Introduction to Brasses (Part I)
Copper Applications in Metallurgy of Copper & Copper Alloys
Introduction to Brass | Why Make it in Brass? | Cost Effectiveness | Types of Brass | Effect of Zinc Content | The Alpha Brasses | High Copper Brasses
An overview of the large and industrially important family of alloys based on copperand zinc. The article is especially recommended to designers, engineers and others who specify materials for manufactured products. A brief history of brasses is included for those interested in learning about these interesting alloys. Links are provided to sources on The Copper Page and other websites where more detailed information can be obtained.
Introduction 
Brass is usually the first-choice material for many of the components for equipment made in the general, electrical and all precision engineering industries. Brass is specified because of the unique combination of properties that make it indispensable where a long, cost-effective service life is required. This combination is matched by no other material.
The word "brass" covers a wide range of copper-zinc alloys with differing combinations of properties, including
- Strength
- Ductility
- Hardness
- Conductivity
- Machinability
- Wear resistance
- Color
- Corrosion resistance
- Recyclability
Combinations of these properties result in unique structural materials. For example:
- The machinability of brass sets the standard by which other materials are judged.
- Brasses can easily be cast to shape or fabricated by extrusion, rolling, drawing, hot stamping and cold forming.
- Brasses are ideal for a very wide range of applications
- Brass products can often be used without needing extra surface protection.
- Brass is frequently the material to select to make the least costly machined products.
To suit every need, there are very many standard compositions for brass, with copper contents ranging from 58% to 95%. Apart from the major alloying element, zinc, small additions (less than 5%) of other alloying elements are made to some brasses to modify their properties so that the resulting material is fit for a given purpose. Selection of brass is covered under Types of Brass.
Form | Cold-Working Brasses | Free-Cutting Brass | High Strength Brasses | High Corrosion Resistance Brasses |
---|---|---|---|---|
Rods | Rivets, pinions, motion sensors | Unions, terminals, spindles, screws, jets, injectors, cable glands, automotive sensors and other under-hood components | Valve spindles, shafts | Marine fittings, plumbing fittings, gas fittings, pneumatic fittings |
Sections | Bathroom hardware | Terminals, tacks, valve bodies, balance weights | Valves, spark resistant mining components | Shower parts |
Hollows | Automotive components | Nuts, cable connectors | Bearings | Nuts |
Hot Forgings (Stamp- ings) |
n/a | Tube fittings, electrical components, plumbing hardware | Synchromesh gear rings, cavity wall ties, mining equipment | Plumbing fittings |
Plate | n/a | n/a | n/a | Condenser tubesheets |
Sheet | Hollow ware, lamp caps, reflectors | Clock plates, instrument frames | n/a | Instrument cases, cartridge cases |
Strip | Springs, terminals, fuse caps, bellows, precision etchings | n/a | Wear plates & strips | Heat exchangers |
Wire | Springs, pins, rivets, Zippers, jewelry | Screws, Terminals | n/a | Scouring pads, papermaking screens, brake pad carrier wire |
Tube | Heat exchanger tubes | See hollows | n/a | Heat exchanger tubes for corrosive environ- ments |
Castings | n/a | Taps, water fittings | Bearings | Valve bodies |
Why Make it in Brass? 
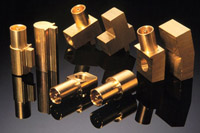
Brass is the best material from which to manufacture many components because of its unique combinations of properties. For example, good strength and ductility are combined with excellent corrosion resistance and superb machinability. Brasses set the standard by which the machinability of other materials is judged and are also available in a very wide variety of product forms and sizes to allow minimum machining to finished dimensions. Brass's availability in near net shapes can result in significant production cost savings.
As rod or bar, brasses are readily available from manufacturers and metal distributors. For longer runs, it is frequently worth considering the purchase of special sizes or extruded shapes designed to minimize machining costs. Brass rod manufacturers are able to produce a very wide variety of shapes and sizes of product—commonly called "shapes" or "profiles"—with minimum order quantities that are very low compared with many other materials. Custom-shaped profile dies are not very expensive, and many styles can be produced and be ready for use within a few days.
Die costs for special extrusions are especially inexpensive when spread over a long production run, particularly if they do away with machining or assembly operations. Hollow extrusions, for example, can save excessive boring operations. As in the case of extrusions, die costs for hot forgings are much lower than those for die casting or injection molding techniques used with aluminum, zinc alloys or plastics. For special shapes, hot stampings can provide a very economic feedstock. Manufacturers welcome discussions regarding optimum alloy, sizes and tolerances at an early stage in the design of components. Brasses, having various combinations of strength and ductility, corrosion resistance, machinability, conductivity and many other attributes are very widely used in the manufacture of components and finished goods. Alternative materials can be considered but it must be remembered that the main criteria to be assessed are those that effect the overall lifetime cost-effectiveness rather than first cost or raw material cost.
The off-the-shelf price of brass may sometimes be higher than some alternatives, especially leaded steels, but the raw materials cost is only part of the overall cost picture. The higher production rate that brass allows, the availability of brasses in precise near net shapes such as extrusions, hot stampings and die castings, plus the considerable value of recycled scrap and turnings often results in items made from brass costing less than those in other apparently lower cost materials. Brasses also frequently offer better and longer service performance, avoiding consequential service and guarantee claims.
Cost Effectiveness 
Here are many factors, sometimes overlooked, that contribute to low costs of brass components.
- Ease of machining means that production costs can be minimized.
- Close tolerance manufacturing techniques can be employed so that finishing costs are minimal.
- Tooling costs may be much lower than for other materials or processes.
- The good corrosion resistance of the brasses means that the cost of protective finishing is lower—or nonexistent—than for many other materials.
- The high value of process scrap and turnings can be used to reduce production costs significantly.
- The long service life normally expected of well-designed brass components means that the costs of service failures are minimal.
For any product, the first cost is important but not necessarily paramount when fitness for purpose must be assured. Life-cycle costing can be used within parameters set up in an organization to monitor cost-effectiveness. The costing of component production depends on many factors, among which are:
Product First Cost
The first cost of a product, put simply, is the starting cost of buying the material plus the production costs to make the item. Lowest material costs may not give the lowest-cost product because production costs can be higher. Free-machining brass costs so little to process that it frequently gives the cheapest and best product. It is also frequently possible to reduce total costs by buying free machining material or components specially supplied in near net shape before finish machining and assembly.
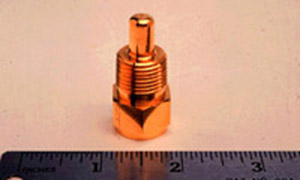
A simple example of comparison of material and first costs for heavy-duty valve chests, or manifolds, is shown in the box, courtesy of Meco International. The requirement here is to produce a reliable, robust and safe valve chest for the operation of mine roof support hydraulic jacks. When made from steel, the amount of pre-machining from bar stock is extensive, the finish machining time extended and there is also a need to send out the components for protective plating. High strength brass is supplied to the required shape, is relatively easy to machine and requires no plating in order to be safe for this application.
Comparisons | High Strength Brass | Steel |
---|---|---|
Design Requirements | ||
Working Pressure (psi) | 5,076 | 5,076 |
Non-sparking for mining applications | Yes | No |
Cost per component ($) | ||
Raw material | $9.95 | $3.76 |
Pre machining | 5.60 | |
Milling | 4.00 | |
Finish machining | 12.64 | 18.72 |
Plating | 2.26 | |
Total cost per component | $22.59 | $34.34 |
Additional manufacturing cost comparisons can be accessed in our section devoted to free-cutting brass (Alloy C360).
Life-Cycle Cost
The life-cycle, or total lifetime cost of a product is defined as the first costs plus servicing cost and costs of failure during component life. Well designed and specified components can be cheaper if they last their full expected life than if designed only for lowest first cost.
Material Cost
A product's material cost component is the cost of the metal mixture plus casting and fabrication costs, less value of reclaimed process scrap. This, however, is only a part of the production cost of components. Careful consideration of material costs can reduce total costs. The usual option is to buy free-machining brass in stock sizes, but if quantities justify, it is frequently worth paying more for special profiles that give more significant savings on production and assembly costs.
Economic Order Size
For wrought material stock, large orders can be placed directly with material manufacturers—brass mills—who are pleased to supply direct and frequently make material that is specially designed to suit requirements agreed with the customer. These can include variations on attributes included in Standards, properties not normally quantified under Standards requirements or manufacturing to other individual specifications. Minimum order quantities depend on production considerations including optimum batch sizes and the programming requirements needed to meet any special orders. The minimum order accepted by brass mills may thus vary from mill to mill but can be on the order of 5,000 pounds.
Small quantities of materials are bought from metal distribution houses rather than brass mills. This is because it is economic for manufacturers to make material in long runs of large quantities and distribute these to a variety of distributors in different areas. Distributors themselves have different specialties, many being able to offer cutting to size or other services as required.
Availability in a Wide Range of Forms
The hot and cold ductility of the brasses makes them amenable to all of the conventional metal forming processes. They are also easily cast. From the range of compositions, standardized alloys can be selected for:
- Extruded rods and sections (solid and hollow)
- Hot stampings and forgings
- Rolled plate, sheet, strip & cut circles
- Drawn tubes—round and shaped
- Drawn wire—round and shaped
- Castings—sand, shell, investment, permanent mold (gravity and pressure-die)
Strength
In the softened or annealed condition, the brasses are ductile and strong but when hardened by cold working processes such as rolling or drawing, their strength increases markedly. Strong, stiff structures can be assembled from extruded-and-drawn sections. Bars and rolled sheet and plate can be fabricated into containers and other items of equipment which work under pressure. The strength of brasses is substantially retained at temperatures up to around 200ºC (3900F) and reduces by only about 30% at 300ºC (5700F), which compares favorably with many alternative materials, and easily exceeds the properties of plastics. The brasses are very suitable for use at cryogenic temperatures since the properties, especially strength and toughness, are retained or slightly improved under these conditions.
For applications demanding higher strengths, the "high strength brasses" are available. These contain additional alloying elements such as manganese, which further improve the properties. Some high strength brasses attain strengths that are comparable with steels.
Ductility and Formability
Brasses with a copper content greater than 63% can be extensively deformed at room temperature, and are widely used for the manufacture of complex components by pressing, deep drawing, spinning and other cold forming processes. If the copper content is below 63% and no other alloying elements are present, the room temperature ductility is reduced, but such alloys can be extensively hot worked by rolling, extrusion, forging and stamping. Strength, ductility and formability are retained at low temperatures, making the alloys ideal for cryogenic applications.
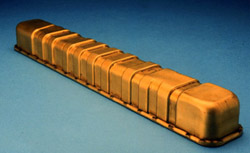
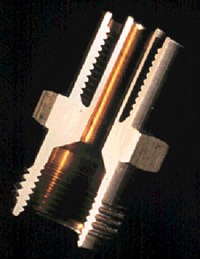
Machinability—the standard by which others are judged
While all brasses are intrinsically easy to machine, the addition of small amounts of lead to brasses further improves this property and the well-known "free cutting brass" (UNS Alloy C36000) is universally accepted as setting the standard by which other materials are judged when machinability is being assessed. Higher machining speeds and lower rates of tool wear mean that overall production costs are minimized, tolerances are held during long production runs and surface finish is excellent. You can access a number of interesting articles on the properties and application of free-cutting brass by clicking here.
Corrosion Resistance
Brasses have excellent resistance to corrosion that makes them a natural, economic first choice for many applications. Atmospheric exposure of the brasses results in the development of a superficial tarnish film. Outdoor exposure will ultimately result in the formation of a thin protective green "patina" which is frequently seen as a visually attractive feature in buildings, but the brass will remain essentially unaffected for an unlimited period of time, i.e. it will not rust away like iron and steel. Seawater can be handled successfully providing the correct alloy is chosen, and there is a long history of the use of brass tube and tube fittings, valves, etc. in domestic plumbing, central heating, seawater lines, steam condensers and desalination equipment. High strength brasses containing manganese have particularly excellent resistance to atmospheric corrosion, continual exposure resulting in a gradual darkening of the bronze color.
Conductivity
Brasses have good electrical and thermal conductivities and are markedly superior in this respect to ferrous alloys, nickel-based alloys and titanium. Their relatively high conductivity, combined with corrosion resistance, makes them an ideal choice for the manufacture of electrical equipment, both domestic and industrial. Condenser and heat exchanger tubing also require the good thermal conductivity of copper and its alloys.
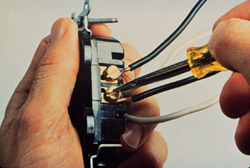
Wear Resistance
The presence of lead in brass has a lubricating effect that gives good low friction and low wear properties utilized in the plates, pinions and gears used in instruments and clocks. Special brasses are available with additions of silicon that make the material ideal for use in heavy-duty bearings.
Spark Resistance
Brasses do not spark when struck and are approved for use in hazardous environments.
Magnetic Permeability
Brasses are essentially non-magnetic, a property which has gained them extensive use in electrical and electronic equipment, as well as instrumentation such as geological and survey equipment.
Attractive Color
Copper and gold are the only two metals with any distinctive color. In brasses, the red of copper is toned to a range of attractive yellow hues by the addition of varying amounts of zinc, ranging from the gold-like colors of the 95% copper/5% zinc (95/5), 90 /10, 85 /15 and 80 /20 alloys (appropriately called "gilding metals") through the more subtle variations in the 70 /, 67 /33 and 64 /36 series of brasses to the stronger yellow color of the 60 /40 alloy, which was formerly known as "yellow metal." (Standard designations for these alloys are given later in this article and are described in greater detail in the Standards and Specifications section.) As a result, brasses are extensively used for durable decorative applications and for the manufacture of functional items where, in addition to a long service life, aesthetic appeal is a requirement. Aluminum brasses have a distinctive silvery sheen and the addition of manganese to some brasses gives them an attractive bronze color when extruded. High strength brasses, some of which are otherwise known as "manganese brasses" or previously "manganese bronzes" are particularly suitable for architectural applications since they can also be patinated to a range of durable brown and bronze finishes.
Decorative or protective finishing is easily applied
Brasses may be polished to a high surface finish which can then be either easily repolished when required or lacquered—preferably with a lacquer containing a tarnish inhibitor such as benzotriazole—to preserve the natural color, enameled or plated with chromium, nickel, tin, silver, gold, etc. as required. Alternatively, the surface can be toned to a range of colors, from "bronze" through various shades of brown, to blue-black and black, using commercially available toning chemicals. These colored finishes are frequently used for decorative and architectural metalwork.
All types of common plating processes may be used. For many other metals it is usual to use a copper plate underlayer. This extra step is not required on brass because the metal is easily polished and does not need the expense of an initial copper strike. To give additional corrosion protection to steel when used against brass, cadmium plating of the brass was once traditional, but zinc is now generally used for this purpose.
Ease of joining
Brasses may readily be joined to other copper alloys or to other metals by most of the commercial joining processes such as riveting, soft soldering, silver brazing and friction welding. Adhesive joining practice can also be used.
Hygiene
Copper is well known as a biocide and the copper content of the brasses has the beneficial effect of restricting the growth of micro-organisms. Tests on door hardware such as knobs and kick plates have shown that those that are made of brass are far less likely to encourage the growth of the organisms causing nosocomal infections than other materials. Brass fittings, free from further protective finishes, should therefore be used in sensitive environments such as hospitals.
Properties not Considered
When selecting brasses to suit end uses there are many possible combinations of properties to be considered. However, some properties associated with alternative materials, including plastics, need not be considered for brass.
These include:
- Loss of properties at slightly elevated operating temperatures (less than 300ºC or 5700ºF)
- Rusting
- Corrosion under plating
- Poor conductivity
- Rapid formation of a non-conducting oxide layer
- Degradation by sunlight
- Embrittlement following migration of plasticizer
- Poor impact resistance
- Initial outlay for expensive molding tools
Types of Brass 
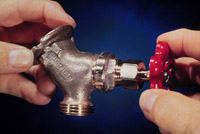
Brasses are copper alloys in which the principal alloying constituent is zinc. Their properties depend primarily upon the proportion of zinc present but can be usefully modified by the introduction of additional elements to further improve specific characteristics such as strength, machinability or resistance to particular forms of corrosion.
The principal cast and wrought brass compositions in commercial use are listed in Standard Designations for Copper and Copper Alloys—Wrought and Cast. Similar information, in English, can be found on the websites of the Copper Development Association (UK), the Canadian Copper and Brass Development Association, the International Copper Association South East Asia and the Asian Copper Information Centre.
There are also alloys not commonly described as brasses but which are similar to them in many respects. These include the nickel silvers (which generally contain more zinc than nickel) and the so-called bronze-welding filler alloys. In North America, a casting alloy containing 5% each of zinc, tin and lead is the most commonly used alloy of the types known as "red" brasses. In the Europe and elsewhere this alloy is classified as a leaded gunmetal. These casting alloys are not covered in this introductory article.
Effect of Zinc Content 
Selecting the appropriate brass for any particular service from the range presented is simplified by division into the so-called alpha and alpha-beta brasses. When up to about 35% zinc is added to copper it dissolves to form a solid solution of uniform composition designated alpha. Further increase in zinc content produces a mixture of the original solid solution and a new solid solution of higher zinc content known as the beta phase.
Brasses containing between about 35% – 45% zinc consist of mixtures of these two phases and are known as alpha-beta or duplex brasses, the ratio of alpha to beta phase depending principally upon the zinc content. The inclusion of certain third elements—particularly aluminum, silicon or tin has the effect of increasing the beta phase content for any particular zinc content.
The presence of the beta phase in the alpha-beta brasses gives reduced cold ductility but greatly increased amenability to hot working by extrusion or stamping and to die casting without hot cracking, even when lead is present. The alpha-beta alloys are also stronger and, since they contain a higher proportion of zinc, cheaper than the alpha brasses. They do however, show higher susceptibility to dezincification corrosion and are therefore less suitable for service under conditions where this type of attack is likely to occur.
The Alpha Brasses 
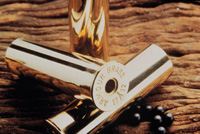
The range of alloys known as alpha brasses or cold working brasses, contain a minimum of 63% copper. They are characterized by their ductility at room temperature, and can be extensively deformed by rolling, drawing, bending, spinning, deep drawing, cold heading and thread rolling. The best known material in this group contains 30% zinc and is commonly called 70/30 or cartridge brass, (UNS Alloy C26000) due to the ease with which the alloy can be deep drawn for the manufacture of cartridge cases. The cases (up to 4 in (100mm) in diameter or more) start as flat discs blanked from strip or plate and are successively formed to the final shape by a series of operations carried out at room temperature which progressively elongate the sidewalls and reduce their thickness. Alloy C26000 possesses the optimum combination of properties of strength, ductility and minimal directionality which make it capable of being severely cold drawn. Its ductility allows cold manipulation and the alloy has better corrosion resistance than the brasses with a higher zinc content.
For long production runs of deep-drawn components it is essential to keep the process well monitored. The tooling and lubrication must be well maintained and arrangements made to ensure a consistent supply of feedstock. Deep drawing properties are controlled by alloy composition and trace impurities and mechanical and thermal history during manufacture. Good agreement should be reached with reputable suppliers regarding quality assurance.
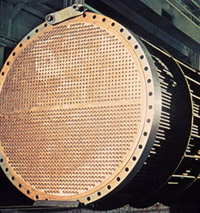
Because of their high thermal conductivity, adequate strength, good corrosion resistance and natural anti-fouling properties, brasses and other copper alloys have long been used in heat exchangers and condensers. The tube and tube sheet alloys normally have different compositions but are generally compatible with each other from the standpoint of galvanic effects.
Tubes for heat exchangers are frequently manufactured from the alpha brasses, normally of 70/30 composition but often containing alloying additions which enhance corrosion resistance. Tube sheets are made from a variety of copper alloys (depending on service conditions), among which are brasses containing 60% copper and 40% zinc, plus other elements as appropriate. Substantial quantities of alpha alloys are also used for the manufacture of fasteners such as wood screws, rivets and zippers.
For less demanding fabrications such as spring contacts in a domestic electrical socket, an alloy with a higher zinc content (and hence lower price) can be used, such as yellow brasses, a series of alloys containing between 63-66% copper and 34-37% zinc, and bearing UNS designations between C26800 and C26400. These alloys are not quite as ductile as 70/30 brass although other mechanical properties are similar. They are perfectly adequate for all but the most severe cold working operations.
High Copper Brasses 
Alloys with higher copper contents (80 to 90%) closely match gold in their color. In the UK, they are traditionally known as "gilding metals," whereas older U.S. nomenclature refers to them as "gilding" (95/5, UNS C21000), "commercial bronze" (90/10, C22000), "jewelry bronze" (87½/12", C23000), "red brass" (85/15) and "low brass" (80/20, C24000). They are used for the manufacture of decorative metalware and roll-formed sections for architectural applications as well as costume jewelry, badges, buttons etc. For this latter use they are often chemically toned to a "bronze" finish. They are sometimes collectively known as "architectural bronzes." This term can cause confusion with the high tensile brass extrusions normally made for architectural purposes (the "manganese brasses") and the standard designation should therefore be quoted.
Gilding metal or "cap copper," 95/5, C21000, has good ductility and corrosion resistance, but it is only rarely used other than for caps for ammunition.
Also in this Issue:
- Brief Early History of Brass
- Introduction to Brasses (Part I)
- Speeding-up Your Computer in the 21st Century Using Copper ICs
- Spotlight on Copper In Architecture
- Introduction to Brasses (Part II)
- Copper Cleans Up