In 1965, CDA blazed a trail in statistical information with the launch of its computerized Copper Technical Data Center, making available for the first time in any information system the computerized retrieval in extract form of actual graphs, tables and related visual material to guide engineers in selecting and using copper, brass and bronze. And this was more than 30 years before the blossoming of the Internet. Known today as the Copper Data Center, it provides computer access to the worldwide technical literature on copper and its alloys with the click of a mouse. Reports are indexed and evaluated by expert engineers.
So much for the '60s. With its position well established as a proactive generator of ideas, a creator of workable prototypes and an information source, CDA moved into its second decade eager and ready to build on copper's image. Home is where the heart is, yes, but as these professionals knew, it's where the copper metals keep that heart beating.
Welcome to the "Decade 70 House of New Concepts," conceived and built in Houston in 1970 as a showcase for new products and innovations in building construction. It opened to great fanfare in 1971 at the National Home Builders Show, where builders, architects and other attendees viewed its two new copper roofing systems; bronze floor tiles; roll-formed bronze sliding glass doors and windows; and copper-clad walls, ceilings and countertops.
Four years later, CDA responded to the front-burner environmental issues, including high energy costs, that were tailor made for copper with its second prototype house, "Decade 80 Solar House" in Tucson, Arizona. While it included prototype decorative products like a thin-line architectural bronze door and window system, copper-clad furniture, solid copper and brass wallpaper and other art elements, this house was all about solar power. The sun would provide up to 75% of its cooling and 100% of its heating.
A few years later, CDA built the "Sun-Tronic House" in Greenwich, Connecticut. It further advanced the applications of solar energy, including solar power, and it demonstrated myriad copper and copper alloy applications in the home.
The electric car continued to occupy CDA professionals, and four more models were produced between 1970 and 1975. Copper Electric Van III, was designed by CDA from the ground up. Its electrical uses included bus bars, motor, cable, switch components, commutator, windings and wiring. Non-electrical uses of copper alloys included brake drums, brake tubing, hardware and air lines.
The last of the prototypes was the Copper Electric Town Car. The two-seat hatch-back model had energy fuel costs of 2 cents to 3 cents per mile, with energy power supplied by 18 6-volt lead-acid storage batteries that could be recharged overnight in the user's garage. The car's range at cruising speed of 40 miles per hour and top speed of 55 MPH was 120 miles.
Copper-nickel alloys wrote another success story, this time on the water. The Copper Mariner, a 67-foot shrimp trawler, was developed in 1971. The 90% copper, 10% nickel alloy, known as Copper Alloy 706, resists hard-shell marine fouling and corrosion, is weldable and cost-competitive. The hull never needs to be painted or scraped, and the boat moves through the water with less drag. Fuel savings are considerable, and savings add up to more fishing time. After four years of testing alongside a steel-hulled boat, the Copper Mariner showed dramatically lower operating costs, averaging 11.6 gallons of fuel consumption per hour vs. 13.7 gallons. The steel-hulled boat was scraped and repainted eight times. Fifteen years later, Copper Mariner was still shrimping, maintenance-free, for the Nicaraguan Fisheries Department, and may still be doing so today.
In 1972, prototypes demonstrated the effectiveness of Alloy 706 sheathing for marine pilings. The alloy extended the life of the pilings by 20 years, protecting against marine borer attack. Moreover, the copper ions released in the seawater reduced the growth of fouling organisms like barnacles. Copper floats and copper mesh extended netting life for material used underwater to fence in the seafood "crop."
Once that seafood came to market, home cooks could learn about "Cooking with Copper," CDA-sponsored classes conducted by prominent chefs using copper cookware. CDA prepared booklets highlighting these recipes.
Back on the construction front, the all-copper "Life Safety" sprinkler system was designed for hotels, office and apartment buildings and nursing homes, places with high density populations compacted in small spaces.
Radiators for the automotive industry long had been a dominant copper and brass market. But as aluminum fabrication technology revved up, the light metal launched its own challenges to the red metal family. The battles were heated as the decade wound down, with costs driving market share. Both industries used the cost factor to tell their story, along with technology and performance. CDA's program of improving the efficiency of radiator components and radiator design, stressing superior heat transfer capability and corrosion resistance, held off against aluminum's market encroachment for nearly 15 years longer than occurred elsewhere in the world.
Indeed, in the 21st Century, defense of the copper and brass radiator remains a high-priority project, through engineering development of new machinery to produce radiator tube from thin strip and the development of new radiator solders that are stronger, lighter and less costly. That long-term effort is manifested today in the CuproBraze™ process developed by the International Copper Association for manufacturing all types of heat exchangers.
There are so many little dyings,
it doesn't matter which of them is death.
- Kenneth Patchen -
The 1980s began with recession. As the copper price tumbled and mines, smelters and fabricating plants were closed, laying off thousands of workers, CDA, too, faced a tremendous challenge. For copper, the recession was compounded by the flood of lower-priced imports of brass mill products to the USA. As original equipment manufacturers-the users of copper and brass products focused on the bottom line, and the U.S. metals industry grappled with the trade issue. Developing countries learned their lessons well, upgrading their own marketing strategies to compete head-to-head with the industrialized world. But there is no question that the import phenomenon, one that remains an ongoing issue-critical in economic slowdowns-was at the crux of the problem.
The mid-'80s may have been the Go-Go Years for Wall Street brokers, but for copper, it was Gone-Gone. Metals producers were operating at or below 50% of capacity. Brass mills, despite paring costs to the bone, were unable to fend off the offshore and economic onslaught, and their ranks shrunk. The famed Connecticut Brass Valley was relegated to the history books as mills shut their doors, falling like dominoes.
Add to this the ongoing competitive battle with aluminum for dominance in automotive radiators and a variety of refrigeration applications. At the same time, the competitive battle on another front opened, with the advent of fiber optics and its penetration into the communications field.
The irony, of course, was that a vast new market was evolving for copper, the flourishing communications business sparked by the Age of the Internet. Every home would have at least one computer. Demand for copper wire in landline applications, however, was being challenged by fiber optics, a battle that would continue into the next decade and beyond.
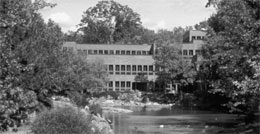
Despite its proactive position, defensive strategies were in the forefront. Seminars across the market spectrum continued to endorse the red metals, and technology to develop better materials combining high conductivity, improved resistance to corrosion and other critical properties topped the agenda. For copper, this was the age of alloys.
But, the U.S. industry was still being challenged by international research and development issues. There was a critical need to unite U.S. and international efforts to support and advance the common good. More copper usage.
Architectural usage became a major market. The wave of restoration concurrent with the need for more physical space created a new front for copper's technical corps. A newly established market development program for architectural copper saw its first crowning achievement in the restoration of Ellis Island and the Statue of Liberty, two beacons of copper in New York Harbor. These national treasures not only made visible and practical use of the red metal and its alloys, they helped usher in a new era of international cooperation that was to open yet another chapter in the association's history.
Under George Hartley's leadership, CDA demonstrated the possibilities for copper, building on each technical achievement with another, each prototype taking copper applications to a new level. The foresight illustrated in the fields of solar energy and electric vehicles was clearly ahead of its time, and its advanced technological work laid the groundwork for 21st Century needs. Hartley retired in 1990 at a turning point for copper, one with new challenges, many unknown.
The farmer and the cowman should be friends.
- Rodgers and Hammerstein -
Robert M. Payne took the CDA helm in 1990. The association was at a crossroads. Economic issues, market cyclicality and the consolidation of the brass mill industry had taken their toll on membership. The year before, the International Copper Association had been formed. It was a restructuring of INCRA, the research entity, and had a charter to develop copper markets globally. Now CDA and ICA had to forge a working relationship. Barriers needed to be broken down and cooperation instilled in its place on a level never before seen in the industry.
Payne was named president, and he set out to restructure the CDA, marshaling the experience he had garnered at Revere Copper and Brass Inc. Payne's career at Revere had run the gamut from sales and marketing to management. When an executive buyout failed, he left the company with more than 20 years of service under his belt to work as a consultant, restructuring ailing firms.
Now he applied those talents to the industry that had nurtured him professionally. He put in motion a series of fundamental changes. CDA was a business, and more than ever in its history, that is how it operated. The days of prototype promotions pulling the carriage were over.
Association finances and program evaluation became front-burner items. Concern for cost-effectively increasing copper consumption shared priority with new technology, marketing and education programs. He ushered in a pragmatic approach to influencing important markets. Electrical markets, for example, which had been on the back burner, except for some advertising, now received major attention. New programs addressing all major markets had to pass the tonnage test. Being sexy wasn't enough.
This centering enabled the association to recognize the need to expand its membership and refocus some of its energy and budget to new areas, eliminating others and putting a fresh focus on still more. Markets important to its membership base were emphasized and the member companies perked up. Product councils were formed with decision power. Getting members in the same business together on common issues made them more committed, more actively involved.
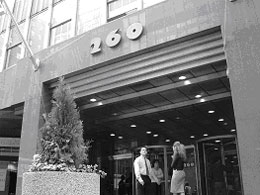
Payne brought together companies from all sectors of the industry, enlisting producers and fabricators to share in the financial, political and creative contributions needed to bring CDA full circle. Under his leadership, CDA established a strong working relationship with ICA. Indeed, they share office space on the 16th floor of their Madison Avenue headquarters in New York. They became united in a common goal-promoting the use of copper and its alloys-while continuing to tend to the needs of their respective constituencies.
Payne reinforced the need for education among producers and consumers of copper. He reorganized the association to better reflect the unique demands of each sector, each with a technical support presence. There was new emphasis on the people who make the association work. Members came to know and work with the entire professional staff. Meanwhile, the association's pre-eminent position in the field of market data was expanding. The Internet and the CDA Web site became crucial tools in disseminating its message. Technical publications were enhanced by more non-technical information, making it easier for the non-professional to learn copper's story. The result was growth across the board.
These changes took time to institute. Executives who lived in their own respective corporate cultures began to know and appreciate CDA, the business entity. CDA staff, unfamiliar with this management style, underwent their own learning experiences.
Bottom line: It worked. The association's ability to adapt to change was smoother. A streamlined, more focused operating structure enhanced responsiveness to the professional users of copper as well as general dissemination of information. And the bumps in the road were easier to navigate.
When Payne chose retirement at the end of 2000, a fresh challenge surfaced, finding the right person to continue the system he had put in place. As with any corporation, an executive search was launched, And at the end of the day, the CDA did not need to look beyond its own Madison Avenue office.
Open a new window, open a new door…
- Jerry Herman -
Andrew Kireta had spent 21 years with the association when he was tapped for the top job. Trained in the mechanical trades, his career began in the piping industry with United Association Local 520. He was field superintendent for G.R. Sponaugle & Sons of Harrisburg, Pa. In 1979, he joined CDA and served as Northeast regional manager for 15 years, was then appointed national program manager and, in 1997, vice president for tube, pipe and fittings. At CDA, he made his mark as director of the North American Plumbing Tube and Fittings Initiative for the USA and Canada, a market promotion and development effort aimed at increasing and improving the use of copper and copper alloy tubular products in building and construction. He developed the Builder Satisfaction Program - a marketing support effort.
As national program manager and based in Pennsylvania, Kireta headed a five-member team of regional managers who provide copper-plumbing-related technical support, training and assistance to builders, remodelers, architects, plumbing contractors and engineers across the United States. The team addresses inquiries and issues in the field, serving five geographic regions.
He is the first "home-grown" leader of CDA, learning and growing with the association as it evolved to better serve its member companies and the users of copper and brass. For a new century, a new age, he welds a wealth of history with new demands of a new age.
How new? Today, CDA holds symposia on health and safety that reach out to pressing issues and address more than the traditional agenda. The 2002 meeting brought together government and private sector speakers to examine new challenges such as safety precautions for drugs, terrorism and violence in the workplace, along with more traditional topics like beryllium health and safety.
For Kireta, training and education are the keystones to the future of the industry. That's how he plans to deal with defending, maintaining, growing and fostering new markets. Programs for the elementary grades will supplement well-entrenched and well-regarded university level programs. Sheet metal contractors have now joined the ranks of plumbing contractors who receive on-site training programs stimulating the use of the red-metal and ensuring its proper installation. But, it doesn't stop there.
Issues critical to fabricator members who must deal with threatened or highly regulated markets have been the focus of two symposia Kireta has instituted. The first dealt with plumbing tube corrosion; the second with California's Prop 65 and NSF 61, onerous trends and regulatory requirements that carry the potential to strain the member company resources in their manufacture of traditional copper products. If you're not watching your backside, it's easy to get left behind.
Market intelligence has been raised to a new level. In-depth market studies, public forums on market trends and private Web site reportage on competitive products now complement the world's most comprehensive data collection operations in the copper industry.
Exciting new prospects with potentially heavy market impact are on the horizon. A die-cast solid copper motor rotor promises to raise the bar on advancing electrical energy efficiency for motors-and raise copper use worldwide. Research on semi-solid metal casting should bolster brass products. And, studies on the incredible effects of copper on the dreaded <i>E. coli</i> bacteria bode well for broad new applications of copper alloys in the food processing industry. It's a brand new century for man's oldest metal. And, there's more to come.
The catalyst for these new ventures and renewed emphasis on membership involvement is teamwork. Teamwork on staff-at all levels-teamwork with member companies, with sister copper associations around the world, with industry-allied organizations, with industry professionals, with engineers, contractors and end-users. That's the way Kireta ran his regional managers, and that's the way he's running the association. There's a healthy cross-pollination of ideas. Most importantly, there are new ideas, ones that are forging new and expanded ground for a venerable group of companies.
Kireta identifies one solid ground for expanded attention-retrofit. New construction, commercial and residential, has been the mainstay of the industry for generations. But, existing structures far outweigh the numbers coming onboard. Market trends show increasing emphasis on renovation and retrofit. CDA plans to meet that opportunity.
Look at the CDA-related Web sites for a view of today's association. Copper in Your Home covers the spectrum of consumers, including features like "How to Rewire" and " Soldering School." Environment, health and nutrition capture a spectrum of information, from the concerns about bodies of water, the needs of plants and animals, how to enrich copper-deficient soils, to the role of copper for infants and nursing mothers, and copper's antioxidant properties in protecting against osteoporosis and arthritis. Beyond the traditional food groups, look to oysters and chocolate to add copper, as well as zip, to your diet.
Our site amasses more than 20,000 pages of technical, practical, pertinent information for myriad users and their myriad applications. It's a compilation of the history, knowledge and experience of the association and a testament to the thoroughness and professionalism of its staff and member companies.
Day by day, By day by day.
- Stephen Schwartz -
As CDA completes 40 years of representing the copper and brass industry's commitment to growth through research, development, marketing and education, it can look back on a proud heritage born from the ashes of war and its ancestor, CABRA. Every step along the way has led to a new chapter in the industry's evolution, through war and peace, depression, recession, recovery, prosperity, corporate expansion and retrenchment. Today is not the best of times for the industry, nor is it the worst. Today's CDA is dealing with the present and is girded for the future. Its intrinsic value is in its people-staff, members and associates. It's a value that's here to stay and to ensure its future, day by day.
Afterword
There is no way to capture all of the many people, events and accomplishments that have made CDA what it is today. This narrative is merely a glossing of some of its highlights and may contain errors and certainly many omissions. For that we apologize. What this narrative does contain is homage to the member companies and professional staff who have brought CDA to the stature and recognition it enjoys today-a position of which each of us can be justly proud.
Previous...