Contents
Typical Forms and Sizes
90-10 and 70-30 copper-nickels are available in a wide selection of product forms. Common production limits on the sizes of these materials are shown below. This is a guide to what is commonly made to order. It may also be possible to make material outside these sizes by arrangement with the supplier.
Form | Sizes | |
---|---|---|
Metric | US Customary | |
Plate | up to 3000 mm wide, 10 to 150 mm thick | up to 10ft wide, to 6" thick |
Clad steel plate | to order only | to order only |
Sheet & Strip | up to 2000 mm wide, 0.2 to 10 mm thick | up to 6ft wide, 0.008" to 0.25" thick |
Seamless Tubes: | ||
|
6 to 420 mm OD, 0.8 to 5.0 mm wall thickness | 0.3" to 16" mm OD, 0.03 to 0.2" wall thickness |
|
8 to 35 mm OD, 0.75 to 2.0 mm wall thickness | 0.3 to 1.5" OD, 0.03 to 0.1" wall thickness |
|
6 to 22 mm OD, 0.5 to 3 mm wall thickness | 0.25 to 1" OD, 0.02 to 0.12" wall thickness |
Tubes - longitudinally welded | 270 to 1600 mm OD, 2.0 to 10 mm wall thickness | 10 to 63" OD, 0.1 to 0.5" wall thickness |
Fabrications | by arrangement | by arrangement |
Wire | all common wire and wire mesh sizes | all common wire and wire mesh sizes |
Rod & Section | all common sections up to 180 mm diameter | all common sections up to 7" diameter |
Welding Consumables | all common sizes | all common sizes |
66-30-2-2 Cu-Ni is normally available as seamless tubing only. |
Fittings
Copper-Nickel fittings are not standardized in EN, ISO for the metric sizes. Therefore, in practice, EEMUA and DIN standards are the common standards used by customers worldwide. Also, DIN standards for shipbuilding have not been replaced by EN or ISO.
Read more about fittings in seawater system design.
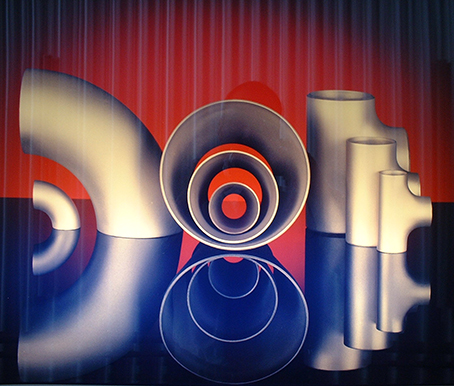
Product Supplier's List
Find Product Suppliers by specifying alloys and forms they carry.
Castings
In many engineering situations, copper-nickel systems have cast valves and pumps in nickel aluminum bronze. However, satisfactory complex castings can be made with copper-nickel alloys, provided that foundry practices are good. The 90-10 composition has a lower melting and pouring temperature than the 70-30 alloy. Normally, extra alloying elements are added to improve properties.
The introduction of electric furnace melting in foundries led to enhanced interest in cast 70-30 alloys, particularly the alloy containing around 2% Cr. The UK Navy developed such an alloy as Defense Standard 02-824 Part 1. This alloy has improved resistance to impingement corrosion. For other cast alloys and their designations, see: Copper-Nickel-Alloys: Properties, Processing, Applications.
Since these alloys have tight limits on impurities, only certified ingots are used. Electric melting practices attain the correct melting temperature within a reasonable time and provide cleaner furnace atmospheres that avoid contamination and gas pick-up. They are only available from specialty castings suppliers.
Product Standards
The table below covers American (ASTM), European (EN - replaces all previous national standards) and International Standards (ISO).
Standards | Applicable Standard Numbers | ||||||||
---|---|---|---|---|---|---|---|---|---|
Composition | Plate | Sheet | Strip | Tube | Rod | Wire | Forgings | Castings | |
ASTM | 122 171 |
122 | 122 | 111 359 395 466 467 469§ 552 543 608 |
122 151 |
369 505‡ |
|||
EN | 1652 1653 |
1652 1653 |
12451 12449 |
12163 | 12420 | 1982 | |||
ISO | 429 | 1634 | 1634 | 1634 | 1635, 16362 |
1637 1639 | 1638 | 1640 | |
‡ 70-30 alloy only § 90-10 alloy only |