The torch had been a problem for years. Thanks to an unfortunate redesign of the original and a lot of tinkering, it was the Lady's weakest point. Bartholdi's flame was solid copper with gold leaf. Later, someone thought it would be nice if the flame were lighted from within, so it was flattened and pierced with portholes.
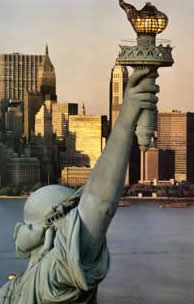
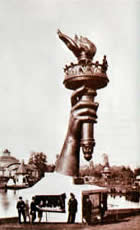
When that didn't work, architect Gutzon Borghum (the guy who did Mt. Rushmore), used copper bands to support thick glass. This, more or less, worked as a beacon …
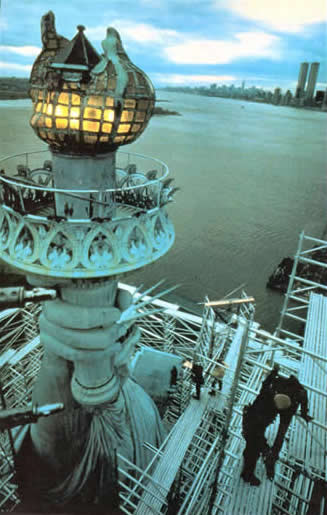
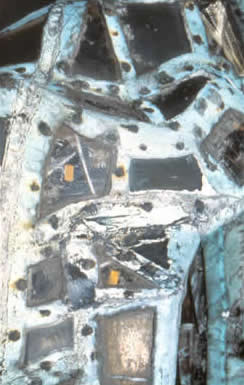
… but leakage threatened the upraised arm and moisture ran down the torch spreading corrosion through the interior and filling the pendant at the bottom with what another architect called "primordial soup."
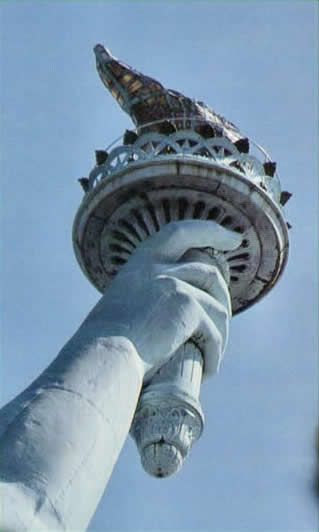
The restoration team deemed reconstruction of the torch too difficult and dangerous. So, instead, they rebuilt it to reflect the original Bartholdi design. A new, solid-copper flame was fashioned from copper sheet and hammered into shape.
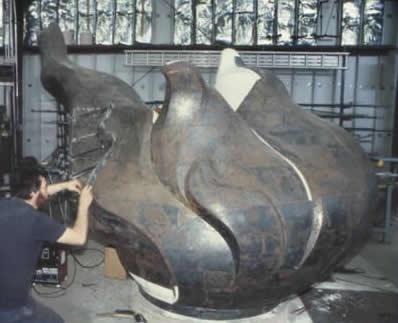
It was then gilded - first by mildly etching the copper surface and coating it with layers of varnish, and then placing gold leaf on the top layer while it was still tacky. The pendant was not rebuilt, but it did get modified with a weep hole. The flame now glitters from reflected light, rather than an internal light.
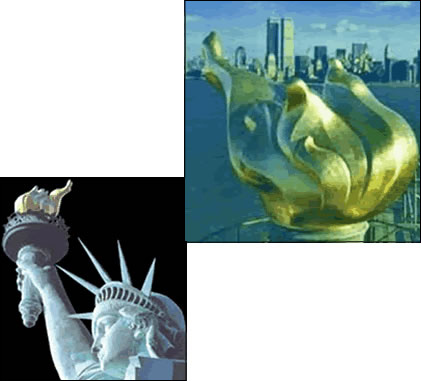
Armature Repair
The biggest problems came from corrosion of the iron bars. Much was from entrapped moisture, but most was from galvanic corrosion. As we had mentioned before, the Americans had used a layer of shellacked asbestos cloth between the copper saddles and the iron. Great idea, and it worked …but only for so long.
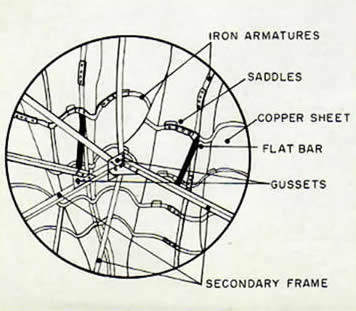
Over the years of flexing and aging, the shellac dried up, and the asbestos became dry and porous. Now, what was left of the protective layer absorbed moisture and actually promoted electrolyte contact and galvanic corrosion.
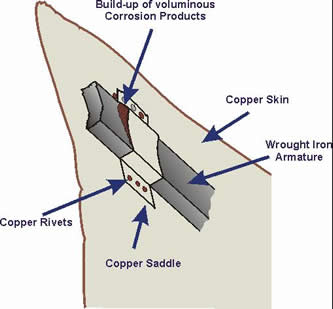
The accelerated corrosion of the iron caused it to swell and distort. That, in turn, caused the saddle rivets to be pulled through the copper skin in many places … actually, about 600 of the saddles were affected. This condition was rapidly worsening and was a main reason to undertake the restoration of the statue.
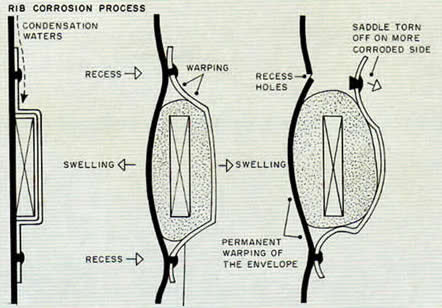
So how does one fix this problem? First, the engineers decided that the puddled iron in the superstructure had to be completely replaced. For the rigid flat bars spanning the armature and the secondary frame, they chose Ferralium 225.
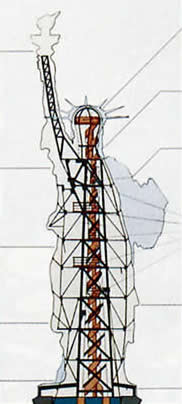
For the armature, the first consideration was to mitigate galvanic corrosion with the copper skin. To determine this, several candidates were tested at the La Que Corrosion Lab in North Carolina. Tests were carried out using four candidate armature materials. They were mated to a C11000 copper sheets and saddle forms with copper rivets:
- C61300: Aluminum Bronze
- C71500: Cupro-Nickel
- 316L: 531603 Stainless Steel
- F-4883: Ferralium
- (Cold-rolled steel was used for comparison.)
After 4-1/2 years (equivalent to a 100 years of exposure), the choice was 316L steel. It has the best combination of corrosion resistance and physical properties - elasticity, weight, strength, ductility and fabricability.
316L has a low enough yield strength, so that it could be cold-worked to conform to the contours of the copper skin. The bars were annealed with a direct-current technique to eliminate any stress corrosion problems. Also, its thermal expansion characteristics are better matched to the copper than the puddled iron, so movement in the saddle would be reduced. To help further reduce friction problems, the stainless bars were coated with Teflon®.
Now, without any isolation layer to restrict observation, the joints can be easily inspected, as they are annually, and maintained … if it ever becomes necessary.
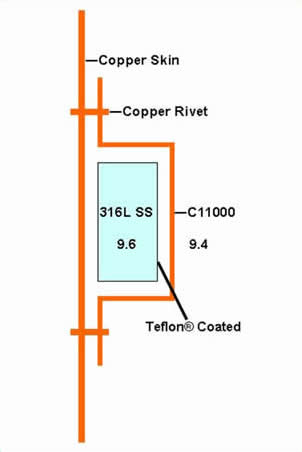
(The numbers 9.6 and 9.4 in the above armature detail refer the coeefficient of expansion of stainless steel and copper respectively.)
Ten years after the restoration, in 1996, the inspection team noted that the corrosion problems had been corrected, that the installation has remained corrosion-resistant, and that it is doing very well in its second century of life.