The Patriotic Roots of Valley Bronze of Oregon
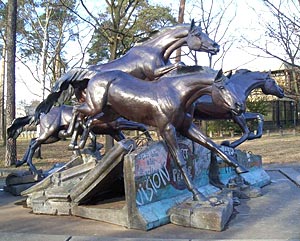
Photograph by Mutter Erde
If you have occasion to visit the National Archives Rotunda in Washington, D.C., pay attention to the cases containing the Constitution, the Declaration of Independence, and the Bill of Rights. They are brand new - all recently created by Valley Bronze of Oregon. This company can do everything from design, casting, fabrication, and machining to engineering and installation - whether for a small sculpture, a large monument, a cathedral door, or a staircase.
You will also see Valley Bronze's work at the National World War II Memorial and the spiral staircases at the new U.S. Capitol Visitor Center. In 2004, the company won an excellence award from the Washington, D.C. Building Congress for its work on the WWII Memorial and was presented with a craftsmanship award last March for structural steel framing work in the Capitol Visitor Center.
Besides their work in Washington, Valley Bronze created sculptor Walter Matia's Spirit of the Bull monument for Houston's Reliant Stadium and artist Veryl Goodnight's sculpture The Day the Wall Came Down, depicting the Berlin Wall, which was given to Germany as a gift from the American people. The original resides at the Alliierten Museum in Berlin, and an exact copy is displayed at the George H.W. Bush Presidential Library in Houston. Another example of the company's ornamental work can be seen in the bronze bas relief cathedral doors at Our Lady of Lourdes Cathedral in Spokane, Washington, which were designed by internationally renowned sculptor Dorothy Fowler.
Started strictly as a casting facility in 1982, Valley Bronze is now run by David and Christine Jackman, who got into the business by accident. David was a lawyer, and the company was his only corporate client. When the owner at the time wanted out of the business in the late 1980's, the Jackmans seized the opportunity. Today, Christine is the company's President, and David is the CEO.
The company is located in the rural area of Joseph, Oregon, where it is one of the county's largest employers with a staff of about forty. Nearly all of its employees were trained by the company, and some have become adept at design.
"Everyone on site," says Christine Jackman, "is an artist themselves to do this kind of work." If someone needs a complicated sculpture or monument, however, the company will commission an artist to design the work, and Valley Bronze will complete the piece at the foundry, as well as install it on site.
One of the company's main services is casting for artists, which sometimes involves taking a small scale sculpture and creating a faithful "point-up" larger-than-life-size version. Artists bring in their originals, whether clay, wood, or stone. Valley Bronze then makes a mother mold from the original, using coats of liquid rubber or silicon backed with plaster or fiberglass. Hot wax is poured into the mother mold, and a second ceramic shell mold is created by repeatedly dipping the wax duplicate into a vat of liquid slurry followed by coating the mold with silica sand. This takes a few days, after which the shell is fired in a kiln to melt the wax and harden the ceramic. When the wax has melted, the mold is hollow and ready for the molten bronze to be poured into it. After the bronze has cooled, the ceramic shell is broken away, and any additional pieces are welded to the metal to complete the sculpture. The work must then pass the company's stringent quality controls to make sure it matches the original sculpture before the final patina process is begun.
Valley Bronze is sometimes called upon for especially challenging projects. The skill required for the National Archives case renovations was so great that the company's employees had to design and build new tools. Two other companies were hired before Valley Bronze, but due to the complexity of the project, the cases produced by the other companies were unacceptable. The old cases from the 1930's had a 30-foot long classic leaf pattern that needed to be duplicated.
"We had to have those sent off and digitally enhanced because they weren't good anymore," Christine says. "And then, it's been a combination of casting, machining, and fabricating."
The finished product is a credit to the company's ingenuity and determination to find a way to produce excellent work no matter the circumstances.
"We pride ourselves on our quality," Christine says. "We like people to come back."
Resources:
Also in this Issue:
- Public Sculpture Series Bronzes Notable TV Icons
- Yoshitomo Saito: The Bronze Weaver
- The Patriotic Roots of Valley Bronze of Oregon
- The Not-So-Lost Art of Lost Wax Casting
- Stellar Collection of Renaissance Sculpture Promised to National Gallery of Art by Robert H. Smith