Speaking the Language of Metal
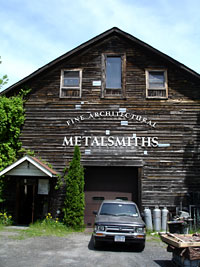
Photograph by Paul David
Although he was an Anthropology major, and she studied English, Ed and Rhoda Mack's future was forged in metal.
"It's very logical what we're here doing, right?" she quips. "Working with metals has so many different directions and interesting things to wrap your mind around."
The pair founded Fine Architectural Metalsmiths during the metalsmithing renaissance in the 80's in a small barn in upstate New York. What began as simple ironwork projects for the home transcended into more elaborate works that delved into the fine art realm. They began studying and reviving methods of metalworking that had simply been forgotten and started creating more elaborate pieces.
With roots in iron welding, the Mack's began working with copper for its versatility.
They've even developed a technique where they cover wrought iron with a bronze powder in a suspension, so the piece is totally encased with bronze.
"You can do alot of the same things you do with iron, but copper is more responsive," says Rhoda. "It has decorative abilities that are different from iron."
Business quickly grew, and the Macks found themselves in need of a larger space. In 1993, they found the perfect location--an 1800's Borden's Creamery Icehouse in Florida, NY. Untouched for decades and overrun with thickets, the Macks spent 6 months renovating the building and today this historic showroom is a beautiful complement to their work, with exposed beams, 19th Century fixtures and original woodwork throughout.
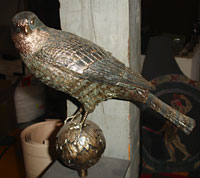
Photograph by Paul David
Fine Architectural Metalsmiths quickly gained a reputation for their impeccable attention to detail, and greater understanding of the nature of metal and soon were asked to work on public installations. Notable works include the elaborate bronze gates of Lewiston, Maine, a commission at the Federal Reserve Bank in New York, and the notorious Gates at the Dakota Courtyard, where John Lennon was shot.
Browsing around the shop, visitors can view a comprehensive selection of the shop's eclectic projects over the past 26 years, paying homage to the Mack's mastery of metalsmithing techniques and styles. The showroom personifies Fine Architectural Metal's range of metalsmithing, featuring everything from a patinated copper and glass table to hand forged, classical bronzed sconces.
"What's possible?," Rhoda says, looking around the studio. "Anything."
They continually experiment with metal crafts, experimenting with new forging and techniques in this creative, freeform environment.
The Center for Metal Arts
In 1993, Fine Architectural Metalsmiths began the Center for Metal Arts, an instructional space dedicated to passing on the techniques and process of accomplished metalsmiths. The Macks and several guest artists hold classes and seminars throughout the year to encourage the exchange of new ideas in metal. Attendees usually include new artists and adventurous 9 to 5ers who want to have a creative vacation, learning a new trade.
"It's amazing to go from sitting at a computer all week to spending a weekend here," says Rhoda. "It's so primal, working with metal---it's really good for you to work with your hands. We get so divorced from our bodies."
They also hold 1-week intensive blacksmithing classes, attracted people from all over the world.
"It's like a blacksmith boot camp," says Rhoda. "I feel like I'm throwing a block party. By the week's end, everyone knows each other."
They recently had the legendary Charles Lewton-Brain for a three-day
session on unconventional repousse and chase work.
Upcoming one-day classes include Copper Fold Forming on November 14, taught by Ed Mack, Blacksmithing for the Design Professional on September 26, with sculptor and classically trained metal artisan Fred Crist, and on October 10, led by art furniture designer Vivian Beer.
"We have four artists who work here," says Rhoda. "Everybody brings their own skills and take on things so there's a great synergy."
Fine Architectural Metals specializes in custom projects, and the Mack, always up for a challenge, love when a customer opens the door in a new way, pushing the boundaries of metalsmithing.
"Customers come with ideas and then the dialogue starts-we discuss architecture, history, style and the type of house the work will live in," says Rhoda. "Ed is good at coming up with solutions."
When buying materials for a project, the Macks prefer local, US-based foundries and shops.
"We purchase our copper materials through local nonferrous suppliers who have been in business for a long time," adds Rhoda. "Depending on the project, we will use one of several small foundries, one in Tulsa, one in Virginia."
In addition to creating custom projects for clients, the artists of Fine Architectural metals are always studying their craft and working on new metalsmithing techniques.
"Our future has to be in experimenting and trying new things," says Ed. You have to stay in synch."
Ed began practicing a unique fold-forming process of copper, and is currently one of the only artists working in this style today. Developed by Charles Lewton-Brain, a metalsmith from Canada, fold forming is a completely new way of forming sheet metal quickly into three dimensional shapes and textures from single sheets of copper. The effect produces a structurally sound piece that that looks like it was soldered, but it requires no heat or tools to shape it. Ed has met with Lewton-Brain, and currently teaches classes on this little-known process to introduce the method to a new generation of artists.
"It's a combination of origami and forging, because we heat the metal, and, the way you fold it determines the shape you are going to get," says Ed. "The way it folds in this process is very organic," says Ed. "It resembles elements in nature."
To form fold the metal, Ed first heats the copper to an annealing temperature between 900-1400 degrees F, before placing it in water so it becomes cool enough to work with. Then, he begins pressing the copper, in the direction he wants, making creases by folding the piece, so it resembles a soldered piece. You can fold other materials, but Ed prefers to work in copper.
"The secret is understanding the elasticity and strength of the copper," says Ed. "The colors we get are absolutely beautiful."
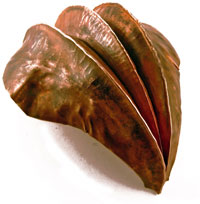
Photographs courtesy of Fine Architectural Metalsmiths
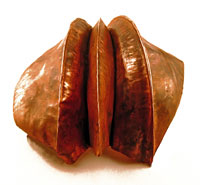
Resources:
Also in this Issue:
- Speaking the Language of Metal
- Ward Elicker Casting: New Horizons Provide a Clearer Vision
- The Art and Legacy of Washington Copper Works
- 20th Century Decorative Arts Auction at Bonham's and Butterfields Features Notable Bronze and Copper Works