FEV is an internationally recognized powertrain and vehicle engineering company that supplies the global transportation industry with advanced testing and instrumentation products and services.
Gary Rogers, Chief Executive Officer and President of FEV, Inc., talked recently about the company's beginnings and its unique role in the evolution of the automotive industry toward vehicle electrification.
Prior to founding FEV's North American operations, Rogers was the Director of the Power Plant Engineering Services Division for a company called Failure Analysis Associates (now called Exponent Corporation), performing forensic engineering analyses and failure prevention assessments in the fossil fuel and nuclear electric power industry. In that role, he hired Professor Franz Pischinger to consult on failures of emergency diesel generators in nuclear power stations. At the time, Prof. Pischinger headed the Institute for Applied Thermodynamics at the Aachen Technical University in Aachen, Germany and had previously founded FEV in 1978. "He asked me whether I would be interested in starting a U.S. daughter company for his little startup, which was called FEV Motorentechnik GmbH. And so 25 years ago last April, I decided to get out of analyzing things that broke and try to design things that don't break."
Innovations in Testing
In 1985, Rogers founded FEV's North American operations in Palo Alto, CA. The company relocated to suburban Detroit in 1988 and continually expanded until 1997 when FEV constructed and opened its North American Technical Center in Auburn Hills, Michigan. Today, FEV provides OEMs with the latest technology in powertrain design and development services, as well as extensive testing capabilities. "The company has grown from about 50 people in Germany and one in the U.S. to almost 2,000 people now," says Rogers.
FEV's latest innovation in testing facilities is state-of-the-art Hybrid and Electric Vehicle Development Center, completed in March of 2009. The center is the location of the company's battery management system development and testing facility, and a dedicated chassis dynamometer for hybrid and electric vehicle testing. The testing facilities are at the heart of why FEV has a reputation for rapid innovation. They are the source of many of the innovations the company has helped manufacturers bring into production.
BMW X6 Crossover Hybrid-Electric Vehicle
The BMW X6 Crossover hybrid-electric vehicle is one example of how FEV testing facilities provide OEMs with a wide range of design and analysis capabilities. "We were able to bring together new algorithms for optimizing the calibration of the vehicle," says Rogers. "The testing allowed us to bring that system into production much more quickly than it would otherwise have been. Prior to that, you could spend as much time calibrating the system as you spent designing it and manufacturing it."
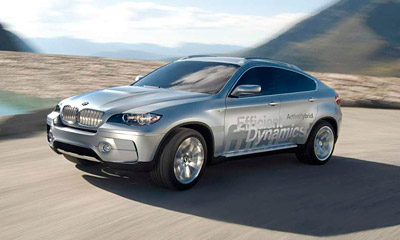
Photo courtesy of FEV.
Dodge Caliber ReEV Concept
The Dodge Caliber-based Range-extended Electric Vehicle (ReEV) with plug-in capability was unveiled at the 2009 SAE World Congress in Detroit. Rogers says that the vehicle "was developed as a concept that shows the potential to take a range-extended vehicle down the same production line as a pure battery-electric vehicle." FEV developed the system as a package that included a gasoline engine driving a generator to produce electric power that provides range extension. They created a unique method for putting the system into a vehicle to provide various options. For example, when the goal is a battery-only vehicle, the space that normally holds the engine and generator would be filled with batteries, as would the area that previously would have held the gas tank.
"That allowed us to get the extra capacity that we needed for a battery-electric vehicle while still going down the same production assembly line," says Rogers. "Everything downstream of the motor is the same, and that configuration was a unique installation. It was a technology demonstrator vehicle that has now led into other production programs."
The ReEV propulsion system developed by FEV allowed them to showcase their powertrain and vehicle development experience including:
- Performance modeling and simulations
- Component selection and procurement
- Design, analysis and packaging
- High Voltage system architecture, development and integration
- Hybrid controls and powertrain development and testing
- Complete vehicle integration
- Overall vehicle calibration, testing and validation
- NVH optimization
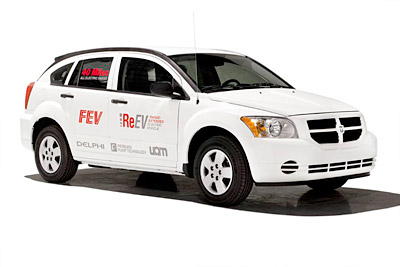
Photo courtesy of FEV.
A History of Innovation
The creation of new technology is not new to FEV. The diesel fuel injection systems in use today by manufacturers from Bosch to Siemens utilize piezo-electrically actuated injection systems introduced by FEV over a decade ago. "We first developed this technology in our research labs to be able to control fuel injection," says Rogers. "How you put the fuel in, where you spray it, how you spray it, the rate at which you spray it - that's all very important in the efficiency of the combustion as well as reducing emissions and noise." The use of piezo crystals was an enormous breakthrough in taking electrical control of mechanical systems and getting the maximum benefit, according to Rogers, and FEV was the first to do it.
Beyond Vehicles
Another area where FEV has played a critical role in electric vehicle progress is in infrastructure development. FEV teamed with Better Place, a company focusing on market-based transportation infrastructure that supports electric vehicles. The Better Place website says this about the project: "Better Place provides this solution via a network of battery switch stations that use an ingenious robotic system to switch new batteries for depleted ones, cool and charge the batteries in inventory, and manage the complex logistics to ensure that each EV gets a fully-charged battery each time the vehicle arrives at a station."
Rogers says Better Place needed vehicles to be able to demonstrate their approach, so FEV produced a fleet of battery-electric versions of a Renault vehicle to showcase their business case. Rogers says, "Their battery swapping concept is the equivalent of a service station, where you would go in and, instead of filling up your gas tank, you would drop out your battery and snap in another battery, and off you go."
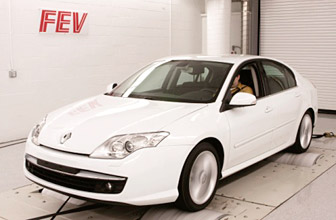
Photo courtesy of FEV.
Looking Ahead
Rogers says that creativity and innovation are only part of the future of the electric vehicle. "There's a lot of room for technology and innovation and some very creative ideas. But real acceptance of the electrification of vehicles is going to be tied to significant advancements in the production cost of these components. If we separate the operating cost from the purchase price I think the operating cost for an electric vehicle can be pretty low. I think the numbers today are more like 80 cents a gallon for an equivalent amount of energy in a battery-electric vehicle."
He's enthusiastic about FEV's continued role in automotive advancement. "What we do is go into our toolbox and pull out some tools that allow real innovation, a real step forward in technology. And there'll be lots and lots of opportunities to demonstrate brilliance as we go forward."