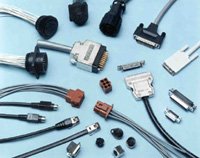
Some very basic requirements must be initially addressed. For example, will the copper alloy strip make a connector that won't overheat? Will there be sufficient contact force to provide circuit integrity? Is there enough space for the spring to deflect sufficiently to provide the minimum contact force? And, can the component parts needed for the connector be stamped without fracture? These initial concerns must be addressed to fashion a connector that will function properly and reliably immediately after manufacture. This means that a copper alloy strip must be chosen that has the optimum combination of conductivity, strength, stiffness, and formability.
It will be seen that the various copper alloy candidates for connector applications can achieve their properties in several ways which can influence the combination of properties available. The approaches used to provide strengthening include:
- the addition of alloying elements which are soluble in the base metal at connector operating temperatures, which increases strength by a mechanism called solid solution strengthening,
- the addition of alloying elements which are insoluble in the base metal at connector operating temperatures, which allows for a strengthening mechanism called precipitation hardening, or a related mechanism called dispersion hardening,
- the use of cold work, usually by rolling, to increase the strength of the strip.
Cold work can also be used in combination with the composition-related strengthening mechanisms. Most alloys suitable for the manufacture of contacts are available in a range of "tempers," which are traditional designations for describing the degree of cold work. Commonly available tempers range from "annealed" where there is no cold work after the annealing treatment, to "spring," which represents approximately 60% cold work by rolling after the final anneal. Even higher tempers can be produced, but formability may be seriously impaired, as discussed in the topics "Formability" and "Directionality of Formability."