This family of alloys, which consists of copper and zinc, demonstrates that the conductivity of pure copper is often not required for connectors. More contacts, terminals, switches, etc. are stamped and formed from copper-30% zinc than from any other copper alloy. Yet its conductivity is only 28% that of pure copper. Of the various brasses, the most important for connectors are those containing 15 and 30% zinc, although a 5% zinc version is occasionally considered. It is obvious that the conductivity of these alloys is a function of the amount of zinc they contain. If the conductivity of copper-30% zinc is not sufficient, there are lower zinc brasses with higher conductivity, ranging up to 56% IACS for copper-5% zinc. There is not much to be gained in increasing the zinc content, from a mechanical property perspective. However, note that the conductivity of brass is little affected by adding zinc in excess of 28%. Because zinc has a lower metal value than copper, the higher zinc-containing brasses are usually more economical.
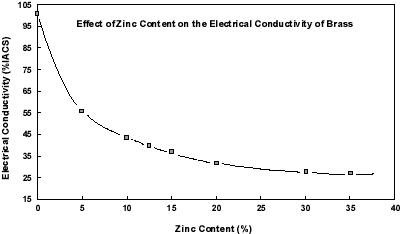
Copper-30% zinc is a good starting place when selecting copper alloys for strength and formability. This is also a good "home base" when selecting alloys for conductivity. Designers can often use their experience with copper-30% zinc to estimate just how much more conductivity they must have in a given application. If only twenty percent more is needed, then a metal with a conductivity equal to 34% IACS is required. If twice the conductivity of copper-30% zinc is needed, only copper-5% zinc will be useful among the brasses, and its lower zinc content means a sacrifice in strength. There are a number of alternate alloys to consider in such a case, from the Coppers, High Coppers, and Bronzes.