Kingfisher Designs: A Cauldron of Creativity
After several years in the jewelry business, Don and Louise Coulson have started a new chapter making copper hollow ware, flatware and home accessories.
“The type of jewelry we were making didn't take much equipment and was portable. It was more of a hobby and we did not attend shows until about 2005. We started working with copper and were impressed by the workability, strength and, most particularly, the wonderful colors we could achieve.”
But metalwork proved to be a challenge, and the couple began to approach things from a new perspective.
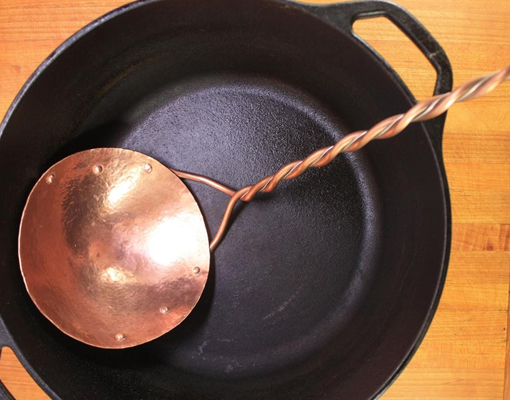
Photograph courtesy of Don and Louise Coulson.
“Simply learning techniques and using materials is not enough,” she says. “We wanted to stretch beyond bodily ornamentation into larger, more complex work. We began making small boxes, then larger hollow forms and mixed metal pieces using copper along with its wonderful alloys - brass, bronze and nickel silver.”
In 2012, they began creating hollow ware, flatware and serving pieces.
“Now, about 10% of what we make is jewelry,” she says. “For both of us, the cauldron of creativity, craftsmanship and choice of materials is fired with a passion for the work. Each piece is a journey and every trip into the studio is an adventure!”
Today, their home studio is on a river near a Mississippi town of 5,500 residents. It contains three different torches with different tips, numerous raising, planishing, forming hammers in various shapes, a recently-purchased rounding hammer, and a “new concept” saw.
The name Kingfisher was inspired by the view from their studio.
“We both love to watch the birds on the river where we live. From the back of our house, we were watching a kingfisher that resided there and realized that would be just the right name for our business.”
Louise does most of the cutting, hammering, repousse and coloring. She loves how copper “gives off a fabulous color with a little tweaking.”
She enjoys enameling beautiful trays, but cautions that torching and cutting the edges have to be done quickly because the two materials have different melting temperatures so the enamel melts faster than the copper and can run before the copper is cut.
“Don originated the idea of torch cutting enamels,” she says.
Don raises bowls from single sheets of copper. They may be placed outside to oxidize and turn green. Liver of Sulphur is used as a patina for the copper shot glasses.
“Don does the torch cutting and we do the enameling together,” she says. “He also makes all of the handles, ladles, slotted spoons and copper mugs with nickel silver inside and does the finish work on almost everything. I do the patina work and most of the computer work. Don does the database work.”
They use mostly 18-gauge copper, so it’s heavy and permanent enough for their work.
“Large copper rivets attach handles and side pieces,” she says. “We order online from a company in Dallas and sometimes Storm Copper. However, we really like to shop at salvage yards. One local company lets us look around, which is unusual. We discovered six huge pure copper boxes that had fallen off a truck and were badly bent/dented. Each had two lids. When I found out they were coffins, I would only let Don purchase one lid. We have used that lid in several projects and we purchased it at scrap prices,” says Louise.
Louise’s repousse skills can be seen on a clam shell hinged box cut out of pure copper and on many of the spoons and ladles. Hinges on the box are copper, as is the ring on the bottom for leveling. She also used historical knife blade ideas when rough carving the cheese cutters. Objects like copper pasta spoons, ladles, coffee scoops and flatware are designed to be used every day, built with strength to endure and become family heirlooms. Flame painting and form folding are among other processes employed.
Louise preps and cleans the glass goblets for the current Libations Collection. Six ounces of copper are fused to the glass as a liquid anode and cathode migrate the copper to the outside. This electroforming is time-consuming so usually several projects are being worked on at once. According to Louise, “Almost all pieces end up on each of our workbenches at some time or another.”
Kingfisher Designs recently won First Place in Mixed Media at the Gumtree Festival, a Mother’s Day tradition in Tupelo, MI, May 2017. Throughout the fall and winter of 2017, they will be attending Monte Sano Art Festival, Bluff Park Art Show, Pink Palace Crafts Festival, Covington and Chimneyville Crafts Festival.
Resources:
Also in this Issue:
- Carl Duzen: Copper's Transformative Effect
- Collage, Encaustics and Cold Wax: Sue Hohman’s Ways with Copper
- Kingfisher Designs: A Cauldron of Creativity
- Form Meets Function with Yucca Lane's Copper Coffee Pour Over
- Whistler and Contemporaries Featured in Reading Public Museum's Etching Revival Exhibition