An Ancient Conversation with Copper
The longevity of an alloy such as silicon bronze is what Jeb S. Wood says is the true purpose behind what drives him to do what he does as the founder and owner of Independent Casting, Inc., a foundry located in Philadelphia, Pennsylvania.
“A lot of what we know about ancient society is from the bronzes,” Wood says. “I think fine art is certainly a symbol of society’s status and its ability to generate fine art in order to document that, as well as create something that has a semblance of permanence and bronze is a phenomenal way to go that attracts me -- that longer view of art attracts me very much.”
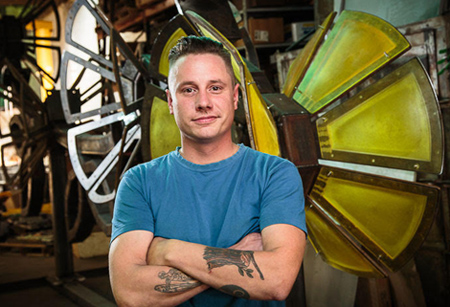
Photo courtesy of Independent Castings, Inc.
Everdur silicon bronze is the main alloy used at the foundry.
“It wouldn’t be our main allow if it wasn’t our favorite,” Wood says, adding they also cast statuary brass, white bronze, aluminum and silver.
Made of 99% copper, Wood finds silicon bronze to be a stable alloy in addition to other qualities that make it attractive to him.
“It is not as toxic as a lot of the others,” he says. “There isn’t the same levels of other metals in it -- we aren’t looking at high levels of zinc, lead or manganese -- it’s just copper and silica, so it’s a cleaner alloy that isn’t toxic, but welds beautifully, works beautifully, forges beautifully and pours beautifully.”
Wood discusses copper’s role in silicon bronze, which Independent Casting purchases at Lancaster Foundry Supply in Pennsylvania, along with all of the other alloys they use.
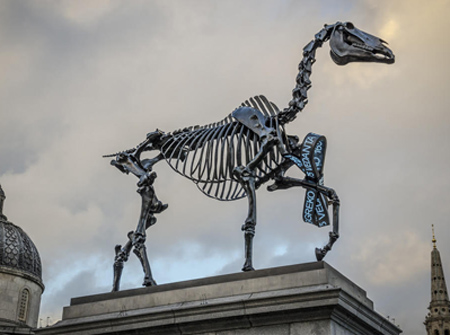
Drexel University.
Photo courtesy of Independent Castings, Inc.
“I think copper is phenomenal and we diversify it a little bit by adding some silicon,” he says. “What we are using in my mind is copper with an additive.”
Woods describes the attributes of copper that make it an appealing metal.
“I think it’s beautiful and amazing,” he says. “It’s very reactive and I think that humans have had a pretty great relationship with copper for a really long time and it’s not going anywhere. It’s an ancient conversation we have been having with that metal and it’s one we’re maintaining.”
The variety of patina the foundry creates using silicon bronze is another primary reason they use it.
“The variety of patina we are able to achieve with silicon bronze is the biggest reason to use bronze alloys in general, aside from longevity and their ability to take color,” he says.
They force a controlled patina on almost every work of art they complete at the foundry.
“Most of the time people don’t want the piece to have that bright green -- they want it controlled,” he says. “They want browns or blacks or blues or reds,” he says.
Wood’s background in fine arts led to his desire to open his foundry in 2008. While he does make his own work on occasion, his business is his primary focus.
“The foundry was very alluring to me and it felt like a challenge -- a very real and significant challenge and I liked the difficulty of it,” he says. “The lack of repetition is also attractive.”
There are varying levels of participation from his clients, which can have an impact on the final outcome.
“We have some clients who are very involved through the whole process and some who are very distant from the whole process,” he says.
A client who is intricately involved in the entire process may provide the foundry with a pattern in clay or plaster that they have made and the foundry is molding and putting it through their process.
“That person is going to want, generally, to check waxes or work on the waxes,” he says. “Often they will be here while the patina is applied and have control over that.”
In other cases, the foundry has a much more independent role from start to finish of the piece.
“We make a file or a simple sketch of what someone wants and the next time they see it, we are installing it in a gallery for a show or a municipality,” Wood says.
While it’s up to the artist to determine the level of involvement they would like to have in the process, Wood has seen how a back and forth working relationship benefits the work.
“We enjoy more involvement than less,” he says. “In most cases, the end result is stronger and more of a collaboration.”
Often times they work with a client in a collaborative fashion until they develop a language they can both speak.
“The standards have been established and we are on the same page regarding the interests and end desires of both the foundry and the artist,” he says.
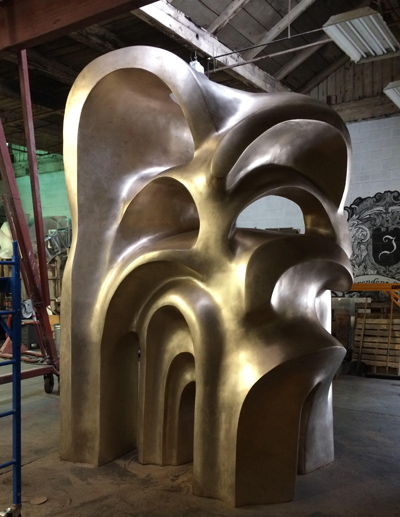
Work by Independent Casting includes Arches by Saloua Raouda Choucair.
Photo courtesy of Independent Castings, Inc.
Over time, a client gains the understanding that the foundry has their best interests in mind and that they are going to execute the work as they would want to see it executed.
“Often times, we’ll see them a lot in the beginning and then it will taper off over the years to the point where a real trust has been developed where we know the answers to the questions before we even ask them,” he says. “It’s a beautiful thing.”
The aim of the foundry-client relationship is to extend it beyond each finished work of art.
“It is really about the longer-term relationship,” Wood says. “Our interest is to develop that relationship and work with people over time. It stops a lot of reinvention and we can focus on the work itself.”
The 25 people working for Jeb at the foundry, located in the Port Richmond neighborhood of the city, help him make it possible to keep up with the demands of his work that is world-wide.
“It’s a lot of fun making work on a global stage,” he says. “Unfortunately we don’t do much with Philly and I wish we did more -- we work with Philadelphia artists but their work is generally being sold elsewhere.”
The majority of their work is coming out of L.A., San Francisco and New York.
“That is where it is all being derived from,” he says.
One of Wood’s most rewarding projects was a silicon bronze sculpture the foundry cast and fabricated in 2014 called Gift Horse by German-born artist Hans Haacke, which was commissioned for London’s Fourth Plinth in Trafalgar Square.
“His work is strong in statement and concept and that was just an enjoyable process from start to finish with the concept, the challenge of the timeline, the budget, who was involved, the variety of players and the amount of people that would see it,” Wood says.
Most of Independent Foundry’s work is seen by gallery goers, so the Gift Horse’s location in a highly public place was gratifying for Wood.
“In Trafalgar Square there is going to be a lot of eyes on the work and exposure to the work and that is going to be a fun opportunity for that level of visibility,” he says.
After being on view in London for a year and a half, the work began traveling around the world.
“It went to the Haus der Kunst in Munich and then it went to the Art Institute in Chicago and then it’s coming back to New York to the New Museum,” he says. “It is being installed there currently.”
Many people and much effort has gone into transporting the large sculpture. Wood was on hand to watch the first installation.
Independent Casting currently has a couple of monuments in the works that will also be heading overseas, but Wood can’t divulge any details due to intellectual property laws or out of respect for intellectual property.
“The concept of having to keep lids on things -- there is an interesting and complicated reality to all of that,” he says. “If what we make gets out there into the world ahead of time before it’s officially released, it could generate a conflict if someone else came out with something similar.”
Resources:
Also in this Issue:
- An Ancient Conversation with Copper
- David Tudor Sound Sculpture Comes to MOMA
- Rumors of War Sculpture Debuts in New York
- Exploring the Repoussé Work of Thomas Hammet
- Sculptor Kevin Jenkins and His Serendipitous Road to Copper