Greg Wilbur: Using An Ancient Process to Create Contemporary Artworks
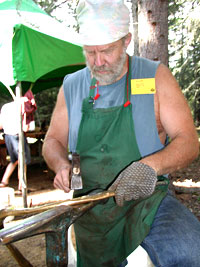
Photograph courtesy of Sierra Nevada College
In Korea, China and Japan, the labor-intensive craft of metal raising developed over thousands of years and is so difficult that few Western craftsmen attempt to master it. Yet, Portland-based studio metalsmith Greg Wilbur forms modern art pieces and enthusiastically teaches the technique in workshops/classes around the United States, Canada and New Zealand.
"I buy large sheets, usually 4' x 8' heavy 16- to 20-gauge copper or 3' x 9' commercial bronze, mostly new," he says. "Local dealers often contact me. I cut the sheets to different sizes depending on what I've decided to make. Sometimes I give jewelers and hobbyists the scrap, but I have about 50 pounds accumulated over 30 years that I need to recycle."
Wilbur has a BFA in jewelry/metalsmithing and a BS in art education from the University of Oregon in addition to a BS in general studies from Western Oregon University.
Last summer, he taught "Moving Metal: The Art of Raising," at Sierra Nevada College. He brings his own tools and materials to the classes he conducts, including cross-peen, steel-forged raising hammers and stakes that he both makes and buys. The projects produced require hand strength and are time consuming but he works closely with students one on one to guarantee everyone finishes a piece.
Wilbur emphasizes to students the simple but stark differences between both Western and Eastern concentric raising.
"In the Western technique, you are pushing away from yourself whereas, with the Eastern style, you are working towards yourself," he comments. "I squish, hammer and make form from one sheet of metal. I don't do any welding or soldering. I hold the copper on a stake and hammer just behind that little area where it comes in contact with the stake, move the piece a bit and knock it down, working in concentric circles from the sheet's center to the outer edge. Depending on the design, I do between two and 200 courses of this raising. One piece of metal could take half a million blows to reach its potential. The whole process of using just one piece of metal is sort of a Zen concept to me, something I've stuck with for over 30 years."
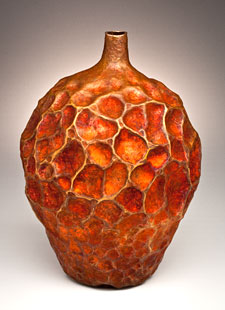
Photograph courtesy of Greg Wilbur
Wilbur's rule of thumb is to not hit the same place more than once.
"Once the metal is struck it becomes brittle," he says. "I stop hammering and anneal the piece by heating with a propane torch to a temperature around 1,000 degrees, then quenching by plunging into water or air cooling to make it more malleable."
His signature look has been developed over years of practice.
"To finish, I often hammer with a slightly convex-faced planishing hammer, in conjunction with a planishing stake, which expands the metal a little, gives it a facet look and can take out surface irregularities," he says. "I use heat patinas on some pieces and certain acids such as copper nitrate, silver nitrate and liver of sulfur on others. Wonderful bright reds on copper are only derived by heating very hot and plunging into boiling water, an oxidation reduction process."
Wilbur has exhibited at American Council Craft Shows in San Francisco and Baltimore, Smithsonian Craft Show, Philadelphia Museum Crafts Show and the annual Oregon County Fair. He participated in a three-person show at the Museum of Contemporary Crafts in Portland. His work can be seen at Velvet da Vinci in San Francisco and Waterstone Gallery in Portland. He co-founded the highly rated Art in the Pearl Festival and has appeared on the Oregon Art Beat.
Resources:
Also in this Issue:
- Jimenez Sculpture: The Beauty Is in The Copper Detail
- Copper in the Air
- Greg Wilbur: Using An Ancient Process to Create Contemporary Artworks
- The Combustible Side of Copper Art
- Large Salvador Dali art collection on display in Austin