Copper Protects Historic Shipwreck
Copper cladding preserved the rudder on The Republic, a steamship that sank off the coast of Georgia shortly after the Civil War (photo below). Copper cladding also protected the ship's hull from barnacles and other biofouling during its time at sea. But, because sea worms could attack the hull from the inside once the ship sank, the wooden hull disintegrated. Odyssey Marine Exploration, Tampa, Florida, searched for and found the wreck because it contains gold coins now believed to be worth about $150 million.
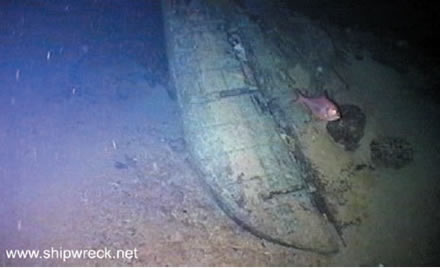
The paddle-wheel-propelled ship had quite a history. Launched in Baltimore in 1853 as the S.S. Tennessee, it was at first in service to Central America, hauling, among other passengers, those bound for the California gold fields.
In 1861, the ship was seized by the Confederates, who hoped to use it to run the Union blockade. The following year, when Union forces captured New Orleans, they found the ship crammed with cotton. After they mounted heavy guns on the ship, it became the flagship of Admiral Farragut (of “Damn the torpedoes, full speed ahead” fame). He sailed it up the Mississippi in his successful campaign to split the Confederacy.
Hulls Sheathed inCopper
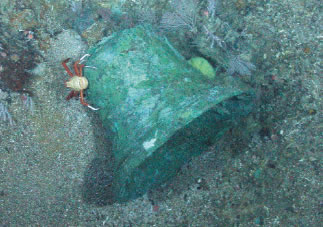
By the time of The Republic's construction, sheathing hulls with copper was a common way to repel barnacles–the first ship so protected was the Royal Navy's frigate Alarm way back in 1761. At first, the sheathing was attached with iron nails, which caused galvanic corrosion of the nails. It took another 20 years before copper nails were substituted for iron.
The technology to prevent biofouling of seagoing vessels has since progressed. Later iterations, such as the Miss Revere in 1941 and the Copper Mariner in 1964, introduced copper-nickel as a hull-sheathing material. This resulted in lower maintenance costs, lower fuel bills (due to much less drag) and a net saving over the life of the vessel, even considering the cost of fabricating the hull itself.
The latest sheathing method, developed in 1989, is called Cuproguard. It uses adhesivebacked copper-nickel foil, quilted into small squares that are electrically separated from each other. This minimizes any galvanic deterioration and makes the overall sheet pliable and easy to mold to the shape of a hull and hull fittings. It is lightweight and cost-effective, and, after more than a decade of testing on the yacht Slim Chance, the copper-nickel hull application continues to perform and protect.
Odyssey Marine Exploration
Cuproguard
Copper-Nickel Web site
Also in this Issue:
- Copper Imparts Distinction to Building Interiors
- Copper Protects Historic Shipwreck
- Copper Enhances City Hall
- Structured Wiring Benefits Homeowners and Others
- Backup Power Systems Pay Off