Schtiller & Plevy: A Commitment to Restoring History
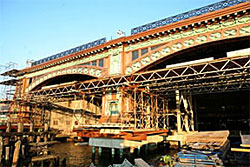
Photograph courtesy of Schtiller & Plevy
It all started in 1920 when Isador Plevy, whose grandfather had installed the "skins" of onion dome churches in Czarist Russia, founded a sheet metal fabrication shop in Newark, New Jersey. Over the years, the Plevy family evolved the company until it became an elite business that restores historic buildings to their former splendor and makes them more structurally resilient in the process.
Today, Isador's grandson, Larry Plevy, serves as President of Schtiller & Plevy, Inc., one of only a few fully accredited Historic Restoration Contractors that exist in the U.S. This has led to work on such buildings as Carnegie Hall, the American Museum of Natural History, and the Plaza Hotel in New York City, the Jersey City City Hall, and Thomas Alva Edison's New Jersey residence.
Plevy is quick to say that the company uses copper in an industrial rather than an artistic manner, but the creativity required in his business is not to be downplayed. Ornamental and architectural sheet metal is only a portion of the company's work. Its exterior façade restorations also include masonry, roofing, decorative woodwork, windows, doors, structural stabilization, and historic painting.
Perhaps one of the most creative aspects of the work, however, is problem-solving.
"I prefer to go into the realm of looking at how the old-timers put the metal work together, why it failed, and how I can improve upon it so that in 100 years, they won't be restoring the same metal work that I just restored now," Plevy says. "A lot of the things that they did wrong were that they connected pieces from one place - vertical or horizontal - to another without anticipating expansion."
These builders in the past also didn't anticipate that the reaction between the substrate support and the perspiration of the copper would cause disintegration of the less noble metal, such as the steel armature or fastener. Schtiller & Plevy commonly replaces fasteners with stainless steel versions and separates dissimilar materials with material that will last another 100 years or more.
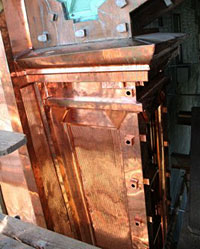
Photograph courtesy of Schtiller & Plevy
Naturally, funding agencies for historic restorations prefer to use as much of the historic fabric as possible, but this can be more expensive than using a newer fabric. This is because the fabric must be removed from the building in a gentle way, cataloged, stored properly to preserve it, patched, and then, reinstalled. The existing conditions of the fabric may have to be documented, and full size mock-ups might have to be made, so there are more steps involved. When some of the original pieces are missing, duplicating old ones can also be a complicated and expensive proposition. A mold might have to be made, for example, of the original piece in order to duplicate it. While the company works hard to use the historic fabric whenever possible, Plevy only recommends it when he can guarantee that it will last for another 100 years or longer.
"Sometimes, we take these facades," says Plevy, "and we actually prefer to re-use the vertical face of an item rather than the horizontal face where the water would be wearing it out, then replace the horizontal items with new copper, and tie it into the vertical old pieces."
Placing new copper behind old pieces, for example, can sometimes keep water out of the building envelope.
"I think my first historic restoration job was a church down in Trenton," Plevy says, "and the Father came to us and said, 'I have this beautiful copper structure. It's about 30-feet long, and it's leaking and causing problems. What can we do to stop the leaks?"
The church didn't have the money to duplicate all of the historic fabric. Therefore, the company cut the original copper structure into pieces, restored it so that it wouldn't blow away, and put a waterproof membrane of copper underneath it with a support system in order to make it last for another 100 years.
The Carnegie Hall project involved restoring copper and galvanized cornices, and they had to anticipate how long it would take the workmen to do the work on a hanging scaffold. There were a number of steps involved, including cleaning the inside of the cornices, and the scaffold had to be moved every time the workmen were ready for the next section.
Plevy grew up watching his father and grandfather work in the business.
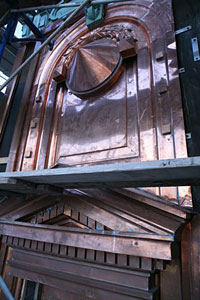
Photograph courtesy of Schtiller & Plevy
"I was a high school and college summer help employee," he says, "I had my aunt as the bookkeeper, and my grandfather semi-retired and reading the newspaper keeping his eyes half open to see what's going on. My uncle was running the outside, and my father was running the Estimating Department."
It looks like the business will remain in the family, as Plevy's son loves working with metal and will soon graduate from the industry's apprenticeship program. Growing up with the business instilled a passion in Plevy that has never left him.
"A lot of people ask me what I do for an occupation, and I tell them literally, I go around to different historic buildings, I fall in love with the building, and put the price together, then have my men work on it," he says. "And then, I take a lot of pictures to make sure they're doing the work properly."
That meticulous attention to detail was born very early. He estimates that his family had at least 50 books about the industry.
"My father said, 'Read those books, look through those books, understand those books, and you'll learn the industry,'" recalls Plevy. That instruction, coupled with the experience he received on the job in the years that followed, made him highly qualified to assist the Sheet Metal and Air Conditioning Contractors National Association (SMACNA) in rewriting the 4th, 5th, and 6th editions of the Architectural Sheet Metal Manual, which is the bible of the industry. He served on the task force for each edition and chaired for the 6th edition, which brings together the best of the best in the unionized sheet metal industry.
While Plevy wrote a few chapters for the 6th edition, he had the biggest impact on the 4th edition.
"For the 4th edition, I literally one night in between our meetings, ripped the book apart and reorganized it the way I thought it should be organized," he says. "More or less, the group said, 'Yeah, you're right. It makes more sense now rather than the way it was.'"
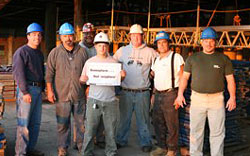
Photograph courtesy of Schtiller & Plevy
One of the perks of Plevy's business is befriending and learning from others in the trade. That includes the company that restored the Statue of Liberty. That company had made two sets of the Statue's lips and ring toe (each about 4-feet wide), so when Plevy's daughter was in kindergarten, he was able to get those pieces for her "Show & Tell" presentation. Everyone in the school crowded into the classroom to see them.
Even though metal work is only part of the restoration work performed by Schtiller & Plevy, Larry Plevy has a particular fondness for copper.
"The color and the feel of copper is something that I'll never forget for the rest of my life," he says. He can bend a piece in his hands and immediately know how thick it is. Someone once told him that his is a noble profession. "Yes, it is," he answers.
Resources:
Also in this Issue:
- Schtiller & Plevy: A Commitment to Restoring History
- Gregory Nangle: Outcast Studios
- The Movement of Bronze: Andrew DeVries
- Capturing the Wild West Through Bronze
- MET Features Work of Renowned 19th-Century American Sculptor and Metalist Augustus Saint-Gaudens