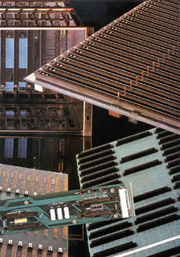
Electrical conductivity is the primary characteristic that distinguishes copper from other metals. Of the commercially useful metals, copper is only surpassed by silver. But copper alloys have a wide range of conductivity. There are hundreds of copper alloy strip metals from which to choose and some of them have conductivity as low as that of iron. Further complicating matters is that thermal and mechanical processing variations can cause profound changes in conductivity. And metals with the highest strengths often have the lowest conductivity. Such alloys might be inappropriate for high current connector applications.
The conductivity of copper alloy strip metals is measured relative to a standard bar of "pure" copper that was long ago assigned a value of 100. Thus, when brass is said to have 28% IACS, it denotes an electrical conductivity 28% of that standard. ["IACS" is the International Annealed Copper Standard]. Due to improvements in metal refining techniques, commercially pure copper today has slightly better conductivity (101% IACS) than the standard.
The Unified Numbering System (UNS) doesn't directly classify copper alloys into groups of similar conductivity. But it does define "Coppers" as those that "...have a designated minimum copper content of 99.3% or higher". It further states that "High Copper Alloys" are "...alloys with ...less than 99.3% but more than 96% ...". The copper content is fundamental to conductivity in copper alloys. However, the different alloying elements added to copper have strikingly different effects on copper's conductivity. Silver, for example, causes no measurable effect whereas minute amounts of phosphorous can severely depress the conductivity.
The thermal conductivity is also an important parameter in connector design. Within alloy families, the thermal conductivity tends to be related to electrical conductivity. Alloys of higher electrical conductivity will tend to have higher thermal conductivity. This is convenient since thermal conductivity is rather difficult to measure, while electrical conductivity, or its inverse, electrical resistivity, is easy to measure.
Alloys of higher electrical resistivity(r) will waste more energy, since heat generated due to an electric current(I) is proportional to I 2 times the resistance. More important, the heat generated will raise the temperature of the connector, with potentially adverse consequences for the characteristics of the connector and its surroundings. Higher thermal conductivity alloys allow the designer to dissipate some of that heat, minimizing temperature rise. So high conductivity is generally a sought-after property of connector alloys.