The Art of Copper Cupolas
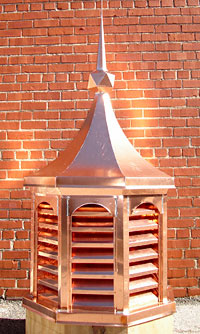
Photo courtesy of John Tyler Architectural Roofing and Sheet Metal
Copper cupolas have prolifically chronicled thousands of years in an array of artistic forms and functions – from their storied Roman era roofs to their presence today, thanks to the continued fascination from today’s architects, homeowners, and historians.
Whether old or new, copper’s choice as a cupola material stands as a testament to this versatile medium, these stately structures continue to stand as an expression of power or unity atop state capitol building domes, residential estates and historic structures.
The First Cupolas
Dome-like roof cupolas (meaning “small cup” in Italian) in general are believed to date back to the Greco-Roman era (146 B.C. to 476 A.D.) as a descendant of the watchtower. Travel and trade by water became more popular, as did enemy attacks at that time. Those men posted as security high above at this view could now do so out of their homes, thanks to the more residential cupola.
Cupolas immigrated to the northeastern United States along with history’s European pioneers in the 17th and 18th centuries, with their popularity peaking after the Revolutionary War. The first prominent copper cupola, along with its accompanying famous grasshopper weather vane, traces back to 1806 at Faneuil Hall in Boston.
“Copper never wears out,” says Bob Adams, owner of Classic Residential Copper of Tulsa, Oklahoma of the cupola’s longevity. “It has a life of about 300 years.”
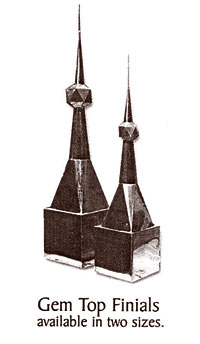
Photo courtesy of John Tyler Architectural Roofing and Sheet Metal
More common versions of the roof cupola, perched atop homes in coastal fishing ports, were known as a “Widow’s Walk” – large lookouts where families and wives could await the return of ships carrying their loved ones.
The patina-weathered copper cupola, dating back to 1832, atop the Adams County Historical Society (ACHS) museum near Gettysburg, Pa., served as a significant view during the Civil War. According to ACHS director Wayne Motts, the building was used as the main administration facility for the Lutheran Theological Seminary at Gettysburg from 1832 to 1895. Its cupola, though decorative, also acted as a signal station for the Union Army during the Battle of Gettysburg on July 1, 1863.
“With our location on top of a ridge, it’s the highest building in town,” says Motts. He adds that some of the filming of the 1993 movie “Gettysburg” was done from the cupola.
Cupolas soon evolved into a more decorative architectural accent or reflection of individuality, rather than a necessity, gracing Victorian-style homes, carriage houses, as well as gazebos and barns.
Diagram and Diversity of a Cupola
Though eye-catching, ventilated, louvered rooftop cupolas also remain grounded in an important role: to allow hot air to escape from a garage or home’s attic, which prevents wood’s premature rotting, the forming of mildew, and paint peeling. Sizes and shapes vary – from octagonal to hexagonal, circular and simple square designs. Cupola’s cousins are the lantern, which live above a tower or turret, belvedere or gazebo – structures large enough for a lookout – and belfry, where bells are hung.
John Tyler, owner of Architectural Roofing & Sheet Metal in Tulsa, OK, began constructing copper cupolas in a slew of sizes in 1965.
“I retired from the union at 39 as a sheet metal worker,” he says. He remembers being initially inspired after seeing an historical house with a copper seam roof in Harrisburg, Pa. “It was just so beautiful and that got me excited.”
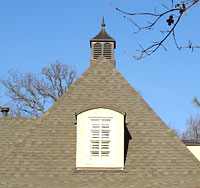
Photo courtesy of John Tyler Architectural Roofing and Sheet Metal
“The first cupola I built was an octagon,” he continues. “But at first I was angry because I couldn’t figure out how to build it; I remember slamming my fist down on the workbench. After the third day staying cooped up in the garage, my wife came in to see if I wanted to come in the house for Thanksgiving dinner. All of a sudden, it was like my spirit, spoke, ‘I can’t figure it out.’ Then I finally saw the pattern in my head. I couldn’t see it before I said that – even if it was right in front of me. I was shown how to do this.”
Since that spiritual intervention, Tyler and company started building square cupolas and selling them “like hotcakes.” “We don’t make the weather vanes for the top because of the birds and their deposits over the years,” he laughs. “It then looks white instead of that copper color.”
Tyler’s cupolas are hand-built on an average of four hours per cupola, three cupolas per week and 50 per year – now a little slower because of the recession. “I’m very protective about what comes in and out of here,” he says. “Some of the tools we use go back to 1863. We cut the copper by hand, starting with raw, flat metal – about a 3-foot to 10-foot piece – and then cut the pattern.” Resulting sizes range from an 18-by-18-inch to 30-by-35-inch; resulting prices range from $1,800 to $2,700. His biggest advice for a clean, quality cupola: “Once you’re done soldering, your fingerprints must be washed off.”
Jim Bryant of Vintage Copper says Tyler is his friend and mentor – and the reason for his copper career. “I met John and his daughter at a beekeeping class several years ago,” he relates. “We struck up a friendship, and through this friendship, he taught me about crafting copper. I was at a stage in my life where I needed to take another route. Copper crafting fulfilled that need and I have not looked back.”
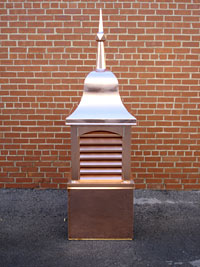
Photo courtesy of John Tyler Architectural Roofing and Sheet Metal
Like his mentor, Bryant keeps to traditional coppersmith methods. “My goal in using the name Vintage Copper for my company was to illustrate that, while we work in copper, we are not a modern assembly line process,” he assures. “Our products are individually hand-fabricated by craftsmen with many years of experience – just like the old timers did. And some of the equipment we use is over 100 years old. The antique equipment is what we use to make most of our products.”
Bryant has also found success in the square cupola, replicas of those in the 18th and 19th century, as well as an octagon shape and French curve variant. Standard sizes range from an 18-inch gazebo to 47 inches wide ($3,425 to $12,050). “The largest percentage of our products go to the coastal regions – More so the East Coast and secondarily, the Gulf Coast,” he says.
Vintage Copper’s cupola handiwork can be seen atop courthouses and other public buildings, universities such as Stanford, schools, business and residential projects.
“Many architects see our products and spec them on the house plans, some home buyers call us and have the builders buy the product,” explains Bryant. “But generally, it is the builder that closes the deal and may be acting on the instructions of his customer or architect. Personally, I like architects. They are looking for the perfect product to fit the house, whether it is one of our standard products or a custom one. Builders tend to worry less about quality and more about the bottom line.”
Bryant is also quite the copper proponent for homeowners interested in it, saying, “New copper is near the color of gold, aging gracefully to bronze and on to the blue-green patina that you see on statues in a park,” he says. “Copper does not rust and will last longer than most of the people that buy it. I believe that people recognize and appreciate the long-lasting value and beauty. Normally, copper used in a house is there for the life of the house.”
Adams also can’t say enough about the lasting beauty of copper and the coppersmith industry. “But I never thought I’d be doing this!” he says. Originally a degreed accountant in business administration, Adams worked for a company that built service stations, which led to his interest in sheet metal and background in sheet metal fabrication. He founded Classic Residential Copper 13 years ago. “I’ve always admired copper work, and said, ‘I think I can do that!’” he says. “I’ve always been more creative than corporate anyway. I used to oversee 65 and now there are just three of us.”
Adams says he has 70 different copper cupola patterns – mostly for large, $5 million residences – and stands firm on coppersmith tradition, just as his fellow coppersmiths. “We have only one powered machine to cut the sheets, but every part has to be hand cut,” he says. “We hand cut many parts. There’s no way you can just get a guy off the street to do this. It requires a lot of facets of work and a lot of time.”
Also in this Issue:
- The Art of Copper Cupolas
- Mystical Creations Jewelry Artist Tara Helwig
- Dennis Cordeiro's Unique Copper Fish
- The Arts and Crafts Society of Central New York
- SFMOMA Unveils New Rooftop Sculpture Garden