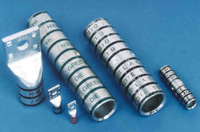
For even higher strengths, copper-nickel-tin, copper-nickel-silicon , copper-beryllium and other precipitation hardenable alloys are representative candidates. All of these alloys require special processing in order to achieve a regime of strength that can't be reached with nickel silvers, special brasses, phosphor bronze, and special bronzes. If the designer can make optimum use of the strength, conductivity and formability combinations provided by these alloys, then their higher cost per pound may be offset by the use of thinner or narrower strip to provide a greater number of connectors per pound.
The highest strength copper-nickel-tin alloy can provide twice the contact force of cartridge brass and 75% more contact force than phosphor bronze containing 5% tin, the phosphor bronze often relied upon for "good" contact forces. Similar strength can be obtained within the copper-beryllium alloy family. The precipitation-hardenable alloys can be purchased in the annealed or cold-worked condition, in which case their strengths are obtained with a "heat treatment," after parts are stamped and formed. Because this raises issues of quality control the producers of these metals also provide them with a modified process, usually referred to as mill hardened. When this is specified, no further heat treatment is required after a part is stamped and formed. In the mill hardened condition, these alloys provide less than their maximum strength, but in most cases the penalty is not severe.
Comparisons of the high strength alloys provide guidance in the selection of metals for required contact forces. If the spring is a simple flat piece with minimal forming requirements (for example, a relay spring riveted in place at the fixed end to a flat base), then contact springs with high strengths probably can be successfully manufactured, because formability is of little consequence. But if the spring is an integral component of a box terminal or there is simply a need to make a 90 bend on one end for insertion into a housing, the strongest tempers of these alloys might not form without failure. Formability then becomes a selection criterion as is described in the topics "Formability" and "Directionality of Formability."