The Continuing Legacy of Vendome Copper & Brass
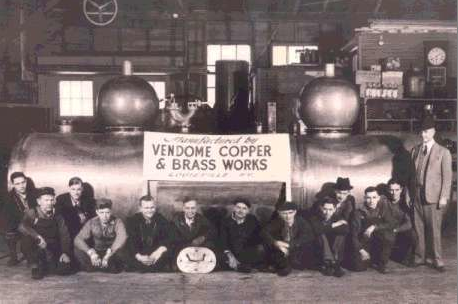
The great bourbons, whiskies and moonshines of the world all have one thing in common: they were created in copper stills. Vendome Copper & Brass is one of only a few U.S. copper fabricators who make copper stills for the distillation industry.

The company was founded in the early 1900s by a young W.Elmore Sherman, Sr., then in his early 20's, who took over the Cincinnati-based Hoffman Ahlers coppersmith firm where he worked as a bookeeper. He renamed it Vendome Copper and Brass Works and with each successive generation of Shermans - from son Elmore Jr. to the current management under grandsons, Vendome has prospered. Today they are one of the largest custom manufacturers of process equipment for the chemical, distilling, brewing, confectionery, food, dairy and pharmaceutical industries.But, the Vendome legacy began with their handcrafted copper stills.
“If any state has a still in them, it’s probably [made by] us,” says fourth generation owner Mike Sherman. Vendome, located in Louisville, Kentucky, is a custom fabricator of a variety of stills including crafting copper stills for many in the bourgeoning craft distilling movement, as well as major players like Jim Beam, Wild Turkey, Buffalo Trace, and Jack Daniels. “We’re keeping real busy,” he says with a slight weariness. But that’s a good thing. In addition to making new copper stills, Vendome also replaces copper and bronze parts on older stills. Since the beginning, copper has been a critical component artisans use when making stills.
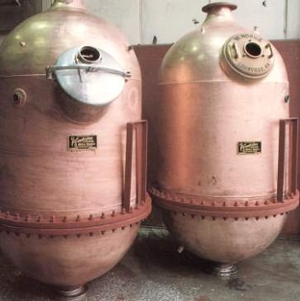
“Copper has a chemical reaction between the fermented mash and the copper,” Sherman says. “It pulls out sulfur and sulfites which you don’t want in the distillate.” Even if a distiller uses stainless steel Sherman suggests, more than likely there will be some copper element, either copper mesh or cut up copper in the top of the column rectifier that captures the vapors. “It’s about copper contact.”
The majority of Vendome’s copper sheet comes from overseas ranging from 1/8th inch to 3/16ths and occasionally into heavier, ¼ inch, and even 3/8th on some pot stills. “Domestically you can’t get anything wider than 36-inch sheet so we have to source some copper sheet from Europe,” Sherman says. Though they have a mill in Europe there is still a 20 to 26 week wait time. Out of necessity, Vendome has a strong copper inventory in their Louisville facility.
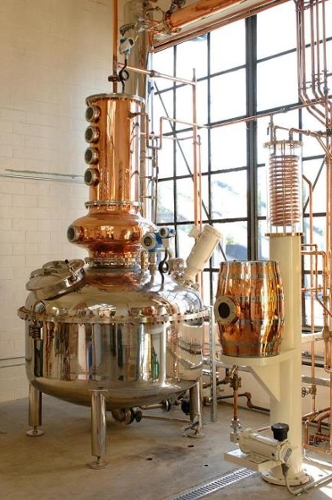
To form the still they circle sheer the copper sheet and anneal it to where it is “folded over like a taco” Sherman says. They perform the majority of machine work in-house, using TIG welding which is 99.99% copper filler metal, Smith says. “We have guys who can weld stainless but can’t even begin to weld copper.” Therefore Sherman has a dozen people who are certified copper welders knowing the nuanced technique it takes to make seams perfect. “Because they are welding at such high amperage for copper if they hesitate one second they blow through the metal. Coppersmithing is a lost art,” he admits.
Once the still is completed Vendome offers three different finishes including an acid clean to get the copper uniform, and a satin finish using a small hand polisher to even out the copper color. Lastly there is the highly polished mirror finish which is labor intensive, and mainly used for stills which are part of a high-end public tours. “It’s absolutely beautiful, but we’ve also found that people love the copper when it’s not always shiny. The patina look is very pretty.”
Vendome’s copper stills can be found in Canada, the Caribbean, Guatemala, Romania, and even Ireland. “Everyone’s intrigued with copper, it catches people’s eyes,” Sherman says. And Vendome Copper & Brass has captured the market. If you’re in the Louisville area you can tour the facility, but contact them for details.
Resources:
Also in this Issue:
- The Continuing Legacy of Vendome Copper & Brass
- The J. Paul Getty Museum Acquires Rare Self-Portrait by Rembrandt
- The Appeal of Apothic Art
- Fauna and Flora Beckon at Elm Grove Forge