Functional Artwork for the Home in Copper
Even though it’s not his intention, every one of Jim Clapham’s copper pieces comes off looking like a work of art despite it being something as functional as a cupola or countertop.
“I have been making things my whole life and never considered it art, but I have been told I’m an artist all the time,” Clapham says.
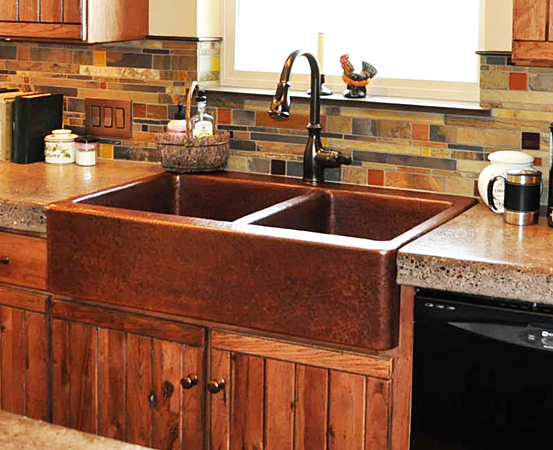
Photo courtesy of Mountain Copper Creations
From hand-hammered copper chimney caps and cupolas, to kitchen, bar, bath and laundry sinks, to counter tops and range hoods, Clapham puts function first when it comes to making his custom designs.
“That’s really what you’re after when you buy a range hood,” he says, of one example. “You want it to perform and then you put the design around that.”
He also makes hand-hammered copper frames.
“They are for mirror frames or art frames and are larger,” he says. “A 16-inch frame is the smallest.”
His first introduction to working in copper took place in a specialty shop where Jim worked in architectural sheet metal in the early 1990’s.
“We would have major copper jobs,” he says. “Roofing, finishing, cupolas and chimney caps.”
After 15 years, he branched out to start his own business, Mountain Copper Creations, with his wife, Pam, specializing in the fabrication of copper and zinc artistry.
“We just started out with one bathroom sink and just grew our business from there,” Pam says.
While Clapham also had experience in working with stainless steel, copper was the metal he chose to be the main focus of their business.
“Copper was just what I chose mostly because of its beauty,” he says. “I tend to stay away from stainless work now.”
He likes the rustic look of copper along other qualities that come into play when he’s making his handcrafted creations.
“Copper has a capability of being stretched and shaped into a shape that normal sheet metals don’t do,” he says.
Early on in the establishment of the business, located in Missoula, Montana, he set out to make six different styles of sinks to serve as samples of his work.
“I went to the local plumbers and designers and just got a feel for what they might like and if what I was doing was something they could use,” he says.
Within three months they had several copper sinks to place in a few showrooms in Missoula and they also attended trade shows. After launching their website they began selling across the country and today they deal directly with customers whether in or out of state.
“Now, we have sold to every state in the U.S. including Alaska and Hawaii,” Pam says.
Together, the Claphams each lend their own specialization to operating the business.
“Jim is the one who creates all of the pieces and I do all of the marketing,” Pam says.
He combines his knack for design along with his craftsmanship when creating his one-of-a-kind pieces.
“If he gets the blueprint for a kitchen or whatever room, he has an idea of how it should go in there and how it should look,” she says.
The quality of craftsmanship is what sets them apart from the standard factory-made varieties.
“For me, what I see out of a factory is really uniform,” he says, referring to the indentations made in the metal through the process of hand hammering. “It’s impossible to do this without overlapping. When it’s all in a row and it’s supposed to be hand-hammered, it’s not hand-hammered.”
Most of the copper they use is thicker than your standard shelf copper.
“I went through steps to figure out what copper works best for me for what I do, as far as the alloys and the mixture,” he says. “Not all copper is created equally — some welds better than others.”
He sought out Libertas Copper, located in Leetsdale, Pennsylvania, to have sheets of copper made to his specifications.
“I talked to an engineer at the mill and got some samples,” he says. “It’s a 51 oz. and the standard is 36 to 48 oz.”
Jim’s workshop, where he creates all of his pieces without any assistance, is situated on the property of their home in Missoula.
“I have hand breaks, a little shear,” he says, referring to some of his hand-held equipment. “Most of my shapes need to be sawed out because they are curves — they are roughed out and then hammered and then finished.”
He only uses heat to create the effects of aging on copper.
“From the beginning, we didn’t want to use any chemicals,” he says.
After hand-hammering the copper, Jim preserves the metal by applying a carnauba wax. He recommends that customers maintain their copper pieces by reapplying the wax occasionally.
“We recommend a range hood twice a year and sinks a little more often,” he says.
Jim doesn’t stock any items to sell.
“Everything is commissioned,” he says, of each piece that he signs with either an Mcc or Jim C. signature.
Their clients range from small homeowners to large homeowners and the working relationship for each project typically exists between the client, the builder and Jim.
“I prefer to know that person and see what they really want,” he says.
Jim is currently working four to five months out on projects and a good share of them are for clients who live out of state.
“The whole country is really busy with building, so I’m busy,” he says. “Right now I’m booked through September.”
Resources:
Mountain Copper Creations, Missoula, MO, (406) 880-9411
Also in this Issue:
- The Art of Crafting Copper Currency
- Functional Artwork for the Home in Copper
- The Precision and Magic of Copperpoint Drawing: A Visit with Artist Susan Schwalb
- La Femme Boheme: In Tune with Gems, Brass and Copper
- Rare Andrew Lord Bronzes on view at Gladstone64