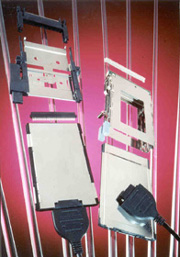
There are several specially-designed bronzes, brasses and copper-nickel alloys, many of which are widely used for connectors. The nickel silvers (copper alloys containing nickel and zinc) are also part of this alloy group; none of them has more than 10% IACS. The nickel-containing alloys are excellent choices when strength and stability at elevated temperatures are required. Conductivity is usually sacrificed at the expense of strength. Nickel-silicon alloys somewhat overcome this problem. They develop high strength while maintaining conductivity. This is accomplished with special processing, i.e., precipitation hardening, which effectively reduces the nickel in solid solution.
Many newer connector metals are produced by alloying tin, zirconium, iron, beryllium, cobalt, aluminum, silicon, magnesium, and/or phosphorous with copper. The wide range of conductivity possessed by these alloys is a consequence of the diversity of the alloying elements and strengthening mechanisms. One copper-zirconium alloy has almost the conductivity of pure copper but certain copper-silicon and copper-nickel alloys, at the other end of the spectrum, have only 1/10 as much. Many of these metals were developed during the 1970's and 1980's with specific market niches in mind. Computer components and electronic automotive components are frequently fashioned from these alloys.