology developed to economically die cast copper has begun to be transferred to other processes. Semi-solid metal (SSM) forming - primarily used for aluminum components - can now be used to cast copper alloys. Dr. Kenneth Young, president and CEO of V-Forge, Inc., in Englewood, Colorado, is a pioneer in SSM technology and has begun testing this process on copper alloys.
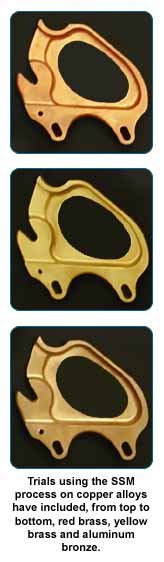
"Actually the original thrust of the work at MIT in the 1970s was directed more at high-temperature alloys such as copper and stainless steel, than aluminum," Young explained of the history of the SSM process. "The drawback was not the SSM technology per se, but the lack of a suitable die material that could withstand the high casting temperatures. So, aluminum alloys, for which there already existed adequate die technology, became the first commercial application of SSM. The latest work by the Copper Development Association Inc. and the U.S. Department of Energy in developing nickel-based dies as part of the copper motor rotor project shows the potential to finally solve the die issue," he said.
Young said that potential candidate parts for this process include those that are presently zinc die cast and then polished and plated to look like copper alloys and, also, steel parts that are either forged or machined. Young said studies show that "there is a large potential market for SSM copper alloys as well as SSM stainless steel. It appears that increasingly higher polishing standards and cost pressures even make some parts, such as those die cast and plated from zinc for things such as door handles and fittings, attractive considerations for an economical SSM copper alloy process. In steels, we saw a lot of interest in valve bodies, which today require a lot of machining."
The trials are currently focusing on both yellow and red brasses as well as aluminum-silicon bronze and alloy C90500, "which I found from our MIT work is a great model alloy with a clear microstructure enabling us to track technical progress in slurry making and part casting," he explained.
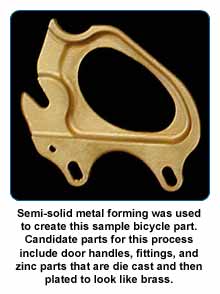
So far, no special equipment has been needed to heat the alloys. Young said that he's adapted existing aluminum heating systems for the trials. He said these systems work quite well for short trials but will eventually require redesign for prolonged running. Small diameter feedstock bars, produced according to the strain-induced mechanically alloying (SIMA) technique, is cut into small billets for insertion into the die casting machine. It is cast, then hot extruded and subsequently cold worked. "That technique was developed some time ago while I was at ITT. Recently, we have initiated testing of 'slurry on demand,' also a trend in the aluminum industry, in which attempts are being made to make slurry from liquid close to the casting machine, thereby eliminating any raw material preparation costs. We think this is essential to make a copper alloy SSM process viable," Young said.
Young is pleased with the results thus far. "The first castings show all the promise expected: smooth surface, impressive detail and replication of the die, high precision. But the proof in that pudding lies in maintaining those attributes over thousands of castings," he said.
From a metallurgical standpoint, "Dr. Elliot Brown is engaged almost full-time in evaluating our metallurgical progress. So far, we can say that we have made good slurry microstructure in our model alloy, C90500, and that the integrity of the test parts we have cast is good, with expected hardness for a rapidly quenched alloy," Young said.
The market potential for using this process on copper alloys remains to be seen. "As opposed to the aluminum case in which SSM provides mostly superior properties and performance, SSM copper will make its real mark only by offering a more cost-effective way to make existing products. That means applying a high-productivity process such as die casting to make parts hitherto made by less effective methods," he explained.
According to Edwin (Ned) Brush, senior consultant to CDA, a market study conducted by CDA found great potential for the use of the SSM process on copper alloys. "More than120 organizations were contacted for the study which focused on the potential for copper alloy die casting as an alternative to current casting, screw-machine, forging or other production techniques. Interviews indicated an enthusiastic response to and industry need for copper alloy die casting," he said.
Young is also enthusiastic. "SSM is a new technology and will require some training," he said, "but enough companies and people around the world are now practicing SSM aluminum that it is reasonable to conclude that there should be no major hiccups."