The Art and Legacy of Washington Copper Works
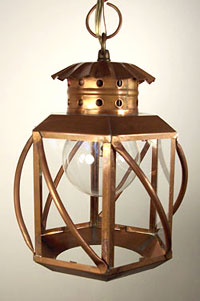
Photo courtesy of Washington Copper Works
Serge (Larry) Miller is the quintessential Renaissance man. A Yale graduate who taught French and geometry, he was a bread maker, a calligrapher, and a house builder before discovering the craft of copper lighting fixtures. "He really was just looking for something he enjoyed," says Serge's son, Chip Miller, who now runs Washington Copper Works in Washington, Connecticut, the business that Serge founded more than 25 years ago. Today, Serge is "mostly" retired but is often consulted when custom work is requested. "There are still things that he can do that other people can't do," Chip says.
Chip is also a history teacher, but he began to learn his father's trade at the age of 12 and worked full-time for the business during summers by the age of 14. Washington Copper Works is still run in Serge's house and currently has two craftspeople making the lights - Janet Buonaiuto and Gary Miller (no relation to the family.)
Of course, starting a copper light business wasn't easy in the beginning, so Serge began taking his work to juried craft fairs. "I have really fond memories of this," says Chip. "You would have to send five works - not photographs, but actual works - and a group of people would judge. A pretty small percentage of people who applied to the juried fairs got in." If a particular design sold well at a fair, Serge called Chip's brother at the workshop to ask him to quickly produce more of that style.
From that, the business began to grow, and they now have several designers and builders as regular customers. Each piece is handmade and custom shaped from flat copper sheets. The company's lights are displayed in every state of the U.S. and several other countries, including Disneyland in France. One customer in Oklahoma hangs 40-60 of the company's lights from trees.
The business has stayed small because that's what Serge preferred. "There aren't that many people who are doing a job that is most of the time pleasant and relaxing," Chip says. "So, that's worth a lot, and I understand why he didn't really care about growing."
As a result, no two lights are the same, even if they're essentially the same design, and every light is signed and dated by the crafts-person who made it. "The two people who are working there are really artists," says Chip. "They want to make one at a time." Cutting some pieces of the copper takes a long time by hand, and if they aren't cut correctly, they won't solder together properly. A metal press could do it in 30 seconds, but this family business has no desire to become a factory.
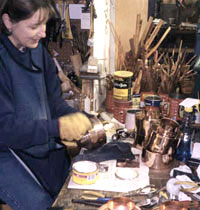
Photo courtesy of Washington Copper Works
"We work with a certain gauge copper [24-gauge]. Some of our bending breaks are antique," Chip says. "Pretty much everything we use, except for the electric lights that we use to see with, are the way you could have made the lights a few hundred years ago. We roll parts around old wine bottles. It's very, very old and very trial and error. Aside from copper refrigeration tubing, which we use for some spiral parts, and some solid copper wire that we use for the hinges of our lights, everything else is just flat 4x8-foot sheets of copper that get cut and folded and punched and notched, etc. and made into those parts all pretty much in the basement and the upstairs of that house."
You might think that such work would be too noisy to perform in a home, but Chip insists that it isn't as loud as you'd expect. Most of the hammering is delicate and done with a small jeweler's hammer. Some designs require no hammering at all except for the hinges.
"We have this thing that we roll over them to make them perfectly flat," says Chip. "Then, we put them in needle-nose pliers, bend them into kind of a double bend, then put them in a vice grip, and hammer half of it over."
The atmosphere in the workshop while Chip was growing up was politically charged with artists like his father who played classical music and spoke daily about philosophy and literature. "For me as a child, this was just wonderful," he says. One of the lessons he learned from his father is that theory isn't enough. You need to be able to do things with what you know, like Thomas Jefferson's contention that everyone should learn to do something with their hands. "It's not just making old-fashioned lights. It's kind of colonial America. And that's disappearing," Chip says. "So, more than just making the lights, I feel incredibly lucky."
Resources:
Also in this Issue:
- Speaking the Language of Metal
- Ward Elicker Casting: New Horizons Provide a Clearer Vision
- The Art and Legacy of Washington Copper Works
- 20th Century Decorative Arts Auction at Bonham's and Butterfields Features Notable Bronze and Copper Works