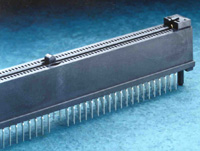
Photo ©1998 AMP INC.
Copper alloy strip used for connector components is often supplied with a tin coating. Tin offers corrosion protection, preserves solderability, and provides a better contact surface than bare copper metals. Tin plated strip is readily available from both metal producers and independent platers. Basically, tin coatings are produced by either dipping the strip metal in molten tin or by an electrolytic or plating process. The tin applied in a molten bath can be mechanically wiped smooth and is defined as "Commercial Hot Dipped Tin" (HDTc). Or it can be wiped by an air jet; defined as "Air Leveled Tin" (ALT). Electroplated tin, called "Electrotinned" (ESN), products can be heated to remelt the tin surface and thus produce a derivative product called "Reflow Tin" (Reflow).
Commercial Hot Dipped Tin is the most prevalent kind and is the lowest cost tin plate. Air Leveled Tin may appear cleaner and brighter than Commercial Hot Dipped Tin. Electrotinned is typically produced with a copper flash underplate. For Reflow Tin, electroplated strip metal is fed through a furnace where the tin is remelted and subsequently solidifies into a smooth, bright, almost mirror finish. Because Reflow Tin is an electroplate converted to "hot tin", it has characteristics of both.
The tin coating on all of these products is elemental tin, or a tin-lead alloy, but there are other differences. Commercial Hot Dipped Tin is not consistently bright and typically there are lines in the longitudinal direction from the physical contact of the wipes. Air Leveled Tin appears brighter and more uniform because it's leveled by air rather than by mechanical contact. Electrotinned is produced with both a bright surface and a dull (matte) surface. Organic brighteners are used for the former to prevent the formation and growth of tin dendrites (that produce the matte surface). The matte surface doesn't have the cosmetic attractiveness of the bright tin, but it avoids the films that can result from the use of the brighteners. Reflow tin has an attractive appearance; it looks smooth and bright.
The thickness of the tin plates from these different methods are not the same. The grain size of the Electrotinned is smaller than that of the other tins. And, there are differences at the interface of the tin and base metal alloy. These differences have significant roles in contact performance and reliability.