Antique Restorations in Philadelphia Shine at Chelsea Plating Company
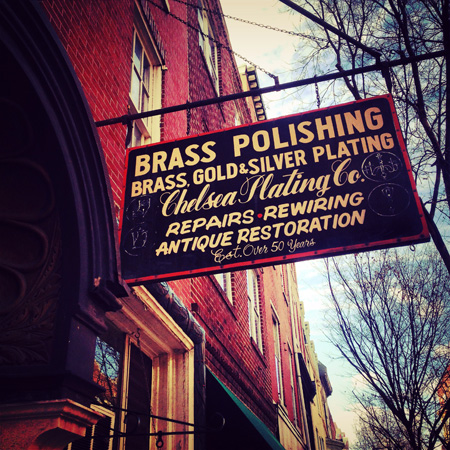
Photograph courtesy of Chelsea Plating Company.
Brass door hardware and copper pots and pans are just some of the pieces coming in for restoration on a regular basis at Chelsea Plating Company along Philadelphia’s Antique Row in Center City.
Founded in 1948, the business is currently operated by its third set of owners, Christopher Witter and Marc Regan, who took over last year but worked there as tradesmen since 2001 and 2000, respectively.
“Mostly plating was their specialty,” Witter says about early days of employees and the main marketed concentration. “They were more into lamps, tables and manufacturing back then.”
Today, Witter and Regan manage all projects themselves; these include predominantly restorations and also custom fabrication of lighting.
“We assist artists in producing whatever they envision, which they may not have the skills to do themselves,” Witter says about one aspect of the business. “Lately, we’ve been doing a lot of work for designers.”
About 75% of the work Witter and Regan do involves brass, copper or bronze, whether solid or plated.
Brass polishing is a large majority of what needs attention weekly.
Other jobs they take on include retinning and refinishing copper pots and pans, revitalizing bronze sculptures and cleaning up nautical components.
“A big part of our business is churches, so we do a lot of brass polishing for them,” Witter adds, noting that this often includes chalices, altar vases and crucifixes.
“Some people think high-polished brass is tacky, but other people love and appreciate it,” Witter says in illustrating the differences in color preference tastes with clients.
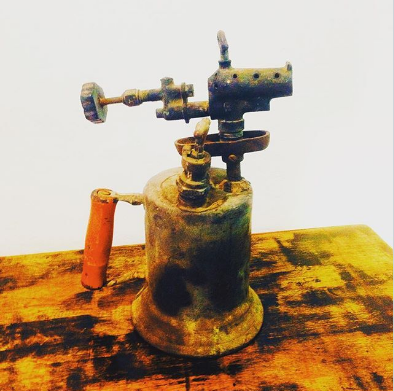
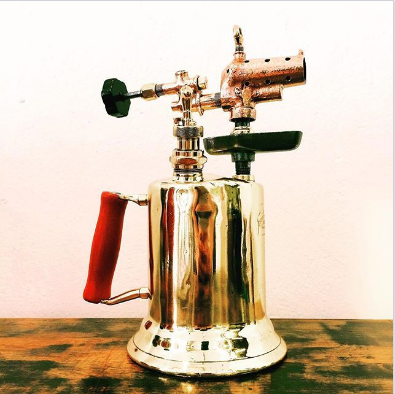
Photographs courtesy of Chelsea Plating Company.
Brass knobs, handles, levers, hinges, locks, deadbolts and knockers show up at Chelsea Plating Company frequently, especially when historic homes in the area are being redone.
“We use big, heavy polishing machines and have three of them,” Witter says about some of the workshop’s primary equipment.
"And we see varying stages of deterioration, so we practice basic restoration principles, but really, every job is different," Witter notes.
He and Regan implement various polishing compounds and techniques with restorations, based on needs with a particular project.
The oldest brass, copper and bronze pieces they see are from the 1800s, Witter confirms.
The company’s clientele is split geographically, with half of their customers located across the country, and half residing in the Philadelphia area.
“It’s a real mix of individuals, antique dealers, jewelers, museums, colleges and churches,” Witter says about the backgrounds of his clients
One notable assignment which Witter and Regan completed in 2015 consisted of restoring selected works, some in brass and copper, from a private collection formerly owned by Dr. Thomas W. Evans.
The exhibit took place at the Arthur Ross Gallery at the University of Pennsylvania.
Evans served as one of the initial benefactors of the dental school at the university in the late 19th century and gathered unique artifacts in his travels abroad.
Anywhere from 5 to 10 new projects come in daily, and while the old turnaround time for finished work used to be 4 to 6 weeks, it’s now about 8 to 12 weeks because client requests are so continual.
“We don’t try to be the fastest or the cheapest—we want to be the best,” Witter says about holding the company’s historic work to a high standard.
Resources:
Also in this Issue:
- Northeast Lantern: Shedding New Light on the Classic Copper Lantern
- Where Form Meets Function: The LTS Solid Copper Pen
- Antique Restorations in Philadelphia Shine at Chelsea Plating Company
- The Copper Tub, Reinvented for Today’s Modern Bath
- Rare Enamel-on-Copper Works on View at Crocker Art Museum