Bird Feeders Redefined as High Art
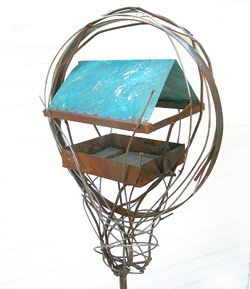
Photograph courtesy of Joe Papendick
At first glance Joseph Papendick’s outdoor sculptures appear to be your typical fare of abstract garden art, until you take a closer look and realize it has a true function as a bird feeder.
Seven years ago when Papendick, who studied at Parson’s School of Design, was working in the restaurant field to support his interest in continuing to make art, he was posed a challenge that would shift his focus from works on canvas to works made of metal.
“My fiance’s mom had a bird feeder. It was a platform feeder and some raccoons had gotten into it and bent it,” Papendick says. “She asked me if I could fix it. She didn’t mind the raccoons using it, so I made her something that would stand up to that.”
He also took a keen interest in the idea of feeding birds after moving from New York to St. Louis, Missouri to work in a 5,000 square foot loft space.
“There are no birds to feed in New York City,” he says, adding he would spot the occasional pigeon.
Papendick recently moved to Fairview Heights, Illinois where he converted his garage into a studio.
From his earlier exposure to abstract steel works he was convinced that if he were to ever dedicate himself to that route, function would have to be the primary motivation.
“It just seemed I would never do that unless I had a reason,” he says.
Soon after selling the two restaurants he owned to focus on making large, standing, and small scale, hanging, one-of-a kind bird feeders, Papendick’s work was featured on HGTV (Home & Garden Television).
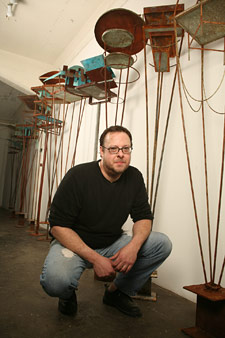
Photograph courtesy of Joe Papendick
He uses copper when making the roof-like structure for his sculptures. The rest of the feeder is typically made using steel and in some cases, he uses brass or bronze rods. He gets most of his materials at Shapiro Metal Supply in St. Louis.
“I never use copper in a structural way -- it’s always a decorative element,” he explains, due to its thin nature. The roof-like structures aren’t necessarily protecting the bird food which his why he considers them to be decorative.
A perforated, removable, steel tray holds the food.
“If it rains, the water drips out and the food dries the next day,” Papendick says.
Due to the high expense of copper, he uses it sparingly. Papendick discusses his approach to welding it.
“When I’m welding copper, I kind of force it slowly,” he says, by way of a MIG welder. “It’s almost like a hot metal glue gun except metal comes out.”
The next step after welding the rest of his piece with a small Miller welder is to finish things off with a hand held angle grinder.
Afterward, a chemical process takes place.
“I use a patina that gets sprayed on there,” Papendick says, referring to his large- scale feeders. “It forces that chemical reaction that would normally take about twenty years to occur.”
He applies the spray to the entire feeder causing each metal to react differently.
“That adds different layers of depth to the whole piece,” he says. “It’s almost like seeing a rainbow of colors – they are natural.”
Lastly, the feeder is sprayed with a clear polyurethane coating to protect it from the elements.
Typically drawn to take a minimalist approach to his work, Papendick enjoys the freedom he has in making his structures.
“These pieces kind of look like architecture,” he says. “But people don’t have to live in them. They don’t need air conditioning or plumbing, so I can do whatever I want.”
Also in this Issue:
- Kenneth Lynch & Sons: A Legacy of Beautiful And Functional Outdoor Ornaments
- The Quaint and Awe-Stirring Lure of Cottage Gate Creations
- Bird Feeders Redefined as High Art
- Ruth Asawa Exhibition at Christie’s
- Roy Datz: Designer of Unique Handmade Copper Doors And More