To understand the contact material system selection, it is necessary to understand the separable contact interface. It is composed of two surfaces in contact with each other. These surfaces are composed of "peaks and valleys" with the peaks generally contacting the opposite surface. These peaks or asperities are called 'a' spots. It is through these 'a' spots that the signal or current passes from one element to another. Thus the real area of contact is a small portion of the apparent area of contact as shown in the figure below.
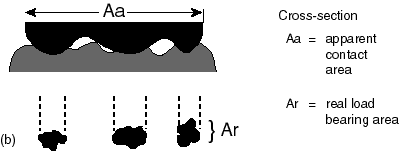
A signal or current will flow or constrict through the 'a' spots as shown in the figure below. Their effectiveness is contingent on the magnitude of contact force that tends to flatten the peaks allowing a wider area of contact to exist.
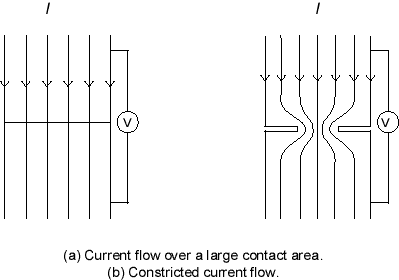
In essence the current or signal passing through an 'a' spot will decrease as the number of 'a' spots increase, thus decreasing the resistance (signal loss) and localized frictional heating caused by election movement (temperature rise). High normal force results in a greater number of 'a' spots. Multiple contact elements will also increase the number of 'a' spots.
The figure below illustrates the relationship between normal force and resistance of a single element. As can be seen, low normal force results in only a few 'a' spots creating a high resistance. As force increases, the number of 'a' spots increase and resistance decreases ultimately reaching a point of diminishing returns (flat portion of the curve).
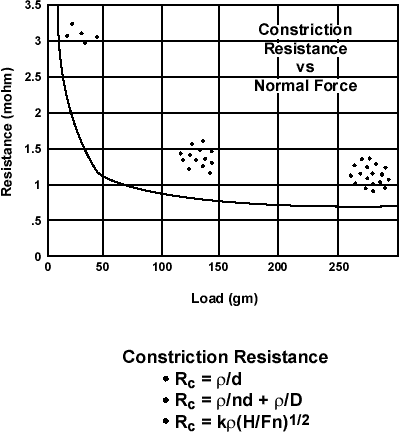
For a contact system to function properly, the forces generated should be in the flat portion of the curve. For base metal contacts (with no protective finish), the force must be high enough to displace or penetrate surface oxides (normally 3 to 4 pounds). In the vast majority of connector products, this is impractical and a protective finish system is required.