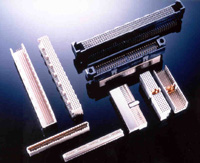
Copper-tin intermetallic compounds form at the interface of the tin plate and the base metal, for all of the different processes used to tin copper alloy strip. With both time and temperature, the intermetallic grows to the surface, becomes oxidized, and can affect contact integrity.
Because Commercial Hot Dipped Tin already has some intermetallic compound at the surface when produced, its service life is likely to be the shortest. After three months in storage at summer temperatures, practically all of the surface could be compound.
Electrotinned products, relatively free of intermetallic when plated, offer longer service life. But after four weeks (without elevated temperature) about 25µ-in can be detected at the copper-tin interface. This too, will eventually grow to the surface. The growth rate of the intermetallic on Electrotinned is more rapid than for that on Air Leveled Tin and Reflow Tin (and Commercial Hot Dipped Tin). Their cast micro structures with big grains inhibit intermetallic growth at moderate temperatures. Longer service times are afforded (or thinner tins can be used for equivalent performance).
Intermetallic growth can be retarded by using a "barrier metal" (a metal that diffuses much, much, more slowly with the base alloy and the tin). Nickel has long been plated under gold to act as this diffusion barrier and it is similarly effective for tin plating. A barrier layer may significantly slow the diffusion of elements other than copper, for example, zinc (zinc oxides at the contact surface are resistive). A copper underplate will prevent or impede zinc from reaching the surface; 20µ-in is often used on Reflow Tin products. For brasses, 100µ-in of copper is effective. Copper underplate is not an effective means to prevent Cu-Sn intermetallic at the surface. Diffusion barriers are often used on Electrotinned and Reflow Tin. Incorporation of a barrier for Commercial Hot Dipped Tin and Air Leveled Tin would require a separate operation.