Copper Wire Ensures Performance of New Antilock Brake System
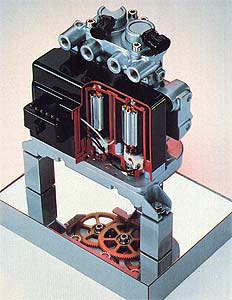
By the mid-1990s antilock brake systems (ABS) will be available on all General Motors vehicles. And nearly two pounds of copper wiring will make each system functional, according to William H. Gillespie III, product manager for antilock brake systems at the Delco Chassis Division of General Motors Corporation, Dayton, Ohio.
In addition to copper wiring, brass screw machine parts, such as hydraulic line connectors, are used by various auto makers for their ABS systems.
Copper wire is needed in several areas of the Delco system: the wiring harnesses between the wheels and the system computer and from the computer to a unit called the hydraulic modulator; the windings on three direct current motors at the hydraulic modulator; and the copper-wound speed sensors located at each wheel. According to Gillespie, cost, reliability and performance were the criteria for choosing copper.
New ABS units from Delco Chassis are currently installed in 15 different 1992 GM models from Chevrolet, Pontiac, Buick, Oldsmobile and Saturn. With ABS, wheel lock is minimized, improving the driver's ability to stay in control of the car during difficult braking situations and decreasing stopping distances on most surfaces.
"This is accomplished," Gillespie says, "through a sensor located at each wheel which transmits information to a computer. When the computer detects the wheel is about to lock, it eases pressure to the brake to minimize lockup. The action occurs repeatedly, and the result is like an automated pumping of the brake at a rate far more rapid and precise than even the most experienced driver could deliver in an emergency."
Delco Chassis' new ABS VI system adjusts brake line pressure by using three motor-driven pistons in a hydraulic modulator. When the computer decides that antilock control is needed, an electromagnetic brake on each motor is released, allowing them to spin independently at up to 7,000 rpm.
The motor drives the pistons down through a gearbox and screw jack mechanism from the full upright position, seating a check valve that seals the system. A solenoid isolates the action at the modulator from the brake pedal.
"All the driver feels is a gentle quivering of the brake pedal, not the staccato sequence of solenoid valves popping open and closed," Gillespie says. The more the pistons move down, the larger the chamber's volume, reducing brake pressure along the way. When the tires regain adequate traction, the piston moves up to reapply the brakes.
"We're not limited to an on-off action," Gillespie explains. "We can adjust brake pressure to exactly what is needed." And two pounds of copper wire enables it to do its thing.Also in this Issue:
- NASA Relies on Copper for Shuttle Engine
- Copper Buffalo to Roam Wyoming
- Demand Increases for Copper Busbars
- Solid Brass Padlocks Now Available to Consumers
- Special Coatings, Packaging Products Keep the Shine on Copper and Brass
- Copper Use in Autos Up 40 Percent
- Copper Wire Ensures Performance of New Antilock Brake System
- Copper to Replace Aluminum in New Chip Technology