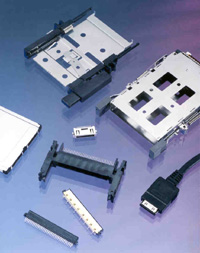
In conjunction with the prime finish indicated above, under-plates are used to enhance their performance. Without an under-plate, the prime finish would be plated directly over base metals. This could result in a number of failure mechanisms to be generated:
- Diffusion of Copper through Gold
- Increase Wear
- Diffusion of Zinc (certain brass alloys)
- Copper/Tin Intermetallic Formation
- Sensitivity to Base Metal Pore Corrosion
- Process Related Problems
Three basic under-plates were or are now in use in contact systems.
Silver
This was the predominate under-plate in the early 60's. However, it was found that silver migrated through gold and formed disruptive films on the contact surfaces or at the very best cosmetic discoloration. Silver as an under-plate is no longer in use.
Copper
- Acts as a leveling medium.
- Will cover substrate surface defects hence reduction of porosity.
- Acts as an internal diffusion barrier (through gold)
- Will diffuse through gold.
- Will form intermetallics with tin (alloys).
- Very compliant relevant to pre-plated material and crimp applications.
This under-plate is only used in a few applications due to diffusion tendency and tin/copper intermetallic formation. Leveling results in the reduction of porosity by tending to create a smoother surface. It does not however, enhance wear resistance or increase corrosion resistance.
Nickel
This is the most common and important under-plate in current use.
- Acts as a leveling medium.
- Will cover substrate surface defects hence reduction of porosity.
- Acts as an internal diffusion barrier (Zn and Cu through gold).
- Acts as an external diffusion barrier to prevent pollutants from reacting with base metals.
- Increases wear resistance.
- Increase corrosion resistance.
- Will eliminate Cu/Sn intermetallics.
However, there are some cautions which must be taken when using nickel under-plates.
- Ductile nickel should be used. Some nickel baths result in brittle conditions to exist. This has implications in crimp applications and when pre-plated materials are used.
- Some nickel baths are stress related increasing potential residual stresses in contacts.
- The thickness of the under-plate must be controlled. It should not be < 50 micro-inches for porosity reasons. It should not be >150 micro-inches as it can start to have an impact on the "composite" modulus of elasticity. This could adversely effect spring rates and other mechanical features such as mating forces.
Nickel will also diffuse through gold and form nickel/tin intermetallics. The diffusion and intermetallic growth rates are very slow and under normal application environments pose little or no potential functional problems.